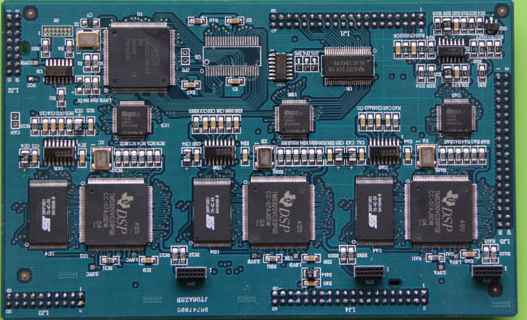
The causes and solutions of PCBA welding point pulling
PCBA welding tip machining has always been a common concern in the electronics industry. With the gradual popularization and upgrading of the application of electronic products, the quality of solder joints has become more and more important in the process of electronic production, and adverse phenomena such as pulling the tip have seriously affected the quality and service life of electronic products. This paper will introduce the causes and solutions of PCBA welding joint pulling, in order to help the electronics industry to better solve this problem.
First, the cause of the solder joint tip
1, PCB board production process
In the production process of the PCB board, copper foil is usually used as a conductive layer, and the surface of the copper foil is coated with a protective film for etching. If there are problems in the production process, such as incomplete or excessive etching, it will cause the surface of the copper foil to be uneven and the solder joint to produce a pull point.
2. The leading end of Component is connected with the The tip of the solder joint may also be related to the poor connection between the leading end of the Component and the PCB pad. If the connection is poor, it will lead to the internal solder joint is not tight enough, and when the solder joint experiences temperature changes or is subjected to external pressure, it is prone to problems such as pinching.3, process and equipment selectionPCB pad
In the processing of solder joints, the use of organic green printing ink/chemical gold plating and other unsuitable technologies and processes will also cause the solder joints to pull. Especially in the processing of high-density PCB board, if the feeding is not accurate or the printing is not in place, the solder joint will be pointed.
4. Environmental issuesIt is rare that the solder joint is pointed due to environmental problems. However, some ultra-quiet environments require the use of large air conditioning and dehumidification equipment, which makes the site comfortable and hygienic to achieve the best state, but at the same time, the welding reflux and annealing equipment are affected, indirectly leading to the occurrence of solder joints
Second, how to better solve the PCBA processing solder joint tiphttps://www.kingfordpcb.com/yuan.php
1. Choose the right process and equipment
Choosing the right process and equipment for welding is the key. Common processes are manual welding and machine welding. Machine welding speed, high degree of automation, suitable for mass production; The manual welding precision is high, suitable for small batch, repair and non-standard products. If you want to deal with high-precision electronic products, the use of machine welding is a more ideal choice.
2. Standardized operation process
The operating process is also very important when processing and welding PCB boards. It is necessary to choose standardized operating processes and standardized processes to avoid the occurrence of problems such as solder joint pulling caused by improper operation.
3. Advanced welding technology
The use of advanced welding technology can also reduce the problem of solder joint tip. For example, the use of flow melting point solder, to ensure the internal integrity and uniformity of the solder joint, while reducing the production of solder joint tension. 4. Balance strength and toughness
In view of the problem of solder joint tip, it can also be solved by balancing the strength and toughness of the solder joint. For example, using a thicker pad and increasing the thickness of the inner copper layer can improve the toughness of the solder joint while ensuring the strength of the solder joint, and effectively avoid problems such as pulling the tip of the solder joint. In SUMMARY:
PCBA welding tip pulling is a common problem in electronic production, but by selecting the appropriate process and equipment, standardized operation process and advanced welding technology, the occurrence of welding tip pulling can be avoided. In practice, mastering technology, strengthening management, and reducing the occurrence of such problems can effectively improve the quality of electronic products and enhance the service life of products.