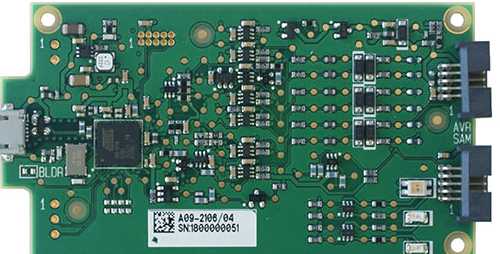
Where can SMT manual patch processing be done
Why do SMT manual SMT processing?
During the b of circuit board, some components such as switches, buttons and connectors cannot be installed by automatic SMT machine, so engineers need to manually patch and then reflow weld.
SMT manual patch processing process
1. Clean and secure the PCB
When the PCB board is processed by patch, the PCB should be checked briefly first to ensure that its surface is clean and whether there are impurities. If the PCB is found to be stuck with oily fingerprints or oxides, clean non-woven fabric should be used to clean, so that it does not affect the subsequent soldering work on the tin. When SMT manual placement is carried out, if equipment conditions permit, the PCB board can be fixed with a welding platform and other tools for welding. However, the general welding work can be fixed directly by hand, but it should be noted that fingers should not directly contact the welding pad on PCB.https://www.kingfordpcb.com/yuan.php
2. Secure the required components
Fixing the required patch element is the most important step in SMT manual patch. According to the different pin number of patch components, fixing methods can be roughly divided into two categories, that is, single pin fixing and multi-pin fixing. The patch elements with less than five pins are generally fixed with one pin, and those with more pins are usually fixed with multiple pins.
3. Weld the pins
With the element roughly in place, the remaining pins can be welded. For relatively few pin components, you can choose a single hand solder, the other hand soldering iron, in turn to spot welding. If the pins are multi-cut and densely distributed, you can use the method of drag welding, but be careful to ensure that all pins are well connected to the pad and cannot be welded.
4. Clean the solder
If too much solder is accidentally melted in the previous step, it is easy to short-circuit the PCB. In order to deal with the excess solder, you can use a tin absorbing tape to remove the excess solder.
5. Clean the welding points
After soldering and cleaning the solder, the patch element is basically welded. However, rosin and tin absorbing tape used in the welding process will leave some rosin residues around the component pins. These residues will not have a great impact on the normal use of PCB, but may bring inconvenience to inspection and maintenance, and it is not beautiful enough. Generally, professional cleaning water can be used to clean the board. If no alcohol is used instead, it can also be used. Cleaning tools can be wiped SMT machines with cotton swabs or non-woven cloth held with tweezers. After cleaning the circuit board, SMT manual patch is completed.
1. Strength guarantee
▪SMT workshop: We have imported SMT machines and several sets of optical inspection equipment, with a daily output of 4 million. Each process is equipped with QC personnel, who can keep an eye on product quality.
▪DIP production line: We have two wave-soldering machines, among which there are more than 10 old employees who have worked for more than three years. The skilled workers can weld all kinds of plug-in materials.
2. Quality assurance, cost-effective
▪ High-end equipment can stick precision shaped parts, BGA, QFN, 0201 materials. Can also template patch, loose material hand.
▪ Sample and size batch can be produced, proofing from 800 yuan, batch 0.008 yuan/point, no start-up fee.
3. Rich experience in SMT and welding of electronic products, stable delivery
▪ Accumulated SMT SMT processing services for thousands of electronic enterprises, involving many kinds of automotive equipment and industrial control motherboard. The products are often exported to Europe and the United States, and the quality can be affirmed by new and old customers.
▪ On time delivery, normal 3-5 days after complete materials, small batch can also be expedited on the same day shipment.
4. Strong maintenance ability and perfect after-sales service
▪ Experienced maintenance engineers can repair all kinds of patch welding caused by bad products, to ensure the connection rate of each piece of circuit board.
▪ 24-hour customer service staff at any time response, the fastest speed to solve your order problems.