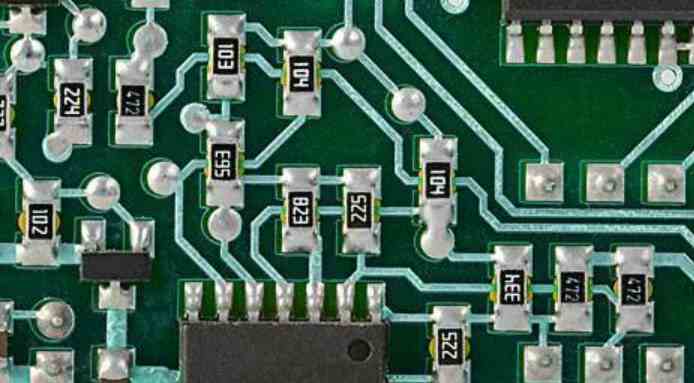
In recent days, smog weather has twice plagued northern China, Beijing for the first time launched a red alert for smog, and cars began to implement odd-even license plate restrictions. The domestic board industry believes that due to the serious pollution of coal, fuel, gas and other emissions, low-carbon travel and new energy vehicle consumption will once again become the focus of public attention.
In response to the attack of haze, Hu Zhenmin, a senior engineer at Zhejiang University, believes that the repeated harassment of haze is related to China's energy consumption structure, without adjusting the energy consumption structure dominated by fossil energy, it is difficult to change the trend of high pollutant emissions. Under the heavy pressure of smog, the development of new energy vehicles is inevitable.
Since 2014, The State Council has issued the "Guiding Opinions on Accelerating the Promotion and application of New Energy Vehicles", and some cities have introduced supporting measures such as free license plate fees, unlimited license plates and subsidies, promoting the explosive growth of new energy vehicle consumption. According to the statistics of the China Association of Automobile Manufacturers, from January to September this year, the cumulative production of new energy vehicles was 156,200, an increase of nearly three times year-on-year. Among them, 65,500 pure electric passenger cars were produced, a year-on-year increase of 2 times, and 38,500 plug-in hybrid passenger cars were produced, a year-on-year increase of 3 times.
PCB copy board reverse research and development, help new energy vehicles take off
Under the situation of actively encouraging new energy vehicles in China, the development of new energy vehicles has an excellent industrial environment. However, in terms of core technologies, how to improve the use and endurance performance of domestic new energy vehicles will become the key to the success of industrial development. In order to solve the lack of core technology and seek new technological breakthroughs, domestic new energy vehicle manufacturers have begun to cooperate with domestic reverse research and development institutions to seek breakthroughs in core technologies of new energy vehicles.
Hong Yunlai Electronics said that domestic new energy vehicles started relatively late, and most of the core technologies are far less than foreign countries, resulting in domestic new energy vehicles unable to successfully occupy the domestic market. In addition, the high cost of construction also directly restricts the popularity of domestic new energy vehicles. Therefore, we can use reverse research and development technology to carry out PCB copying research, and we can seek new ways to reduce production costs while referring to foreign advanced technology.
Hongyunlai Electronic reverse R & D Center has a professional PCB board team, has rich experience in PCB board modification, PCB design, secondary development, and its board products involve communications, radar, automotive, medical, aerospace and other fields. Recently, Hongyunlai Electronic reverse research and Development Center has reached cooperation with a number of domestic new energy vehicle manufacturers to provide a complete set of core technology and product secondary development solutions.
If necessary, you can also add optical character recognition (OCR) and Optical Character verification (OCV) in steps 2, 3, and 4.
The pros and cons of different inspection methods are endlessly discussed by engineers and manufacturers, but the main criteria for selection should focus on the type of component and process, the fault spectrum, and the requirements for product reliability. If you use many BGA, chip-level package (CSP) or flip chip components, you need to apply the inspection system to the first and second steps to get the most out of it. In addition, testing after the fourth stage can effectively find the defects of low-grade consumer goods. For PCBS used in the field of aerospace, medical and safety products (automotive air bags), due to the very strict quality requirements, it may be required to test in many places on the production line, especially after the second and fourth steps. For this type of PCB, X-rays can be used for detection.
If you want to evaluate the AOI used on the production line, you need to distinguish between systems that can only be inspected and systems that can be measured.
Inspection systems that can only look for defects such as missing components, misplaced locations, etc., do not provide tools for process control, so they cannot be used to improve the PCB production process. Engineers still have to adjust the production process manually. However, these detection systems are fast and cheap.
On the other hand, the measurement system can provide accurate data for each component, which is very important for measuring production process parameters. These systems are more expensive than inspection systems, but when you integrate them with SPC software, measurement systems can provide the information necessary to improve the production process.
In general, it is not comprehensive to evaluate the quality of a detection system based solely on its accuracy rate of error reporting, that is, the ratio of true errors (accurate errors) to false positives (false errors). If a measurement system is to be evaluated, it must also be based on an evaluation of the accuracy of the measurement system within a narrow tolerance range.
Statistical process control
Finally, if you want to use the data from the AOI system to effectively help you control the production process, so that the company can achieve higher production and higher profits, you must have the following information:
Accurate measurement data
Reproducible, repeatable measurements
Measurement of proximity to events in time and space
As well as real-time measurement process and all information about the production process
By installing AOI systems during printing or mounting, you can help eliminate other process variables that accumulate during production. If you measure whether the component has shifted position after reflow soldering, the data you collect does not reflect the accuracy of the mounting process. You should measure the results both after mounting and after reflow soldering. But this information is almost useless for controlling device mounting. Given the monitoring trend, installing an AOI system near the process you must monitor can quickly correct a parameter that moves to the next step, while close inspection can also reduce the number of PCBS that do not conform to specifications before the inspection process.
Although most AOI users in the electronics industry still focus only on post-weld inspection, the future miniaturization of components and PCBS will require more effective closed-loop process control. AOI systems that provide efficient inspection and measurement solutions will attract more and more users, and engineers will see the investment in such systems as more worthwhile. For all our customers, AOI will continue to play an important role in improving product lines and increasing yield.