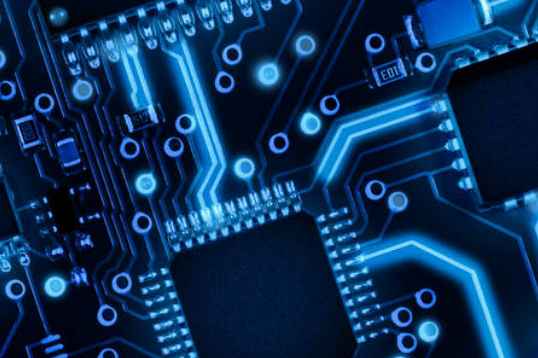
With the rise of industrial automation and intelligent manufacturing, the industrial robot market has also begun to show a significant upward trend. According to the statistics of the International Robot Association, in 2014, the sales of industrial robots in the world increased by 27%, and the sales of industrial robots in the Chinese market increased by 54%. Domestic enterprises believe that industrial robots are becoming intelligent and high-end development, and the lack of domestic core technology will once again become an obstacle to the rapid rise of domestic industrial robots.
Core technologies are seriously missing, and 90% of key components are imported
The robot industry divides the entire industrial chain into three levels: upstream is the core parts, mainly reducer and control system, which is equivalent to the "brain" of the robot; The middle stream is the robot body, that is, the "body" of the robot; Downstream is the system integrator, relying on upstream and midstream core equipment to do the finished product.
According to statistical analysis, not only the Pearl River Delta region, but also 90% of the domestic robot enterprises are in the downstream link, and the industrial chain shows the characteristics of "huge downstream, scattered in the middle, and missing upstream". Due to the lack of core technology, many general-purpose precision parts, such as guideway, reducer, servo motor, etc., rely heavily on imports.
PCB copy boardredevelopment, local robots to highlight the encircling
In order to solve the embarrassing situation of the lack of core technology and the dependence of key components on imports, domestic robot companies have begun to find a new breakthrough. The domestic professional PCB copying board enterprise Bang Kai technology said that the use of reverse research and development technology for PCB copying board redevelopment can quickly obtain the production technology of core components, so as to break the monopoly of foreign countries, reduce the cost of robot production, and find a way out for domestic robots.
However, due to the surge in demand for domestic industrial robots, a number of international robot companies have begun to cooperate with Chinese companies to set up production bases in China and lay out the domestic market in advance. To this end, once the domestic robot enterprises can not make a breakthrough in the core technology, it will lose competitiveness in the international robot enterprises to enter the frenzy, and fall into the trough again.
Therefore, our PCB copying board research in the field of industrial robots needs to get rid of the drawbacks of traditional technology cloning, increase independent research and development efforts, take the international core technology as a reference for PCB revision and secondary development, complete new breakthroughs in core technology, in order to highlight the encircling industrial robot market in the future and usher in a new round of development opportunities.
The principle of capacitor voltage reduction in LED drive power supply is briefly analyzed
As far as the current domestic LED driver power supply design trend is concerned, the products that use the capacitor step-down principle to complete the driver circuit design have gradually established a firm foothold in the market. LED power supply products with this design have better stability and lower cost. In today's article, we will carry out a brief analysis and introduction of the capacitor step-down principle in the LED driver power supply.
In the LED drive power circuit made of capacitor buck principle, the block diagram of the buck principle is shown in the figure below. When a sinusoidal AC power supply U(here the most common 220VAC, 50HZ for example) is applied to the capacitor circuit, the charge on the two plates of the capacitor and the electric field between the plates are a function of time. That is to say: the effective value and amplitude of voltage and current on the capacitor also follow Ohm's law. That is, when the voltage added to the capacitor has a certain amplitude and a certain frequency, it will flow through a stable sinusoidal AC current ic. The smaller the capacitive reactance, the larger the capacitor value, the larger the PCB proofing current flowing through the capacitor, and a suitable load in series on the capacitor, you can get a reduced voltage source, which can be rectified, filtered, and voltage stabilized output. A problem to note here is that in this circuit system, the capacitor only absorbs energy in the circuit, but does not consume energy, so the efficiency of the capacitor step-down circuit is very high.
Under normal circumstances, the LED power supply designed by the principle of capacitor buck, its main drive circuit will be composed of buck capacitor, current limiting, rectification filter and voltage regulator shunt circuit. Among them, the step-down capacitor is equivalent to the step-down transformer in the ordinary voltage regulator circuit, which is directly connected to the AC power supply circuit, almost all the AC power supply U, and non-polar metal film capacitors should be selected. At the moment of closing the power supply, the PCB manufacturing may be a positive or negative peak-peak of the U half week, at this time the instantaneous current will be large, so a current limiting resistor needs to be connected in series in the loop to ensure the safety of the circuit, which is the main reason why the current limiting circuit is essential. The design requirements of the rectifier filter circuit are the same as those of the ordinary DC regulated power supply circuit. The reason why the voltage regulator shunt circuit is needed is because in the voltage step-down circuit, the current RMS value I is stable and is not affected by the load current size change, so in the voltage regulator circuit, there should be a shunt loop to respond to the load current size change.