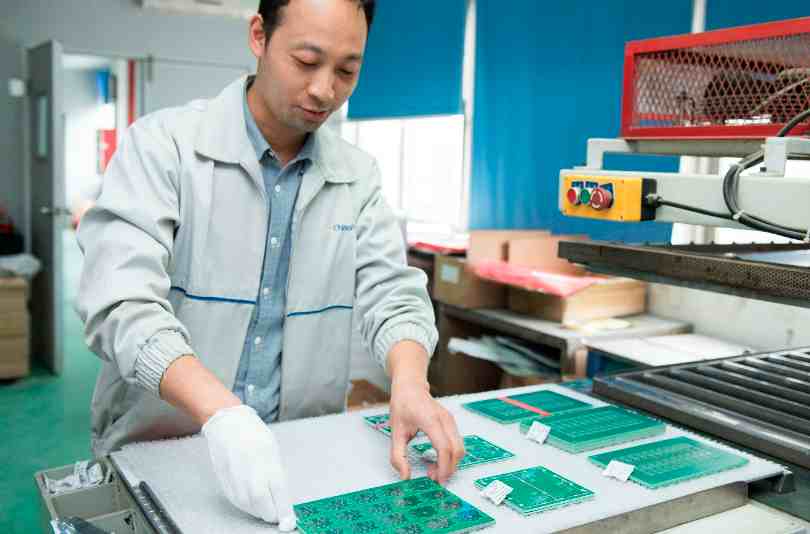
Q: What are the main and secondary reasons for the occurrence of vertical copper wire on the circuit board? What can be done to improve?
Answer: - Most of the reasons for the occurrence of copper wire in secondary electroplating are abnormal additives or copper tank pollution. As for why the pollution source or whether there is a problem with yao fluid, you must trace and discuss in detail. According to previous experience, secondary copper plating will dissolve more substances because the sensitive film is immersed in yao solution. Especially from the outside, the new yao liquid will change color quickly as long as it is used for a short period of time, which is a problem caused by the dissolving phenomenon of the sensitive film because these substances come from the sensitive material, so it is easy to stick to the tank wall after dissolving. If there are some polar polymers in these substances, it is easier to electroplate bonding between lines.
According to previous predecessors pointed out that this kind of copper wire will not be found in the internal section of any foreign body, which represents that the generation of copper wire should be temporary conductive material guidance, resulting in the subsequent copper growth and connected into a line of phenomenon, so it is necessary to regularly clear yao fluid and indeed clean the tank wall residue. Regular repreparation of the tank has become one of the important means to prevent such problems. Unfortunately, so far, there is no maintenance frequency for reference.
In the past, circuit board factories have lost a lot of money because of this problem, and after a period of improvement, they disappeared without knowing what changes to solve the problem. Active carbon treatment has not completely solved this problem, but there is a more obvious change in scrubbing tank wall, rearranging tank, which means that there should be foreign pollutants interfered with the process. Now many circuit board manufacturers have FTIR polymer analysis equipment, it is suggested that yao water pollution degree comparison can be carried out to monitor the change of organic content. Believe that different yao water system will still have differences, the past experience or can only be used as a mirror, the above information is Keyou circuit board production for reference only.
Circuit board hole copper uneven cause side thick side thin is what reason?
Q: circuit board hole copper uneven cause (one side thick, one side thin) why? What's causing the UNEVEN PLATING (pulsed plating is being used)? How can it be improved? Is the current related to the thickness of the plating and the width of the wire? What about relationships?
A: I do not know whether your electroplating equipment uses a single rectifier or a two-sided control design. If it is a single rectifier control structure, the electroplating current distribution will be directly affected by the contact resistance. If the hole is deep and the flow uniformity of the liquid is not ideal, the problem of uneven thickness of the single hole will be produced. In addition, I do not know whether you are talking about full plate plating or line plating. If it is line plating, it can only be said that uneven is inevitable, and the difference lies in what level the race range can achieve. Pulse electroplating belongs to alternating electroplating, which is highly sensitive to waveform. If the contact condition is not ideal, the problem of uneven left and right sides may also occur.
Electroplating uniformity is divided into large areas and small areas of uneven plating, uneven for large areas, the possibility of improvement is higher, but it is more difficult to improve local areas. In general, the problem of uneven plating is discussed, and the main consideration is the distribution of power lines. A power line, in the case of electroplating, is an imaginary path of charged particles. The factors affecting the distribution of these hypothetical routes include: anode configuration, anode and cathode distance, circuit board hanging mode, liquid mixing, circuit board swing, current density, type of gloss system, shield system design, etc.
These factors for large areas, moderate adjustment will be helpful, but for small areas, especially in line plating, because the distribution of copper surface has been irregular, and the cathode configuration and design is fixed, so the distribution of power lines is bound to produce mutually exclusive uneven distribution. At present, most of the more effective ways are improved by using lower current density and proper gloss system. Other mechanical designs should be adjusted appropriately by equipment manufacturers. There should also be room for improvement.
The current size is related to the plating area, which is called current density. The more uniform the current distribution, the better the plating quality, and the higher the current density, the shorter the time to reach the same copper plating thickness. However, high current density is often accompanied by the problem of electrical uniformity variation. How to strike a balance between production capacity and quality is a problem you must think about. In general, if the line is thinner and the copper surface is unevenly distributed, then theoretically it means that the current density can be used is lower.
Early circuit board manufacturers in the face of the problem of plating uniformity, there is another direct thinking is to increase the distance between anode and cathode, this treatment can reduce the power line repulsion to a relatively low level, is really helpful for plating thickness uniformity. However, this process consumes more energy and is not appropriate for pulse plating. For line plating, the dense line area will bear more uniform current, but in the independent line area (uneven density area) the current distribution will be relatively poor, at this time if it is possible to increase some false points on the circuit board to disperse the current, otherwise the plating uniformity is bound to become relatively poor, the above information is made by Shenzhen Keyou Circuit Technology Co., Ltd. for reference only.