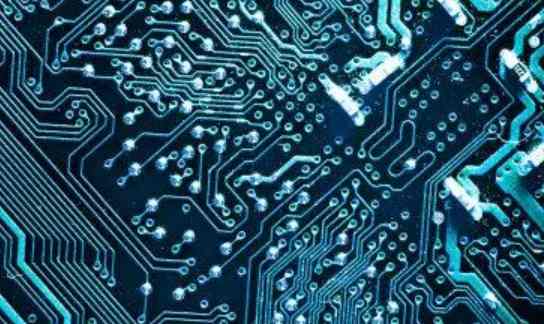
1. Compared with the circuit material without microsphere packing, the RO4730G3 circuit material with hollow microsphere packing may form metallized pores on the surface of rough pore wall.
RO4730G3 circuit boards and their microsphere fillers were extensively evaluated to fully understand their characteristics under different operating conditions before evaluating the effect of metallized pores and their pore wall surfaces on the performance of high frequency circuits. These tests include 10-layer accelerated heat shock (HATS)/metallized through hole (PTH) reliability, double-sided PTH reliability, double-sided PTH-Pth conducting anode wire (CAF) resistance, plane-to-plane CAF resistance, MOT and surface-to-surface mount (SMT), insulation resistance, Metallized pore quality and a series of material testing research. All tests showed that the material and its microsphere fillers passed these tests without problems under industry-standard test conditions.
In fact, in a number of studies and tests on this circuit board material and its microsphere filler, we used two materials with different characteristics of metallized pore wall to study the effects of changes in surface roughness of metallized pore wall on RF properties. The research and test are based on a specially designed microstrip transmission line circuit. There are microstrip line circuits in the top layer and the bottom layer respectively, and the medium in the middle is the dielectric material. The connection between the top layer and the bottom layer of microstrip lines is realized through the metallization hole. These tests are designed to provide very meaningful data reference for 5G applications, so the test circuits have good RF performance in the range of 100 MHz to 40 GHz.
The dielectric constants (Dk, or εr) of the two materials used in this study are very close, with values around 3. Materials of the same thickness were also selected for both materials, both of which were 20mil. The main difference between the two is that one can produce a metallized perforated hole with a smooth surface, while the other produces a metallized perforated hole with a rough surface. Rogers' RO3003G2™ circuit board material is used to create a smooth metallized perforated wall surface, while RO4730G3™ circuit boards with glass reinforcement and hollow microsphere fillers produce a rougher metallized perforated wall surface.
The texture difference of circuit metallized perforated wall surface is generally considered to be a circuit manufacturing problem rather than a material problem. However, a number of material characteristics can be optimized for metallizing through the pore wall surface, including circuit material filler type, filler size, glass reinforcement, and resin type. As a RO4730G3™ PCB and its hollow microsphere filler (rough metallized through pore wall surface), the RO3003G2™ PCB material in comparison has no glass reinforcement and has very small filler particles. Assuming the best PCB process is used for both, the latter will have a very smooth metallized through-hole wall surface. RO3003G2™ circuit boards can form a very smooth metallized through hole wall.
2. Microscopic images show the formation of smooth-faced metallized perforated pore walls in a 20mil thick RO3003G2 circuit material.
For the two circuit materials of the same thickness, the difference in surface roughness of the metallized holes of the two materials is very obvious. The observation of both diagrams may raise the question of whether the higher surface roughness of the metallized hole implies any problem in terms of RF performance. For test circuits, microstrip transmission line circuits are an effective way to compare the effects of smooth and rough metallized through hole wall surfaces on RF performance, because some changes in the fabrication of microstrip lines have less effect on RF performance than other high-frequency transmission line structures.
A great deal of effort has been put into optimizing these microstrip circuits in order to provide meaningful results from metallization through holes in different circuit materials at 40GHz. One of the big design challenges is the transition from RF test connectors to PCB microstrip lines. In general, it is difficult to get better echo characteristics on the signal transition of microstrip transmission lines on 20mil thick circuit boards, especially the transmission lines with frequencies above 25GHz. For wideband microstrip circuits, return losses of less than 15dB or better are generally considered acceptable.
The through-hole transition is another important factor to be considered, especially the low loss transition from one layer to another line layer is difficult to achieve at the millimeter-wave frequency. Generally speaking, it is difficult to achieve good performance of microstrip line through hole transition higher than 20GHz on 20mil thick circuit materials. However, considering the above difficulties, the microstrip test circuit in this study is designed to achieve good results even when the frequency reaches 40GHz.