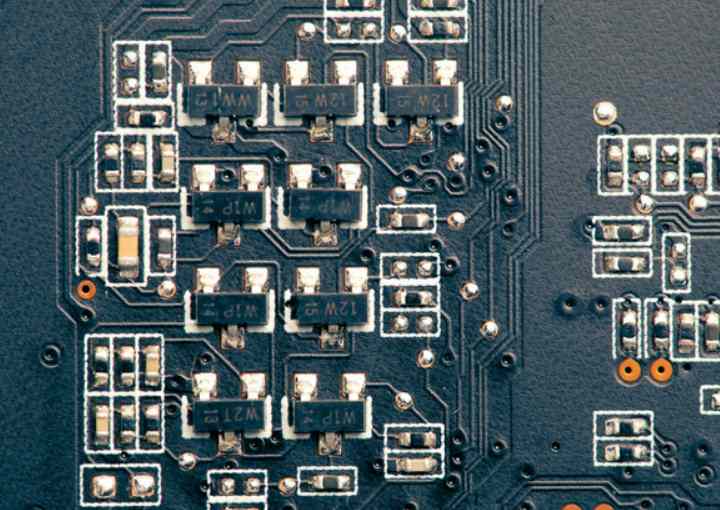
Printed circuit board (PCB), the development has been decades and hundreds of years of history, in the market common color PCB red, yellow, green, blue, black, but at present due to the production process and other problems, many lines of quality inspection process must rely on workers to see and identify, so in the strong light continuous exposure to the environment work, Relatively speaking, green is not harmful to eyes, so it is common to use green PCB in most manufacturers. The principle of blue and black is that they are respectively mixed with cobalt and carbon and other elements, with certain conductive properties, in the case of power is likely to short-circuit problems, and green PCB board is relatively very environmental protection, in the high temperature environment, generally will not release toxic gases.
Before the advent of the printed circuit board, the interconnection of electronic components relied on wires directly connected to form a complete circuit. Printed circuit board develops from single layer to double panel, multilayer board and flexible board, and continuously develops to high precision, high density and high reliability direction. Secondly, because PCB surface needs welding components, it requires a part of the copper layer burst
Exposed to the surface for welding, these exposed copper layer is called the pad, pad is generally rectangular or circular, small area. If the copper on the pad is oxidized, it is not only difficult to weld, but also increases the resistivity, which seriously affects the product performance. So engineers came up with all sorts of ways to protect the pad. Such as plating the inert metal gold, or coating the surface with a layer of silver through a chemical process, or coating the copper layer with a special chemical film to prevent contact between the pad and the air.
Therefore, the exposed pad on the PCB, the copper layer is directly exposed, this part needs to be protected to prevent it from being oxidized, from this point of view, whether gold or silver, the purpose of the process itself is to prevent oxidation, protect the pad, so that it can ensure the yield in the following welding process. The PCB is also said to contain a number of precious metals. In daily life, the average smart phone used by each of us contains 0.05g gold, 0.3g silver and 13.6g copper. The gold content of each laptop computer is more than ten times that of mobile phones. In fact, the precious metal plating material is not only the key material for the manufacture of printed circuit boards, but also the important material for realizing the excellent performance of chips. For example, the pins and lead frames used in the chip connection are almost coated with silver, and the electrode materials of the chip, the coating of the integrated circuit board wire, the LED light-emitting chip, etc., also need to be processed by the plating process of gold, platinum, silver and other precious metal plating materials. It can be said that the development of the integrated circuit industry in our country also couldn't leave the support of precious metal electroplating materials.
However, the use of different metals will require the storage time and storage conditions of PCB used in the production factory. Therefore, many domestic PCB manufacturers generally use vacuum plastic sealing machines to pack PCB before PCB production is completed and delivered to customers to ensure that PCB does not occur oxidation damage to a large extent. And in the components on the machine before welding, circuit board manufacturers also need to detect the oxidation degree of a PCB, eliminate oxidized PCB, to ensure the yield. When consumers get the circuit board, it has been tested, even if the oxidation after a long time of use will almost only occur in the insertion and removal of the connection part, and on the welding plate and have been welded components, there is no impact.