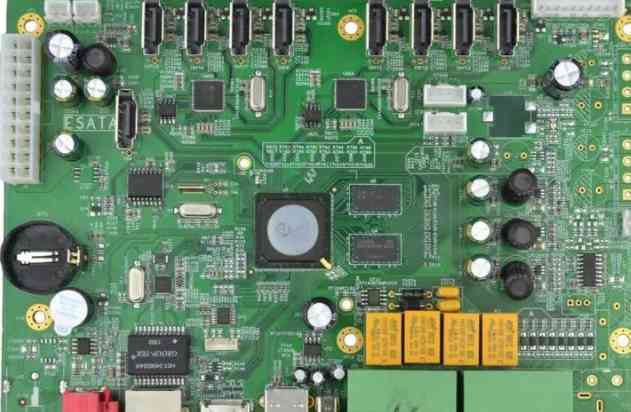
Friends from all industries, good afternoon! I am a small editor of OEM OEM processing plant. SMT quality management technology is a systematic and complex project, and problems in any link will increase the welding defect rate. Relevant statistics show that the proportion of SMT patch machining welding defects caused by original components is 20%-25%, welding paste is 20%-25%, PCB is 10%-15% and reflow is 35%-40%. It can be seen that the proportion of welding quality problems caused by electronic components is relatively high, so the SMT material management technology deserves attention. Next, we will introduce the packaging, transportation and storage requirements of electronic components in SMT patch processing by the OEM OEM enterprises in detail.
The high temperature of lead-free welding has strict requirements on the humidity sensitivity level of materials. Post-welding delamination and burst caused by moisture will seriously affect the reliability of electronic products. OEM suppliers must strictly control the transportation, packaging, storage, use and management requirements of moisture sensitive materials.
SMT assembly
Humidity sensitive materials mainly include PWB, FPC, LED, transistor (diode, transistor, field effect tube), IC, infrared tube, buzzer, power amplifier, crystal oscillator, FLASH, oscillator and fuse, etc. Components are the most sensitive, and the relevant reference standards are more detailed. For example, JEP113 is the symbol and identification of moisture sensitive components. J-STD-033B is for the classification and disposal of moisture sensitive integrated circuit components, and JEDECA113 is for the pretreatment of plastic sealing components before reliability tests. Class MSL-1 usually means that the component can be kept on the shelf for a long time without worrying about production issues; Components of the MSL-2 or higher grade are packed in a vacuum package in a moisture-proof and electrostatic proof bag. Desiccant must be added to the package. Note on the bag that the component is a damp sensitive device and its humidity sensitive grade, warning label, and sealing date label.
The moisture-proof performance requirements of the packaging of materials with different humidity sensitive grades are also different. The desiccant can absorb 2.85g water vapor at 20%RH/25℃ and dry the moisture in the bag. The humidity indicator card can roughly indicate whether the components are damp. Humidity card can be reused, generally a single point, three points, four points and six points, three points and six points are more common, can easily detect the relative humidity in the sealed packaging, when the indicating point becomes purple (between blue and pink), the value of the indicating point is the current environmental humidity.
To sum up, MSL-1 is a non-moisture sensitive material, which can be packed in vacuum or not, but must be sealed. Moisture-sensitive materials must be packed in moisture-proof bags (MBB) or in cartons if the above requirements are not met. All materials are not allowed to be stored in the following environment: direct sunlight or through Windows; Close to cold and wet objects, heat sources or light sources; Proximity to outdoor environments often results in excessive temperature and humidity.
Material inventory life, excluding the time consumed in manufacturing and receiving, refers to the time from receipt to storage plus the maximum inventory time. Unless otherwise specified on the packaging, all materials should be placed on open shelves and packaged in internal packaging. Generally, the maximum term is 12 months. Semiconductor material packaging materials shall meet MES00025, EAI-583, JESD625 and first-in-first-out (FIFO) principle.
2. Preparation for PCBA patch production
Friends from all industries, good afternoon! Last time, kingford shared the relevant knowledge of SMT automatic soldering. Today, Xiaobian would like to share with friends in the industry the relevant preparatory work before the official production of SMT patches.
The electronic components in SMT patch processing have changed from the original improvement only to adapt to the miniaturization of the whole machine and its new process requirements to meet the characteristics of the development of digital technology and microelectronics technology, and it is a complete set of meet the industrialization development stage.
SMT patch equipment is the core mounting equipment in SMT patch processing and production. It is necessary to know its preparation before mounting during operation. The first is to prepare the relevant product process documents; Collect materials (PCB, components) according to the mounting list of product process document, and check; For PCBS that have been opened, clean and bake them according to the length of time they have been opened and whether they are damp or polluted. Check the components after opening, and deal with damp components according to SMT process components management requirements; Select the integrated feeder according to the specification and type of the component, and install the component braid feeder correctly. When loading, the center of the component shall be aligned with the picking center of the feeder; Check the air compressor pressure should meet the requirements of the equipment, generally 6kgjf/cm2 ~ 7kgf/cm2; Check and make sure that there are no obstacles in the movement range of guide rail, mounting head, around the automatic replacement nozzle library and tray rack.
Many SMT processing plants will do a good job of the maintenance of the SMT placing machine after using it, so we need to do regular inspection. It is recommended to apply a thin layer of lubricant if the buffer action is not smooth. If the fixture is loose, tighten the moving lens to clean the dust and residue on the lens. It is also necessary to check the lead screw in X(w) axis for debris or residue. If there is, it is also necessary to clean them. There is attention to check the X (Y) axis guide rail to check whether the grease hardening and residue adhesion. Finally, look at the Y-axis lead screw to check whether the lead screw debris or residue.