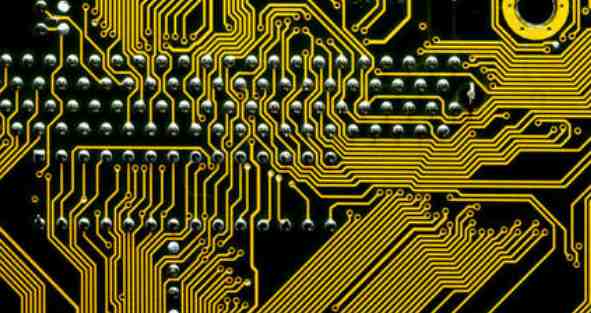
Inspection is a product-centered activity, while monitoring is a process-centered activity. Both are needed for a quality program, but the long-term goal should be less product inspection and more process monitoring. Product inspection is passive (defects have already occurred), while process monitoring is proactive (defects can be prevented) - obviously, prevention is much more valuable than reacting passively to defects that already exist.
Checks will always remind you if there are too many variables in your assembly process (SMT process). Even after your manufacturing process has achieved consistent zero defect production, some form of inspection or monitoring is necessary to ensure the desired level of quality. Surface mount assembly is a series of very complex events with a large number of individual actions. The trick is to create a strategy that balances inspections and monitering without having to do 100 percent of the inspections. This article discusses inspection methods, techniques, and manual inspection tools, as well as reviewing automated inspection tools and using inspection results (number and type of defects) to improve process and product quality.
Inspection is actually a screening process, as it attempts to find unacceptable products to fix. The fact is clear that extensive inspection does not necessarily improve or guarantee the quality of products. Deming's third of 14 points says, "Don't expect mass inspections." Demin emphasizes that a strong process should focus on establishing stable, repeatable, and statistically monitored process goals, rather than on mass inspections. Inspection is a subjective activity, and even with a fair degree of training, it is a difficult task. In many cases, you can call a team of inspectors to evaluate a weld and get several different opinions.
Operator fatigue is the reason why a 100% inspection usually fails to find every manufacturing defect, plus, it is a costly, value-adding operation. It rarely achieves the desired goals of higher product quality and customer satisfaction.
A few years ago, we started using the term "process monitoring" instead of inspectors because we wanted to change the mindset of the production site from reactive to proactive prevention. An inspector usually sits at the end of the assembly line and checks the product. In an ideal world, process monitoring activities are a balance between product inspection and process monitoring - for example, verifying that correct process parameters are being used, measuring machine performance, and establishing and analyzing control charts. Process monitoring assumes a leading role in these activities; They help machine operators with these tasks. Training is a key element. Process monitors and machine operators must understand process standards (e.g., IPC-A-610), process monitoring concepts, and related tools (e.g., control charts, Pareto charts, etc.). Process monitors also improve product quality and process monitoring. As a key member of the manufacturing team, the monitor encourages a defect prevention approach rather than a search and repair approach.
Overinspection is also a common problem. In many cases, overinspection is simply the result of a misplaced understanding of the IPC-A-610 process standard. For example, for insert mounted components, many inspectors also want both sides of the plate perfectly welded round feet, with the through-hole fully filled. However, this is not required by IPC-A-610. The quality of the inspection fluctuates with the intensity and concentration of the inspector. For example, fear (management pressure) may increase the concentration level of the production site, and quality may improve over time. However, if mass inspection is the main inspection method, defective products may still be produced and may leave the factory.
Another term we should avoid is touch-up. In this industry, many employees consider repair welding to be a normal and acceptable part of the assembly process. This is unfortunate, as rework and repair of any kind should be considered undesirable. Rework is often seen as undesirable, but it is necessary to instill information throughout the manufacturing organization. It is important to establish a manufacturing environment where defects and rework are seen as avoidable and least desirable.