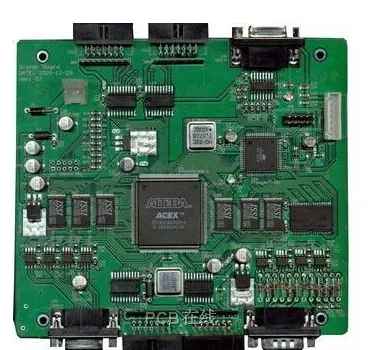
How many steps does PCBA process product rework?
In the manufacturing process of electronic products, PCBA processing is an important step. However, in the PCBA process, if there are some problems, then it needs to be reworked. Rework is a necessary work that can take some time and cost, but it can help manufacturers solve many quality problems of electronic products and improve the stability and reliability of products. So, what are the steps in the process of reworking PCBA processed products?
Step 1: Identify quality issues
Before reworking PCBA processed products, it is first necessary to identify the quality problem. This can help manufacturers deal with problems more effectively and improve the efficiency of rework. The problem can be determined by some fault analysis test equipment. Fault analysis test equipment is an electronic test equipment that can help manufacturers determine the fault point of electronic equipment, quickly find out the cause of the failure of electronic products, and improve the efficiency and accuracy of maintenance and rework.
Step 2: Prepare spare parts
After determining the cause of the failure of the electronic product, the manufacturer needs to prepare spare parts. Spare parts include spare components and solders. The quality of spare parts preparation directly affects the success or failure of rework, so manufacturers should try their best to prepare spare parts to ensure the quality and quantity of spare parts, and be more handy in the rework process.
Step 3: Rework operation
The rework operation is a very critical step, and the process needs to be taken seriously by the manufacturer. Before the rework operation, a variety of test equipment is needed to detect, confirm the fault point of the electronic equipment, and carry out the corresponding maintenance treatment. In the process of rework operation, it is necessary to complete the installation, welding, and insertion of components according to the PCB drawings and component manuals, so as to ensure that the electronic equipment after rework can meet the manufacturing standards and ensure product quality.
Step 4: Test acceptance
After the rework operation is complete, some test acceptance work needs to be done. This can help manufacturers determine the effect of rework, test the quality of electronic products, and verify the reliability of products. Test acceptance can be carried out by a variety of test means, such as circuit board tester, constant temperature and humidity test box.
The above is all the steps of PCBA processing products rework, each step is very important, so as to ensure the quality and stability of electronic products. Manufacturers can adjust these steps according to the actual situation to meet specific production needs.
First: the correct selection of PCB materials.https://www.kingfordpcb.com/yuan.php
When starting manufacturing, the organization or company needs to choose a high-quality PCB material. You can ensure that the PCB materials you are using are of high quality by talking to your suppliers. The thermal expansion coefficient of PCB material is very important, if the selected material thermal expansion coefficient does not match, it will lead to plate bending and plate warping. Therefore, the use of PCB materials with matching thermal expansion coefficient can reduce the probability of bending and warping of the plate during the welding process.
Second: Determine the correct PCB thickness.
As with PCB materials, the correct selection of PCB thickness is also very important. If the PCB thickness is too thin, it may lead to bending and warping of the board. On the contrary, if the PCB thickness is too thick, it will lead to poor welding and increase its weight and cost. When determining the PCB thickness, the PCB material and welding process must be considered, and determining the correct PCB thickness can help reduce the probability of bending and warping the board.