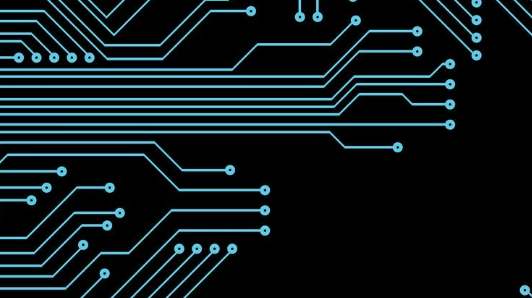
Electronic communication technology from wired to wireless, from low frequency, low speed to high frequency, high speed. Now mobile phone performance has entered 4G and will move towards 5G, which means faster transmission speed and larger transmission capacity. With the advent of the global cloud computing era, the data flow has multiplied and the high frequency and high speed of communication equipment is an inevitable trend. PCB for high frequency, high speed transmission needs, in addition to circuit design to reduce signal interference and loss, maintain signal integrity, and PCB manufacturing to maintain in line with the design requirements, it is important to have a high performance substrate.
Design engineers to solve PCB increase speed and signal integrity, mainly for electrical loss properties. Dielectric constant (Dk) and dielectric loss (Df) are key factors in substrate selection. When Dk is below 4 and Df0.010, it is a medium Dk/Df class laminate. When Dk is below 3.7 and Df0.005, it is a low Dk/Df class laminate.
At present, the high frequency circuit board substrate is mainly fluorine resin, polyphenyl ether (PPO or PPE) resin and modified epoxy resin these three categories of materials. Fluorinated dielectric substrates, such as polytetrafluoroethylene (PTFE), have the lowest dielectric properties and are usually used above 5GHz. In addition, modified epoxy FR-4 or PPO substrates can be used for products between 1GHz and 10GHz. Among these three types of high-frequency substrate materials, the cost of epoxy resin is the cheapest, while fluorine resin is the most expensive; From the dielectric constant, dielectric loss, water absorption and frequency characteristics, fluorine resin is the best, epoxy resin is worse. When the product application frequency is higher than 10GHz, only fluorine resin printed board can be suitable. But the disadvantages of PTFE are poor rigidity and high coefficient of thermal expansion in addition to high cost.
For polytetrafluoroethylene (PTFE), in order to improve the performance with a large number of inorganic materials (such as silica SiO2) filled material or glass cloth for enhancement, to improve the rigidity of the substrate and reduce its thermal expansion. In addition, because of the molecular inertia of PTFE resin itself, it is not easy to combine with copper foil poor, so it is more necessary to combine with copper foil special surface treatment. Treatment methods on the surface of PTFE chemical etching or plasma etching, increase the surface roughness or add a layer of bonding film between copper foil and PTFE resin to improve the bonding force, but may have an impact on the performance of the medium, the whole fluorine system high frequency electric subgrade board still needs to be further developed.
A unique insulating resin is synthesized by modified epoxy resin or polyphenyl ether (PPE), metaphenic anhydride (TMA), diphenyl methane diisocyanate (MDI) and bismaleimide (BMI). FR-4 copper clad plate, which is similar to glass cloth, is widely selected at the present stage because of its excellent heat resistance, dielectric property and mechanical strength. compat also has the processability of conventional PCBS and will be more popular than PTFE substrates.
Dk6.6(1MHz) of E glass cloth and Dk3.6(1MHz) of epoxy resin make up Dk4.2~4.8 of FR-4. New NE glass cloth Dk4.4, constituting about Dk4.0 of FR-4. The new NE glass cloth is an effective way to reduce Dk. For example, the Megtron6 HF substrate introduced by Panasonic uses polyphenyl ether (PPO) as the main resin, Dk=3.4, Df=0.0015(1GHz). Japan Lee Chang Industry also uses polyphenyl ether as the main resin substrate, launched the CS-3376CN new substrate its Dk=3.1, similar to PTFE substrate. The new BT resin substrate of Mitsubishi Gas is nearly 60% lower than the dielectric properties of its original BT substrate by adjusting the ratio of BT to epoxy resin. Esora's Tachyon-100G substrate has PTFE-like electrical properties, and FR-4-like PCB processing conditions, Dk3.0 and Df0.002 at 40GHz, to deliver 100 gigabit Ethernet (100GbE) needs.
In addition to the above insulating material properties of resin and other special requirements for high frequency copper coated plate, the surface roughness (contour) of conductor copper is also an important factor affecting signal transmission loss, which is affected by the SkinEffect. The skin effect is the electromagnetic induction generated in the wire during the transmission of high-frequency signals. The inductance is larger at the center of the cross section of the wire, so that the current or signal tends to be concentrated on the surface of the wire. Conductor surface roughness affects the transmission signal loss, smooth surface loss is small.
At the same frequency, the greater the surface roughness of copper, the greater the signal loss, so we try to control the surface roughness of copper thickness in the actual production, the smaller the roughness without affecting the binding force, the better. Especially for signals in the range above 10GHz. The copper foil roughness at 10GHz should be less than 1μm, and the superplane copper foil (surface roughness 0.04μm) is better. Copper foil surface roughness also needs to be combined with appropriate oxidation treatment and bonding resin system. In the near future, there will be a nearly contourless resin coated copper foil, can be higher peel strength without affecting dielectric loss.