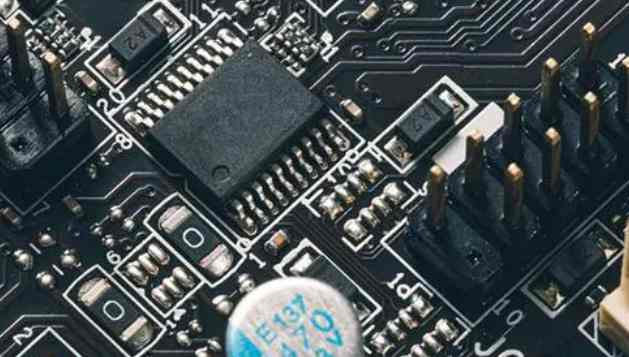
Some netizens asked "SMT process, the circuit board after Reflow is prone to bending and warking, serious cases will even cause component welding, monument, how to overcome it?"
To be honest, the reasons for the formation of each plate bending and warping may not be quite the same, but it should be attributed to the stress exerted on the board is too large to bear the stress of the board material, when the stress under the board is not uniform or the ability of each place on the board to resist the stress is not uniform, there will be the result of bending and warping.
Where does the stress on the board come from? In fact, the biggest source of stress in Reflow process is "temperature", which not only makes the circuit board soft, but also distorts the circuit board. This, coupled with the material properties of "thermal expansion and cold contraction", is the main cause of the bending and warping of the board.
So why do some boards bend and warp differently?
1. The copper surface area on the circuit board is uneven, which will worsen the bending and warping of the board.
Generally, a large area of copper foil will be designed on the circuit board for grounding, and sometimes Vcc layer will also be designed with a large area of copper foil. When these large areas of copper foil are not evenly distributed on the same circuit board, it will cause the problem of uneven heat absorption and heat dissipation speed. Of course, the circuit board will also expand and shrink. If the expansion and contraction cannot be done at the same time, it will cause deformation under different stresses. At this time, if the temperature of the board has reached the upper limit of Tg value, the board will begin to soften, resulting in permanent deformation.
2. Connecting points (vias) between the layers on the board limit board growth and shrinkage
Most of today's circuit boards are multilayer boards, and there will be a connection point (via) to the same as the rivets between the layers, and the connecting point is divided into through holes, blind holes and buried holes, where the connecting point will limit the effect of the board, but also indirectly cause the bending and bending of the board.
3. The weight of the circuit board itself will cause the board to sag
General back welding furnace will use the chain to drive the circuit board forward in the back welding furnace, that is, to both sides of the board when the fulcrum to prop up the whole board, if the board above the excess parts, or the size of the board is too large, it will be due to its own kind of amount and show the middle depression phenomenon, resulting in bending.
4. The depth of V-Cut and the connection strip will affect the deformation of the plate
Basically, V-Cut is the culprit of damaging the structure of the board, because V-Cut is in the original a large sheet of the board to cut out V-shaped grooves, so the V-Cut place is prone to deformation.
How can we prevent the bending and warping of the plate after the back welding furnace?
1. Reduce the influence of temperature on the stress of the plate
Since "temperature" is the main source of plate stress, so as long as reducing the temperature of the backwelding furnace or slow down the heating and cooling speed of the plate in the backwelding furnace, the bending and warping of the plate can be greatly reduced. But there may be other side effects, such as a short circuit in the solder.
2. High Tg plate is used
Tg is the glass conversion temperature, that is, the temperature at which the material changes from glass state to rubber state. The lower the Tg value is, the faster the board will become soft after entering the backwelding furnace, and the longer it will take to become soft rubber state, the more serious the deformation of the board will be. The plate with higher Tg can increase its ability to withstand stress and deformation, but the price of the material is relatively high.
3. Increase the thickness of the circuit board
Many electronic products in order to achieve the purpose of thinner, the thickness of the board has been left 1.0mm, 0.8mm, and even 0.6mm thickness, such a thickness to keep the board in the welding furnace without deformation, really a bit of force, it is suggested that if there is no light and thin requirements, the board can use the best thickness of 1.6mm, Can greatly reduce the risk of bending and deformation of the plate.
4. Reduce the size of the circuit board and reduce the number of boards
Since most backwelding furnaces use chains to drive the circuit board forward, the larger the size of the circuit board will sag and deform in the backwelding furnace because of its own weight, so try to put the long side of the circuit board as the board side on the chain of the backwelding furnace, you can reduce the weight of the circuit board caused by the sag deformation, reduce the number of plates is also based on this reason, That is to say, when the furnace, as far as possible to use the narrow side of the vertical direction of the furnace, can achieve the lowest depression deformation.