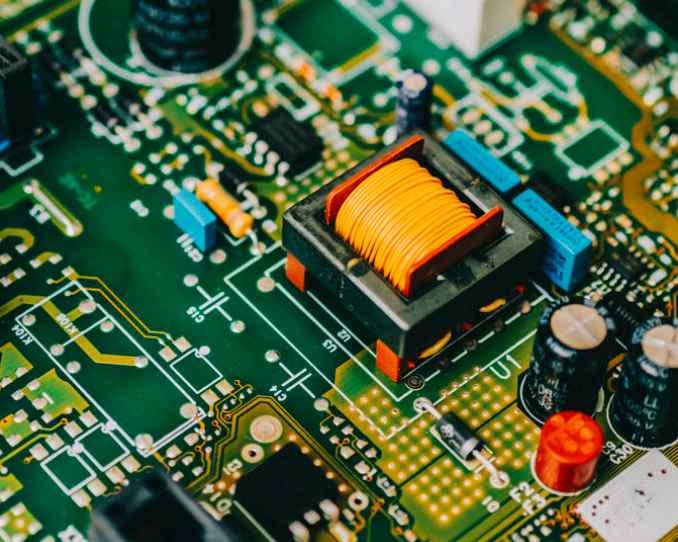
Today's mass-produced electronic hardware is manufactured using the well-known surface mount technique or SMT. Besides offering many other advantages, SMT still has a long way to go to speed up PCB production.
Surface mount technology
In essence, Surface Mount technology (SMT) takes the basic concept of through-hole manufacturing and continues to make significant improvements. No drilling is required for PCB boards when SMT is used. Instead, what they're going to do is use solder paste. In addition to increasing speed, this significantly simplifies the process. Although it is true that SMT mounted components do not have the strength of through-hole mounted components, they offer many other advantages that offset this problem.
The surface mounting technology goes through the following 5 steps:
1. PCB production - This is the actual phase of PCB production with solder spots
2. Deposit solder onto the pad to secure the assembly to the plate
3. With the help of the machine, place the component on the precise solder joint
4. Bake PCB to harden flux
5. Check the completed components
The reasons that make SMT different from through hole include:
(1) Through the use of surface mount technology can solve the widespread space problems in through-hole installation. SMT also provides design flexibility because it gives PCB designers free control to create dedicated circuits. The reduced component size means that more components can fit on a board and fewer boards are needed.
The components in the SMT installation are lead-free. The lead length of surface-mounted components is shorter, reducing propagation delay and packaging noise.
(2) Higher density of components per unit area because it allows components to be mounted on both sides
(3) It is suitable for mass production, thus reducing the cost
(4) Reduced size leads to increased circuit speed. In fact, this is one of the main reasons most manufacturers choose this approach.
(5) The surface tension of the molten solder pulls the assembly into alignment with the pad. In turn, this automatically corrects any minor errors that may occur in component placement.
(6) SMT has proved to be more stable under conditions of a lot of vibration or shaking.
(7)SMT parts are usually cheaper than similar through hole parts.
Importantly, SMT can greatly reduce production time because drilling is not required. Moreover, SMT components can be placed in the thousands per hour, compared to less than a thousand for through-hole installations. In turn, this results in the product being produced at the desired rate, which further reduces time-to-market. So if you want to speed up PCB production time, SMT is definitely the answer. By using manufacturing Design (DFM) software tools, the need to rework and redesign complex circuits can be greatly reduced, further increasing the speed and possibilities of complex design.
All this does not mean that SMT is without its own inherent drawbacks. SMT may not be reliable if it is used as the only fastening method for components facing a large amount of mechanical stress. Components that generate a lot of heat or withstand a high electrical load cannot be installed using SMT. This is because solder melts at high temperatures. Therefore, in cases where there are special mechanical, electrical and thermal factors that prevent SMT from working, it is likely that through-hole installation will continue. Similarly, SMT is not suitable for prototyping, as components may need to be added or replaced during the prototyping phase, and high-density circuit boards may be difficult to support.