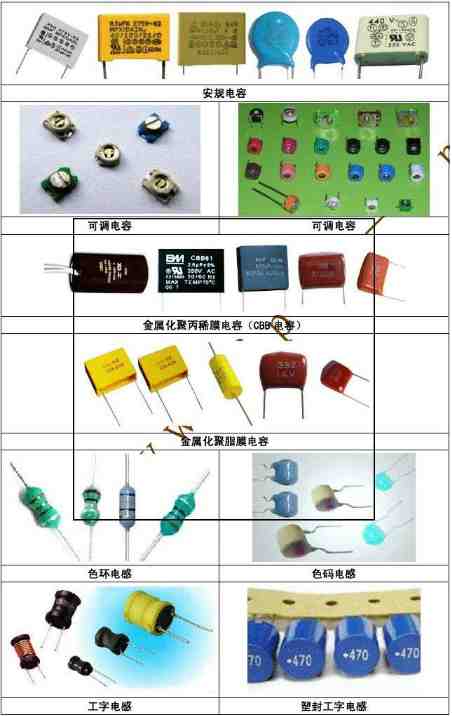
PCB process: Details of the latest circuit board via hole process
PCB through hole (via) process is the core of quality control, but also accounts for about 30 to 40 percent of the entire PCB manufacturing cost, because it has a pivotal position. Using scientific and standard via process flow and drilling equipment, and equipped with professional inspection procedures is the basis to ensure the quality of PCB circuit board via hole.
1. Basic concepts of via through holes
via through hole is a circular aperture through the circuit board, according to its role can be divided into signal through hole, power/ground through hole, heat dissipation hole, among which the signal through hole is the most common. Signal through hole (via) is mainly used for electrical connection between PCB layers and positioning of components. In terms of process classification, signal through holes (via) are further divided into blind via, buried via and through via.
2. via perforation process
PCB via holes must be completed with the help of professional drilling RIGS, such as Hitachi, Schmoll, Timax and other brands. The PCB substrate is fixed on the drilling machine, and the drill bit meeting the aperture requirements is assembled. The drilling process can be completed by inputting the drilling coordinate program in the PCB file on the drilling machine and adjusting the corresponding drilling speed. In the via process, drilling accuracy, position deviation and bit fracture must be monitored in real time, and problems can be solved in time.
3. pcb drilling machine via drilling equipment
Drilling machine is the most important equipment for via perforation. There are many styles and functions in the market. PCB factory selection can be evaluated based on the following factors:
A. Number of shafts: directly related to output
B. Effective drill plate size
C. Drilling machine surface: select the material with small vibration and good strength.
D. Spindle
E. Drilling disc: automatic change of bit and bit number
F. Pressure foot
G. X, Y and Z axis drive and size: accuracy, X and Y move independently
H. Dust collection system: equipped with pressure foot, good chip removal, and cooling bit function
I. Ability to Step Drill
J. Broken needle detection
K. RUN OUT
4. Process notes for via through holes
In through hole via process, the following faults often occur, and operators and technicians need to have rich problem identification and solution capabilities.
A. Broken cobalt nozzle
B. Hole damage
C. Hole offset and mismatch
D. Through hole size distortion
E. Leaking borehole
F. The Cape
G. The hole is not drilled through
H. Curly debris appears on the panel
I. The hole is blocked
pcb via
PCB hole via process is one of the most critical links in the whole process of PCB manufacturers, which determines PCB quality and electrical connection performance, and is also an important node for batch scrapping or rework. Therefore, every PCB factory will establish a strong and perfect mechanism from the process documents, personnel control, inspection procedures and other aspects, in order to ensure the good operation of batch PCB production.
7. The board surface oxidizes in the production process; If the oxidation of the copper plate occurs in the air, it may not only cause no copper in the hole, the surface of the board is rough, but also may cause the surface of the board to bubble; Copper plate in acid storage time is too long, the surface will also occur oxidation, and this oxide film is difficult to remove; Therefore, in the process of production, the copper plate should be thickened in time, and should not be stored for too long. Generally, the thickened copper plating should be completed within 12 hours at the latest;
8. Bad copper rework; Some of the copper or graphics after the rework board in the rework process because of poor fading plating, rework method is not correct or rework in the process of micro erosion time control or other reasons will cause foaming; If the copper plate rework on the line is found to be bad, it can be washed directly from the line after oil removal after pickling without corrosion directly rework; It is best not to re-remove oil, micro corrosion; For the plate that has been electrically thickened, the plating should be removed by micro-etching groove and pay attention to time control. One or two plates can be used to roughly measure the plating time to ensure the plating effect; After the plating is finished, apply a set of soft grinding brushes to brush lightly and then sink copper according to the normal production process, but the corrosion time should be halved or adjusted as necessary; High frequency plate
9. In the process of graphic transfer, insufficient washing after development, too long placement time after development or too much dust in the workshop will cause poor cleanliness of the board, and the fiber treatment effect is slightly poor, which may cause potential quality problems;
11. There is organic pollution in the plating tank, especially oil pollution, which is more likely to occur in the automatic line.