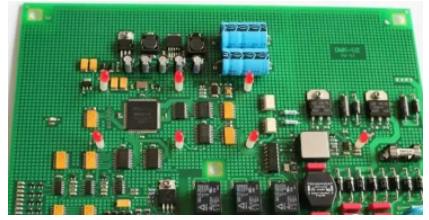
The first piece detects operation on the SMT patch
The first piece detection is an essential mechanism in the production and processing process of PCBA contracted work and materials. In the production process of PCBA, the first piece detection can help people find wrong parts in advance, prevent technological omisses, and effectively improve the quality of processing.
1, manual or use automatic loading machine to send PCB to the conveyor belt, the equipment automatically complete a series of procedures such as spraying flux, wave soldering, cooling and so on.
2. Catch PCB at the wave soldering outlet.
3, according to the industry standard "Welding Spot Quality Assessment" SJ/T10666-1995 or IPC-A-610E for the first part of the welding quality inspection, according to the first part of the welding results to adjust the welding parameters, until the quality standards can be mass production.
We have repeatedly mentioned the PCBA first part testing, which plays a non-negligible role, why the need for the first part testing after wave soldering?
The PCBA process mainly includes solder paste printing, SMT patch, reflow welding, DIP plug-in, wave soldering and electronic product testing and assembly. If there is no fault in the process, the circuit board can be assembled by wave soldering. If a product that has passed the process is directly produced without inspection, it needs to be repaired in case of poor quality. Therefore, in most cases, PCBA processing plants must carry out the first inspection after wave soldering, and confirm with the customer after passing the inspection, and then carry out mass production.
Silk screen printing. It is to prepare for the welding of components. It is to leak the patch or solder paste onto the pad. The equipment used is screen printing machine, which is at the very front of smt production line.
2, dispensing. This step is very important. Use a glue dispenser to drop the glue onto a fixed position of thehttps://www.kingfordpcb.com/yuan.php?time=1685377305 The purpose is to fix the component to the board.
3. Mount. The assembly components are correctly installed on the fixed position of pcb by using the SMT machine.
4. Cure. A curing furnace is used to melt the patch so that the component is firmly bonded to the plate.
5. Reflow welding. The reflow furnace is used to melt the solder paste, mainly for bonding and firmness.
6. Wash. Use a cleaning machine to remove the welding residue on the pcb board, including the flux, which has no fixed location, can be online or not online.
SMT patch processing needs to go through the above procedures, in addition to detection and repair, which need to be completed with corresponding tools.