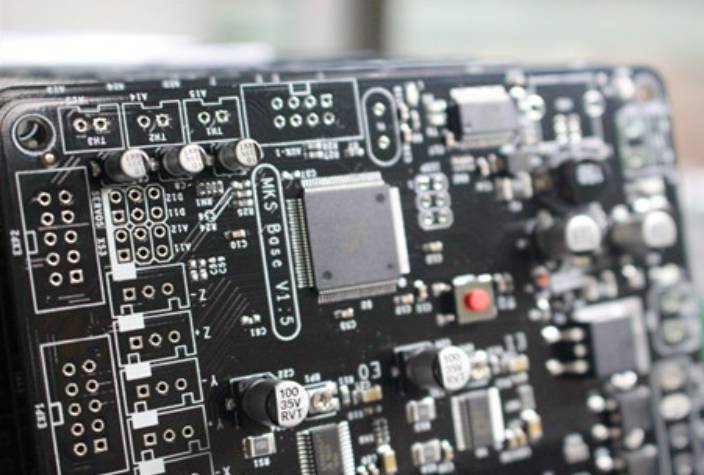
1. printed circuit board lamination
Laminating parameters may vary from company to company. in order to ensure the full flow of the resin and make the binding force good, it requires a low heating rate of the sheet material (1.0-1.5℃ / min) and multi-stage pressure coordination, and in the high temperature stage, it requires a longer time, 180℃ to maintain more than 50 minutes. The following is a group of recommended platen program Settings and the actual plate temperature rise. The bonding force between the copper foil and the substrate is 1.ON/mm. After six thermal shocks, there is no stratification or bubble phenomenon in the plate.
2, drilling machinability
Drilling condition is an important parameter, which directly affects the quality of hole wall in the process of circuit board machining. As P and N series functional groups increase the molecular weight and enhance the rigidity of molecular bonds, halogen-free copper clad plates also enhance the rigidity of materials. At the same time, the Tg point of halogen-free materials is generally higher than that of ordinary copper clad plates, so the drilling effect of ordinary FR-4 drilling parameters is generally not very satisfactory. When drilling a halogen free plate, make some adjustments under normal drilling conditions.
For example, if the company uses Shengyi S1155 / S0455 core board and PP four-layer board, its drilling parameters are not the same as the normal drilling parameters. When drilling halogen-free plate, its speed should be faster than the normal parameters increased by 5-10%, and the feed and rewind speed is reduced by 10-15% than the normal parameters, so that the drilled hole roughness is small.
3, alkali resistance
Generally, the alkaline resistance of halogen-free plates is worse than that of ordinary FR-4. Therefore, special attention should be paid to the etching process and the rework process after welding resistance. The soaking time in the alkaline film removal liquid can not be too long to prevent the appearance of white spots on the substrate. In our actual production, we have suffered a loss: the halogen-free plate after welding resistance and curing needed to be backwashed due to some problems, but the backwashing was still done in the way of ordinary FR4 backwashing, which was soaked in 75℃ temperature and 10% NaoH concentration for 40 minutes. As a result, all the substrate white spots were washed, and the soaking time was reduced to 15-20 minutes. This problem no longer exists. Therefore, it is better to make the first plate first for rework resistance welding of halogen free plate, so as to obtain the best parameters, and then rework in batches.
4, no halogen welding production
At present, there are many kinds of halogen-free solder ink introduced in the world. Its performance is not much different from that of ordinary liquid sensitive ink, and the specific operation is basically similar to ordinary ink.
5. Summary
Halogen-free PCB printed circuit boards can meet the quality requirements of PCB boards due to its low water absorption rate and the requirements of environmental protection. Therefore, the demand for halogen-free boards has been increasing. In addition, major plate suppliers have invested more funds in the research and development of halogen-free substrate and halogen-free PP. It is believed that in the near future, low-priced halogen-free plate structure will be put into the market immediately. Therefore, PCB manufacturers should put the trial and use of halogen-free boards on the agenda, work out a detailed plan, gradually expand the halogen-free boards in the factory possession, so that they go ahead of the market demand.