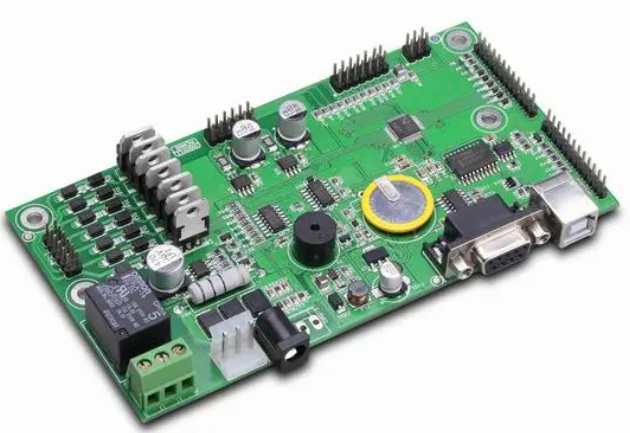
Design tips for different types of PCBA manufacturing
Various factors affect the use of devices in electronic devices, such as performance, environment, and functionality. These same parameter types affect the PCB constructionprocess. Based on a clearly defined set of steps, manufacturing boards for critical applications such as aerospace, automotive, and industrial applications requires considerations that go beyond what is typically required for commercial electronics.
Let's take a look at these different PCBA manufacturing types based on the application and establish design tips to ensure that your board meets the requirements of its intended use.
The world's leading associations help manufacturers build better electronics through reliable certification, education and training standards, innovative solutions, thought leadership, advocacy and industry wisdom. IPC (Connected Electronics Industry Association).
IPC standards include category identification for various electronic devices, such as the IPC-6011 standard. Overall, this classification system contains three general categories that reflect the progressive increase in complexity, functional performance requirements, and frequency of tests and inspections.
These three categories indicate the level of quality each type of board should be built, and the classification that CM must follow when developers build PCBS themselves.
IPC Category 1 includes general-purpose electronics such as computers (desktops and laptops), computer peripherals, and consumer products. In all cases, these devices are suitable for applications where cosmetic defects exist, and the main requirement is the functionality of PCBA.
2.IPC Class 2 applies to specialized service electronics, such as complex business machines, instruments and communication equipment. These are devices that require extended life and high performance. Although this classification requires uninterrupted service, it is not a critical requirement and also allows for certain appearance defects.
3.IPC Class 3 is suitable for electronic products in harsh working environments that require high reliability. In addition, this class includes equipment and equipment that must provide on-demand performance or continuous performance. In addition, these devices or devices have zero fault tolerance for downtime and must be executed when needed. Examples of such devices, devices, or systems include space applications such as NASA oxygen generation systems, flight control systems, and life support systems. In summary, PCBA in this category is suitable for applications that are critical to the service and require a high level of assurance.
It is important to note that the final performance rating (assembly, welding, cleaning and testing) of a PCBA cannot be higher than the performance rating specified for a bare board or prefabricated PCB. Therefore, to obtain a Class 3 PCBA, IPC Class 3 must be specified for manufacturing.
The classification system of various products is strictly followed by strict design considerations. Here are three industries that meet the IPC-6011 standard. We'll start with a 3 category breakdown that includes mission-critical equipment and systems and the most stringent guidelines. Moreover, there is no industry more dependent on its equipment and programs. Aerospace, of course, except in the medical field.
Aerospace applications
1. Reliability is key: this means zero tolerance for failure and extended life cycle. Therefore, designers and manufacturers need to avoid using any cutting-edge technology when designing and manufacturing PCBS and adhere to standard, proven technologies. 2. Use heavy copper: In space, they control heat by dissipating heat. Therefore, when building for these applications, use a heavier copper design, that is, 4 or 5 ounces of copper with thermal through-holes, and utilize the case for heat dissipation. PCB include
3. Material selection: Use polyimide (wood), especially in applications requiring extended service life (i.e., more than two or three years). The advantages of using polyimides on your excellent flexibility, excellent tensile strength, thermal stability, high durability and chemical resistance.
4. Assembly process and surface finish: HASL (Hot air solder leveler) containing lead is used during assembly, for example, ENIG can be used for surface finish.
IPC 6012DS: Always refer to this standard as it is technically an enhanced IPC Category 3. For military and space applications, it is also release requirements, quality requirements, minimum plating, etc.
The automotive industrPCB industryy continues to move toward electric and autonomous vehicles on its own path. Only through the , it is possible to achieve growth. In addition, the need for thermal resistance and longevity makes automotive PCBS different from other industries. Adherence to IPC-6012DAIATF 16949 (ISO 9001 Automotive standard) is a key manufacturing requirement. Here are design and manufacturing tips for the automotive industry:
1. If no other specifications are available, use Class 3 specifications for all board features.
2. Spacing and pad specifications are within the IPC-6012DA tolerance standard.
3. Drilling shall meet the dimensions and quality requirements of IPC-6012DA and comply with the equipment aspect ratio of the contract manufacturer.
4. Solder resistance film specifications must meet the tolerance standard of IPC-6012DA.
5. Ensure that your CM applies reasonable quality control, including automatic Optical inspection (AOI) for appearance checks throughout the assembly and manufacturing process.
6.CM shall adhere to strict cleanliness guidelines and clean the board after each operation to avoid excessive debris, including before and after the solder mask.
With Industrial PCBA, we embed boards into broader industrial production systems. In addition, these boards are usually custom made or have special requirements. Here are some tips to watch out for:
1. Use conformal paint (IPC-CC-830C standard) to protect the board from moisture and debris.
2. Selection of materials: mechanical, thermal and electrical properties of materials should be considered when selecting. Also, make sure the PCB type can withstand the structure, heat or heat. Possible high speed industrial environment challenges.
3. Use proper wiring to ensure proper copper wire weight, impedance and length. Proper wiring translates to signal integrity and the necessary current-carrying capability.
4. Tests: These types of tests include the resistivity of solvent extraction tests (crumbs), AOI (solder joints and component placement) and stripping tests (adhesion).
5. Use DFM inspection and simulation to analyze the power transmission network (PDN) and thermal resistance of the board.
The expected environment of PCBA determines the expected level of quality, performance, functionality, and lifecycle. For critical applications, design for harsh environmental conditions is often required. Beat Automation works with PCBA manufacturing partners who are able to meet these stringent requirements and, together with assembly boards, meet standards at any classification level.