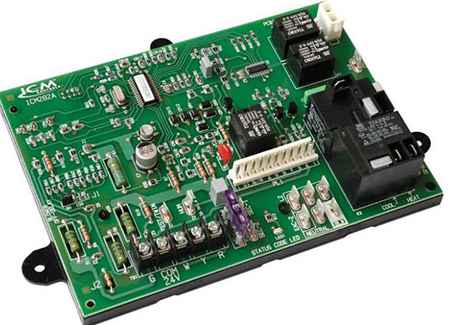
Overview of PCB assembly documentation
PCB assembly is a very precise and highly technical process. To ensure that the final product fully conforms to each specification, manufacturers rely on extensive documentation provided by customers. Although documentation is often used by manufacturers, customers, especially new customers, may need some guidance on what information to provide and when. In this overview of PCB assembly documentation, we list the required documentation for most manufacturers and outline the benefits of a complete documentation package.https://www.kingfordpcb.com/yuan.php
Overview of PCB assembly documentation
PCB assembly projects require a myriad of specifications. Of course, manufacturers can make high quality PCBS, but even the best boards must meet customer requirements to be useful. Documentation packages protect both parties and make assembly as smooth as possible. By providing written instructions, the customer can determine expectations for the final product. Manufacturers strictly follow specifications to ensure that customers receive their requirements accurately. Documentation can eliminate any speculation or misunderstanding that may occur during a verbal agreement.
Although requirements may vary slightly from manufacturer to manufacturer, most documentation is fairly standard for the industry. These include:
CAD files in ODB ++ use full documentation to get quotes. This will ensure that prices and schedules are accurate. What's more, manufacturers only need to enter the specifications once to greatly reduce the risk of human error.
Regardless of project size, each PCB component should meet several requirements specific to each customer and each project. Since precision is crucial, detailed, precise instructions are usually required during PCB assembly. Consider the types of documentation listed above when preparing the PCB assembly RFQ and build.
Defect Detection Strategy for Prefabricated PCBS By nature, PCB manufacturing is a very precise science with little margin for error. Therefore, a major requirement is to verify the electrical continuity of the board. There are two main ways to test these primitive plates. These include:
This way of working is to build test fixtures for specific PCB designs. The jig contains a number of spring-loaded test pins on the side, which is where the test is named. Press PCBS onto test pins and then check their conductivity. The test is known for its short test time.
Flying needle test
Flying needle test originated from bare plate test, involving short circuit, open circuit and other tests. The main parameter of the test is the resistance between the points. However, these tests have been developed to measure capacitance and inductance. In fact, this is what makes them effective for testing not only bare boards but also PCB components. Reasons for the widespread use of this test for defect detection include:
They are cost effective.
They have fewer accessibility problems than ICT testers. Because the movement of the probe is controlled by software, the changes are easy to implement.
They provide better test coverage than ICT tests.