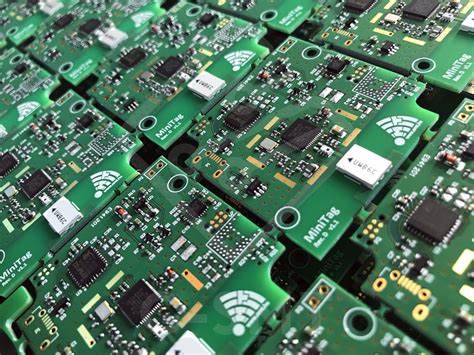
RF Traditional Printed Circuit Board (PCB) Fabrication Method
At present, the plates I have come into contact with mainly include: FR4, RO 3003, RO 4350B, RT 5880, and ceramic substrates. Now integrate the information on the Internet and some of my own understanding of the board making process. If there is any error, please correct me.
First introduce a few concepts (all can be queried on Baidu for further detailed understanding):
Dielectric constant (Dk): The smaller the dk, the higher the signal propagation speed
Loss tangent (Df): The lower the df, the smaller the loss of signal propagation
Copper clad laminate: also called core board, the substrate covered with copper skin on the upper and lower surfaces
Prepreg (PP): required for the production of multi-layer boards, used to bond two copper-clad boards, mostly made of glass fiber
FR4: Epoxy-based flame retardant (Fire Retardent, FR) glass material, which is a relatively cheap substrate with a high df (0.03, at 1GHz)
RO3003: ceramic filled PTFE circuit material, dk3, df0.001
RO 4350B: hydrocarbon/ceramic laminate, dk3.66 df0.0037 (the recommended value for circuit design is that when we perform impedance calculation or HFSS simulation, the dielectric constant is designed according to 3.66 by default, but I don’t know the design value and The reason why the manufacturing nominal value differs so much, I hope someone will give an answer)
RT 5880: Glass fiber reinforced PTFE, flexible sheet, generally used in products that require micro-assembly, can be easily cut with a scalpel, and the price is more expensive. dk2.2 df0.0004
There is another kind, Al2O3 ceramic substrate, its dk9.6~9.8 (it seems that the dk is different with the content of Al2O3), generally for some microstrip filters and microstrip bridges, compared with other plates, its advantages are: Realize a circuit with a smaller area, easy to correct and replace (because the simulated microstrip filter may have a center frequency shift, if it is placed on a board with other circuits, if the center frequency is shifted, it may cause the entire board Scrap); but the disadvantage is that the ceramic substrate processing manufacturers I have contacted before need to put together a lot of ceramic substrates to make up an area for processing. Generally, it is likely to use 20~30 boards to make enough. If you There are many types of needs that are suitable for self-assembly. If you wait for the manufacturer to help you assemble the board, the delivery date will be delayed (once, it seems that it was reported that the assembly was completed and started processing after a month of submission. Fortunately, I was only designing and verifying at the time, and did not submit goods); my former leader was directly rich and powerful, sometimes without waiting for the manufacturer to fight, remember to vote for two kinds of filters at a time, a total of more than 30 pieces were put together to meet the processing requirements, and the price is more than 2000, but in fact we only need each filter 2, if the product is not in quantity, this approach is indeed too costly.
Generally, strong printed boards, such as FR4, 3003, 4350B, etc., can be directly fixed on the cavity by screws, or can be sintered on the cavity by solder paste according to heat dissipation requirements. Sheet thickness is generally a multiple of 0.254mm (10mil).
Soft boards, such as 5880, are generally sintered on the cavity through tin; they can also be sintered on a carrier plate of a few mm, and then fixed on the cavity by screws as a hard printed board. Sheet thickness is generally a multiple of 0.127mm (5mil).
Like alumina ceramic substrates, it is necessary to use gold-germanium alloy and tungsten-copper carrier for eutectic sintering. Sheet thickness is 0.254mm/0.381mm.
Generally, I will use FR4 to make the control board (it needs to be considered separately when there are high-speed signals and RF mixing), and the RF board of the frequency band below ku uses RO4350b, and the RF board above ku uses RO3003 and RT5880. My current unit doesn't use 5880, and I will use taconic's RF35 when it reaches a certain frequency.
Sometimes multi-layer boards use mixed pressure. For example, if the top layer uses radio frequency lines, then the first layer to the second layer will use 3003, 4350B and FR4 for lamination. Not to mention four-layer boards, each layer requires guaranteed use RF sheet.
Multilayer boards also need to pay attention to the symmetrical design when designing the thickness of the stack. For example, for a six-and-a-half-layer board, the thickness of the boards from the first layer to the second layer should be the same as the thickness of the boards from the fifth layer to the sixth layer, so as to avoid deformation and warping of the board after processing. But it seems that it is not absolute. There are engineers in my current unit who do not require symmetrical design.
When specifying the total thickness of the PCB, it is also necessary to note that generally we specify the thickness of the board, which is only the thickness of the medium, and does not include the copper thickness of the upper and lower layers of the copper clad copper. Generally, we choose 1oz (0.036mm) or 1/2oz (0.018mm), these need to be calculated, and the thickness of the green oil must be added.
Regarding the current process capability of PCB, different manufacturers have different capabilities, and it is necessary to select the corresponding PCB manufacturer for processing according to the needs. Pay attention to the PCB that needs to be pressed with gold wire, you must pay attention to the thickness of the gold layer, it seems that if the gold layer is less than 2um, there will be no gold wire.