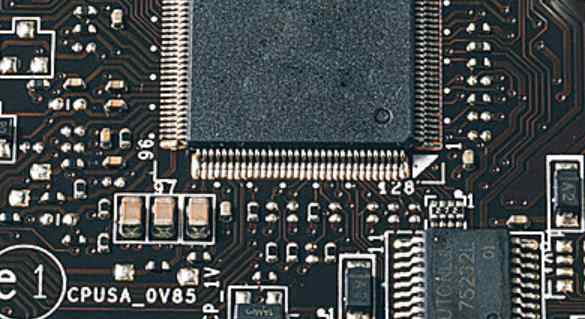
Definition of PCB high frequency board
High frequency board refers to special circuit board with high electromagnetic frequency, which is used for PCB in the field of high frequency (frequency greater than 300MHZ or wavelength less than 1 m) and microwave (frequency greater than 3GHZ or wavelength less than 0.1 m). It is a circuit board which is produced by using part of the manufacturing process of the common rigid circuit board or by using a special processing method on the microwave-based copper clad board. Generally speaking, high-frequency boards can be defined as circuit boards with frequencies above 1GHz.
With the rapid development of science and technology, more and more equipment is designed in the microwave frequency band (> 1GHZ) or even the field of millimeter wave (30GHZ) above the application, which also means that the frequency is higher and higher, the requirements of the circuit board substrate is also higher and higher. For example, the substrate material needs to have excellent electrical properties, good chemical stability, with the increase of power signal frequency on the substrate loss requirements are very small, so the importance of high frequency plate is highlighted.
Two.PCB high frequency board application field
2.1 Mobile communication products
2.2 Power amplifier, low noise amplifier, etc
2.3 Power divider, coupler, diplexer, filter and other passive devices
2.4 Automotive anti-collision system, satellite system, radio system, etc. The high frequency of electronic equipment is the development trend.
Three. High-frequency plate classification
3.1 Thermosetting materials filled with powder ceramics
A. Manufacturer:
Rogers 4350B/4003C
Arlon's 25N/25FR
TLG line from Taconic
B. Processing method:
And epoxy resin/glass braid (FR4) similar processing process, only the plate is brittle, easy to break plate, drilling and gong plate drilling nozzle and gong knife life to reduce 20%.
3.2 PTFE material
A: The manufacturer
1Rogers RO3000 series, RT series, TMM series
2Arlon AD/AR series, IsoClad series, CuClad series
3Taconic's RF series, TLX series and TLY series
4 F4B, F4BM, F4BK, TP-2 of Taixing Microwave
B: Processing method
1. Opening: must retain the protective film opening, to prevent scratches, indentation
2. Drilling:
2.1 New drill nozzle (standard 130), one piece in stack is the best, press pin pressure is 40psi
2.2 The aluminum sheet is the cover plate, and then the PTFE plate is tightened with 1mm dense amine plate
2.3 After drilling, blow the dust out of the hole with the air gun
2.4 Using the most stable drill, drilling parameters (basically, the smaller the hole, the faster the drilling rate, the smaller the Chip load, the smaller the return rate)
3. Hole treatment
Plasma treatment or sodium naphthalene activation treatment is beneficial to pore metallization
4.PTH copper sinking
4.1 After microetching (controlled with microetching rate of 20 microinches), pull into the plate from the deoil cylinder at PTH
4.2 If necessary, the second PTH can be performed from the expected? The cylinder began to feed into the plate
5. Welding resistance
5.1 Pretreatment: acid washing shall be adopted, and mechanical grinding shall not be used
5.2 After pretreatment, bake the plate (90℃, 30min) and brush with green oil for curing
5.3 Three sections of baking plate: one section at 80℃, 100℃ and 150℃ for 30 minutes each (If oil is found on the substrate surface, rework: wash off the green oil and reactivate it)
6. Gong boards
The white paper is laid on the PTFE board line surface, and the upper and lower FR-4 substrate board or phenolic substrate board with a thickness of 1.0MM etched to remove copper is clamped: as shown in the figure:
High frequency plate and gong plate laminated method
The raw edge of the gong plate after the plate needs to be scraped carefully by hand, to prevent damage to the substrate and copper surface, and then separated by a considerable size of sulfur-free paper, and visual detection, to reduce burr, the focus is on the gong plate process to shaw effect should be good.
Four: technological process
1.NPTH PTFE plate processing process
Opening - Drilling - Dry film - Inspection - Etching - Corrosion inspection - Solder resistance - Character - Tin-spray - Molding - Test - Final Inspection - Packaging - Shipping
2.PTH PTFE plate processing process
Opening - drilling - hole treatment (plasma treatment or sodium naphthalene activation treatment)- Copper plating - electroplating - dry film - Inspection - Electroplating - Etching - Corrosion inspection - solder resistance - character - tin spray - Molding - Test - Final inspection - Packaging - Shipping
Five: Summary: high frequency plate processing difficulties
1. Copper sinking: the hole wall is not easy to copper
2. Control of line notch and sandhole of graph turning, etching and line width
3. Green oil process: control of adhesion and foaming of green oil
4. Strict control of board scratches in each process, etc
North American PCBS returned to growth strongly in 2019, with the book-to-shipment ratio rising to 1.06 in February
IPC -- International Association of Electronic Industry Connections ® recently released the "2019 February PCB industry Survey Statistical Report in North America". The report showed strong growth in both sales and orders in February, with the book-to-shipment ratio rising to 1.06; As a result of revisions to industry submissions, January's operating results were much more positive than originally reported.
PCB shipments in North America increased 13.9% in February 2019 compared to the same period last year, compared to 15.5% growth in January. Year-to-date sales growth is up 14.7 percent. Shipments fell 5.2 percent in February from the previous month.
PCB orders rose 10.7% in February from a year earlier, after falling 1.7% in January. Year-to-date order growth is up 4.4%; Orders rose 8.8% in February compared with the previous month.
Ms Sharon Starr, Director of market Research at IPC, said: "The revised operating figures for January are better than the results published in the original report. After slowing in late 2018, growth returned strongly in 2019. The order-to-shipment ratio rose to 1.06 in February from a revised 1.02 in January, indicating a positive outlook for sales in the coming months."