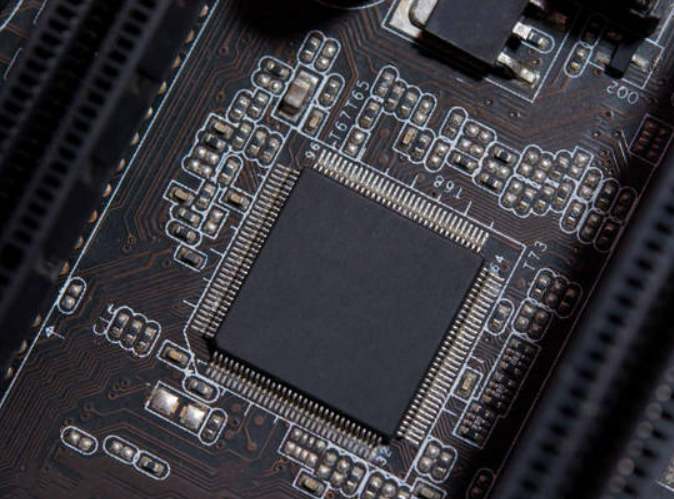
In our life, PCB (printed circuit board) can be more and more widely used, because its high reliability, high density, designability, productivity and other unique advantages are closely related, the demand for PCB both in output, performance indicators for many years to show rapid growth, accordingly, For PCB quality inspection also put forward higher requirements, the traditional inspection method can not meet the PCB industry's quality control requirements. As an important part of modern electronic equipment, PCB board is required to further improve the integration degree of PCB board due to the small size of patch components and high installation density. The quality of PCB directly affects the quality of the whole electronic products, so PCB detection equipment is particularly important and key. PCB testing is a kind of inspection method to find problems in time, but also a necessary means to prevent more defective products and reduce losses.
When testing PCB board, we should pay attention to the following points:
1. Test PCB board without causing short circuit between pins;
2. Pay attention to the insulation performance of electric soldering iron when detecting PCB board;
3. The internal resistance of the PCB test instrument should be large;
4. Pay attention to the heat dissipation of power integrated circuit when detecting PCB board;
5. Test the PCB lead properly
6. Check PCB board to ensure welding quality
7. Detection PCB board do not easily determine the damage of integrated circuit
8. Understand the working principle of the integrated circuit and its related circuits before testing the PCB board.
What should be done before PCB inspection? First, understand the working environment of the equipment, mainly considering the possible influence of external electrical parameters on the equipment; Ask what happens when the circuit board fails, and analyze the cause of the failure; Carefully look at the components on the circuit board to find out which components play a key role in the circuit board; We will take measures to prevent electromagnetic and electrostatic interference.
So, what are the common detection methods of PCB circuit board in the production process? In addition to the high cost of manual visual inspection, due to a long time of visual error, coupled with the reduction of PCB wire spacing and component volume, the requirements of manual visual inspection are also increasing, obviously, with the PCB output in the continuous increase, this method is more and more inappropriate; There is also a PCB board functional test, the functional system test is in the middle stage and the end of the production line, the use of special testing equipment to carry out a comprehensive test on the functional module of the circuit board, in order to confirm the quality of the circuit board. It requires special equipment and specially designed test flow, and is not suitable for most circuit board production lines because it is complicated to write functional test procedures. However, there is a kind of size detection that is relatively widely used nowadays, which uses quadratic image measuring instrument to measure hole location, length and width, position and other dimensions. As the PCB circuit board is a small, thin and soft product, it is easy to deform in contact measurement, resulting in inaccurate measurement. Therefore, the two-element image measuring instrument has become the choice of high-precision dimensional measuring instrument. The image measuring instrument of Sirui measurement can realize automatic measurement after programming, not only the measurement accuracy is high, but also greatly shorten the measurement time, improve the measurement efficiency.