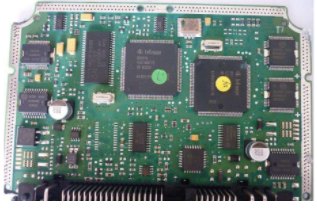
Precautions for SMT processing plant to start operation after the festival
Before starting up the SMT factory after the festival, it is necessary to confirm whether the temperature and humidity of the SMT workshop exceed the environmental requirements, whether the equipment is affected by moisture and whether there is dew. Do not rush to raise the temperature of the SMT workshop in a cold environment, as dew is likely to occur on the equipment. (Do not turn on the power at this time)
Select the dehumidification treatment time of the equipment according to the different degree of moisture exposure, (check whether the electrical part of industrial control is normal) open the front and rear case cover of the equipment (pay attention not to touch the wire inside the corner), and place the fan 0.5 meters in front of the case for blowing (purpose: to blow the moisture in the case with a blower note: Do not use hot air), choose 2-6 hours of blowing operation according to the degree of moisture, after the moisture removal operation, switch on the power, start the machine after the check, but do not return to the origin, about 30-60 minutes after starting the machine to warm up.
I. Printing Press
Notes for solder paste press
1. Remove the scraper to clean the residual solder paste; 2. Add special new lubricating oil after the lead rail is cleaned; 3. Use air gun to clean the dust of electrical equipment department; 4. Protect phase with anti-sitting cover; 5. Check whether the rail transport belt is replaced; Whether the cleaning mechanism device needs to be cleaned; 7. Whether the cylinder holding steel mesh mechanism is normal; 8. Check whether the gas circuit is normal; 9. Electrical industrial control is normal.
Two, patch machine
Points to note for the patch machine
1. First check whether the electrical part of industrial control is normal;https://www.kingfordpcb.com/yuan.php
2. Check whether there are any missing products in the SMT machine;
3. Whether the track belt is damaged and deformed;
4. After cleaning the dust of the lead screw, inject special new lubricating oil;
5. Whether the suction nozzle air path is normal;
6. Feeder guide chute clean and maintain;
7. Cleaning and electrostatic inspection and maintenance of automatic suction nozzle replacement device;
8. Cleaning and electrostatic inspection and maintenance of the throwing box;
9. General use machine backpack mechanism cleaning inspection and maintenance;
10. Feeder automatic refueling vehicle mechanism inspection and maintenance.
Three, reflow welding
Precautions for reflow welding
1. Annual maintenance of reflow welding machine.
2. Clean the residual components and rosin in the furnace; Transport chain after cleaning and maintenance of high temperature chain oil, mesh belt inspection and maintenance.
3. Clean the dust on the heating wire of the hot air motor with an air gun, and clean up the reflow welding electric box. It is mainly the dust inside the electric box.
4. Power off the UPS completely. Ensure that the UPS power supply is off.
5. Check whether the fan works properly.
6. Preheating zone, constant temperature zone, reflux zone, cooling zone four temperature zone system is normal.
7. Check and maintain the flux recovery system in the cooling area.
8. Check whether the waterway is normal.
9. Whether the furnace sealing strip device is normal.
10. Import and export cutting curtain inspection and maintenance.
11. Empty plate on the track to check whether the track deformation plate phenomenon.
Four, wave welding wave welding matters needing attention
1. Completely clean up the welding aid residue of the spraying device, empty the welding aid, add alcohol, and clean the welding aid pipe and nozzle with continuous spraying mode.
2. After cleaning, empty the alcohol to ensure the helpless flux and alcohol inflammable substance on the machine.
3. Use an air gun to clean the hot air motor, dust on the heating wire, and use the gun to clean the electric box, mainly the dust inside the electrical appliance. If necessary, add a drying agent to avoid moisture exposure to the electrical appliance.
4. Disconnect the power supply completely.
5. Whether the electrical part of industrial control is normal.
6. Track inspection and maintenance.
Five, AOI
Notes for AOI:
1, guide screw cleaning and maintenance add new butter.
2. Use air gun to remove dust from electrical appliances, and add desiccant into electric box.
3. Clean and protect with dust cover.
4. Check whether the light source mechanism is normal.
5. Check whether the motion shaft and motor of the equipment are normal.
Vi. Precautions for loading and unloading machine of peripheral equipment
1. Add butter to the lead rod column.
2, use the air gun to clean the dust of the electrical part, and add the desiccant in the electric box.
3. Remove the material frame from the bottom and clean up the sensor dust.
Points for attention at the docking station
1, drive shaft, belt pulley clean, oil.
2. Clean the inductor.
Strength guarantee
▪SMT workshop: We have importedSMT machines and several sets of optical inspection equipment, with a daily output of 4 million. Each process is equipped with QC personnel, who can keep an eye on product quality.
▪DIP production line: We have two wave-soldering machines, among which there are more than 10 old employees who have worked for more than three years. The skilled workers can weld all kinds of plug-in materials.
2. Quality assurance, cost-effective
▪ High-end equipment can stick precision shaped parts, BGA, QFN, 0201 materials. Can also template patch, loose material hand.
▪ Sample and size batch can be produced, proofing from 800 yuan, batch 0.008 yuan/point, no start-up fee.
3. Rich experience in SMT and welding of electronic products, stable delivery
▪ Accumulated SMT SMT processing services for thousands of electronic enterprises, involving many kinds of automotive equipment and industrial control motherboard. The products are often exported to Europe and the United States, and the quality can be affirmed by new and old customers.
▪ On time delivery, normal 3-5 days after complete materials, small batch can also be expedited on the same day shipment.
4. Strong maintenance ability and perfect after-sales service
▪ Experienced maintenance engineers can repair all kinds of patch welding caused by bad products, to ensure the connection rate of each piece of circuit board.