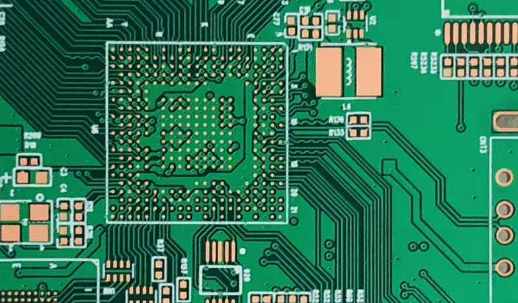
As cameras based on a 360-degree panoramic system are increasingly an optional feature of cars, the technology will do as much as it can for self-parking vehicles that solve the hassle of finding a spot or plugging in.
The system uses the rear view camera of the 360-degree panoramic system to prevent collisions during reversing. "Fisheye cameras with 360-degree panoramic systems are ideal for autonomous parking because they are able to 'see' the full picture around the car," he said. "For example, their wide aperture angles even allow viewing of parking Spaces with corners. In addition, the camera can detect the white parking space boundary line, which is not possible with traditional ultrasonic sensors."
The 360-degree panoramic system has the potential to expand
The driver can change the recommended parking position by moving the outline of the car in any direction on the touch screen. This option allows the driver to respond to specific situations that are difficult to interpret even with high-performance object-recognition systems (such as delivery vehicles parked in front or behind the vehicle and requiring more maneuvering space than a car).
In the future, autonomous parking based on 360-degree cameras will also allow drivers to park from outside the vehicle, or remotely initiate parking operations. "In Remote Parking, the driver uses a touch screen to select the parking space and activate Remote mode, then leaves the car and uses the smartphone app to initiate and observe the automatic parking operation."
As the system is further refined, the current progress will evolve into a scalable, mass-production-capable system that can provide one or more ancillary functions to the overall on-board network. These features, based on a 360-degree panoramic system, will include intersection assist and reverse assist with automatic braking.
Analysis of factors affecting SMT installation rate and common failures of SMT machine
SMT equipment is mainly considered in the selection of SMT installation precision and installation speed, in the actual use process, in order to effectively improve product quality, reduce production cost, improve production efficiency, how to improve and maintain SMT equipment installation rate is placed in front of the users of the primary topic.
The so-called mount rate refers to the ratio between the actual mount number of the device and the number of absorption within a certain period of time, namely: mount rate = ×100% of the number of absorption, in which the total number of discarded pieces refers to the number of absorption errors, identification errors, number of vertical pieces, number of lost, and identification errors are divided into two types: component size error and poor optical recognition of the device. SMT machine no matter small machine, medium machine, large machine, no matter medium speed machine, high speed machine, they are mainly composed of device storage device, XY workbench, mounting head and control system. The mounting head is the core and key parts of the mounting machine. The mounting head is generally divided into a fixed head and a rotating head. The fixed head is generally multi-head arranged, with as few as 2 and as many as 8, which can be taken simultaneously or separately.
A. Device suction nozzle suction height switch
B, θI rotation (±90 ')
C. Optical recognition of devices
D, device attitude detection θ2 rotation (±90 ')
E. Switch the mounting device/nozzle height
F, θ3 rotation (±180 '-θ) suction nozzle origin detection of defective products excluded
G. Nozzle conversion
H. The number of the nozzle is detected according to the fitting machine
In the whole process of mounting, purely from the perspective of equipment, the main factor affecting the rate of mounting equipment is the position of taking parts. According to the production information statistics of the equipment, the influence accounts for more than 80% of the whole influencing factors when the height of the suction nozzle and the relative position of the suction nozzle center and the feeder are set correctly. The reasons are: on the one hand is the feeder on the device storage device, on the other hand is the suction nozzle, about 60% of the film of the feeder, about 40% is caused by the pollution of the suction nozzle.
Feeder impact Feeder impact master focuses on feeding anomalies.
The driving modes of the feeder include motor drive, mechanical drive and cylinder drive, etc. Here, the mechanical drive is taken as an example to illustrate the influence of the feeder on the mounting rate:
1. The mechanical driving part is driven by the CAM spindle to drive the feeding mechanism, and the striking arm of the feeder is quickly found. The ratchet connected with it drives the component braid forward a distance through the connecting rod, and drives the plastic coil to remove the plastic cap from the braid, and the suction nozzle drops to complete the taking action. But because the feeding mechanism visits the feeder at high speed, after a long time of use, the pawl of the feeder is seriously worn, resulting in that the pawl cannot drive the plastic strip of the coil plate to peel off normally, so that the suction nozzle can not complete the fetching work. Therefore, the feeder should be carefully checked before the installation of braid, the pawl wheel has been worn out of the feeder should be repaired immediately, can not be repaired should be replaced in time.
2, the deformation of the feeder structural parts due to long-term use or improper operation of the operator, the pressure belt cover plate, thimble, spring and other motion mechanism deformation, corrosion, etc., which leads to the device bias, vertical or suction device, so it should be checked regularly, found problems in time to deal with, so as not to cause a lot of waste of devices, At the same time, the installation of the co-feeder should be correctly and firmly installed on the platform of the feeding department, especially the equipment without the height detection of the feeder, otherwise it may cause damage to the feeder or equipment.
3, the poor lubrication of the feeder is generally maintenance and maintenance of the feeder, which is easy to be ignored, but regular cleaning, cleaning, refueling lubrication is an essential work.