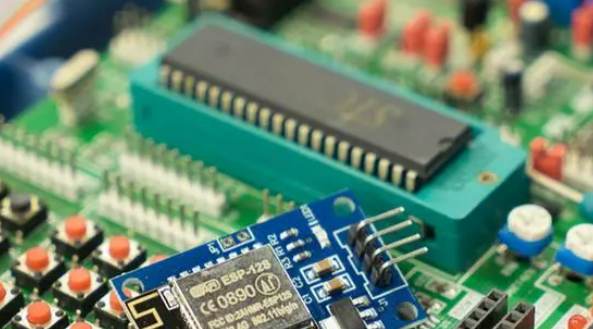
Single-sided soft PCB, only one layer of conductor, the surface can have a covering layer or no covering layer. The insulating base material used varies with the application of the product. Commonly used insulation materials are polyester, polyimide, polytetrafluoroethylene, soft epoxy-glass cloth and so on.
Single-sided soft PCB can be further divided into the following four categories:
1) Single-sided connection without covering layer
The wire pattern of this kind of soft PCBis on the insulating substrate, and the surface of the wire is not covered. Like the usual single-sided rigid PCB. This type of product is one of the cheapest and is usually used in non-critical and environmentally friendly applications. The interconnection is achieved by solder welding, fusion welding or pressure welding. It was commonly used in early telephone sets.
2) There is a covering layer single-sided connection
Compared with the previous class, this type only provides a layer of covering layer on the surface of the wire according to customer requirements. When covering, the pad should be exposed, and the end area can be simply not covered. Requiring precision can be used in the form of clearance holes. It is the most widely used and most widely used single-sided soft PCB, and is widely used in automotive instruments and electronic instruments.
3) Double-sided connection without covering layer
This type of connecting disk interface can be connected on the front and back of the wire. In order to do this, a channel hole is cut in the insulating substrate at the pad, which can be first punched, etched or made by other mechanical methods at the desired location of the insulating substrate. It is used for double-sided mounting elements, devices and where soldering is required, and the pad area at the path is free of insulating substrate, such pad area is usually removed by chemical methods.
4) Double-sided connection with a covering layer
This class differs from the previous class in that the surface has a covering layer. However, the covering layer has access holes, which also allow both sides to be terminated and still maintain the covering layer. This type of soft PCB is made of two layers of insulating material and one layer of metallic conductor. It is used in cases where the covering layer needs to be insulated from the surrounding device, and itself needs to be insulated from each other, and the ends need to be connected both front and back.
What is the difference between SMT inductors and SMD inductors
1, surface mount technology SMT
Surface Mount Technology, known as "Surface mount technology" in English, referred to as SMT, is a circuit mounting technology that attaches surface mount components and welds them to the specified position on the surface of the printed circuit board. Specifically, first, solder paste is coated on the printed board circuit plate, and then the surface mount components are accurately placed on the solder paste coated pad, by heating the printed circuit board until the solder paste melts, and after cooling, the interconnection between the element and the printed board is realized. In the 1980s, SMT production technology is becoming more and more perfect, the mass production of components for surface mounting technology, the price has dropped significantly, a variety of technical performance, low price equipment have been available, electronic products assembled with SMT have small size, good performance, full function, low price advantages, so SMT as a new generation of electronic mounting technology, It is widely used in the installation of electronic products in various fields such as aviation, aerospace, communications, computers, medical electronics, automobiles, office automation, household appliances, etc.
2. SMD Surface Mounted Devices
"In the initial stage of electronic circuit board production, through the hole assembly is completely completed by manual. When the first automated machines were introduced, they could place some simple pin components, but complex components still needed to be placed manually for wave soldering. Surface mount components were introduced about twenty years ago and ushered in a new era. From passive components to active components and integrated circuits, all eventually become surface mount devices (SMDS) and can be assembled by pick-up and drop devices. For a long time it was thought that all pin components could eventually be packaged in SMD.