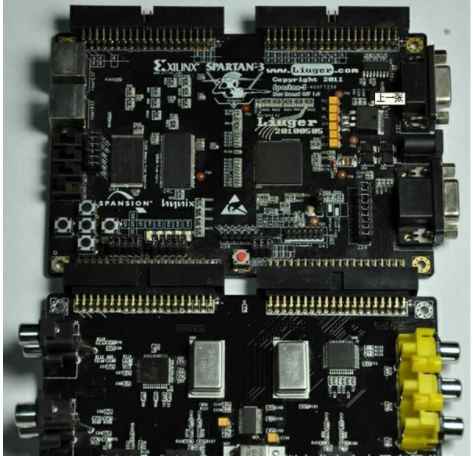
A collection of examples of printed circuit boards (PCBS) from professional pcba proofing manufacturers
(1) Roller mounting quality evaluation Industries: Displays, printed circuit boards, lead frame challenges: Lamination defects occur if the rubber has poor adhesion to the steel core of the laminate roller, or if the rubber is damaged.
Benefits of Prescale: Save time, improve quality
(2) Measurement of scraper pressure distribution during solder paste printing
Industry: Printed Circuit Board (PCB) electronic component installation challenges: When screen printing paste solder onto a printed substrate, any inhomogeneity in the scraper pressure distribution will result in uneven application of paste solder.
Benefits of Prescale: Save time, save materials, improve quality (3) Check the adhesive pressure of dry film resist (DFR) laminating industries: printed circuit boards (PCBS), lead frames, liquid crystals, etc
Challenge: If the base material/dry film resist/laminate roller is not balanced or the pressure is not properly adjusted, bubbles and wrinkles can form.
Benefits of Prescale: Save time, save materials
(4) Check the mold contact and pressure uniformity of the laminating machine or laminating machine
Industry: Laminated ceramics, ceramic substrates and packages, PCBS, electronic components for automotive and mobile phones, manufacturing challenges for laminated devices: need to be pressed with extremely high precision to avoid changes in electrical characteristics due to problems of poor adhesion or uneven thickness, and to avoid electrical connection failures due to shifting electrode patterns.
Benefits of Prescale: Increased yield, improved quality, and improved accuracyhttps://www.kingfordpcb.com/yuan.php
(5) Pressure uniformity verification of vacuum hot pressing devices Industries: electronic components, OLeds, touch screens, printed circuit boards, semiconductor devices used for manufacturing and development machines, etc
Challenge: Equipment is expected or required to maintain as uniform surface pressure as possible to improve the quality of processed products.
Benefits of pre-scale: Reduce pressure failure or yield and improve quality
A few years ago, a colleague contacted me with a question: "How can we weld a plate with a Tg of 180°C or even 200°C at 225-245°C without damaging the plate?" Even with lead boards, the peak reflux temperature is much higher than the Tg of the board. How is that possible?"
The answer is simple. Every time a printed circuit board is exposed to welding temperatures, it breaks. This applies not only to lead-free welding applications, but also to eutectic welding composed of tin lead. Tg is one of several parameters to pay attention to. In the case of Tg, many designers refer to this value as a measure of stability. High Tg products have less thermal expansion on the Z axis. Below Tg, the laminate epoxy system is hard and strong. You can expect a thermal expansion rate of about 25 ppm /°C. Above Tg, the epoxy becomes soft and flexible. Compared to the expansion rate of less than Tg value, the expansion rate can be up to 10 times the expansion rate when the epoxy resin is soft and flexible.
The parameter that best determines when a board begins to experience thermal damage is called the maximum continuous operating temperature (MOT). MOT is a parameter tested and certified by Underwriters Laboratories (UL). Bare plate manufacturers should go through their most disruptive process to construct a qualified sample and submit it to UL for compliance testing. Boards with a certified MOT of 130°C will not cause thermal damage in the field when exposed to temperatures of 130°C or lower. Above the MOT value, the epoxy resin made of the PCB begins to decompose at the molecular level. As molecular bonds break due to thermal stress, energy is released. The energy released shows up as smoke. The higher the temperature the board is exposed to, the faster the damage occurs. The damage is cumulative.
The drying and baking moisture on the PCB is well demonstrated to be the damage threshold. For PCBS, the dry baking temperature must be higher than the boiling point of water (100°C) but lower than the MOT. In theory, you can dry a circuit board with a MOT of 120°C at 110°C for a year, and the epoxy resin from which the PCB is made will not suffer thermal damage. Similarly, if the dry baking temperature is 121°C, the epoxy will begin to suffer damage. One degree above MOT, in theory, could take months to do real damage. At 300°C, PCB damage is so rapid that delamination occurs in less than a minute. The higher the temperature, the less time it takes to burn off the epoxy from the PCB. In fact, the MOT is the test value. The actual PCB may exceed this value by several degrees.