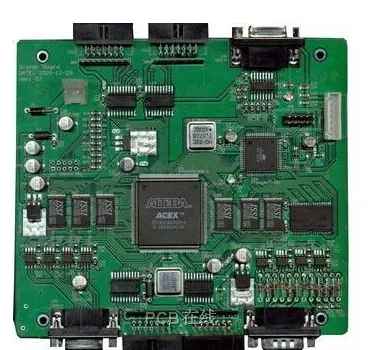
PCBA is the production process of PCB empty board first through SMT parts, and then through DIP plug-in, which involves a lot of fine and complex process flow and some sensitive components. If the operation is not standardized, it will cause process defects or component damage, affecting product quality and increasing processing costs. Therefore, in PCBA processing, it is necessary to comply with the relevant operating rules and operate in strict accordance with the requirements.
Operating rules for PCBA processing
1, in the PCBA work area should not have any food, drink, no smoking, do not place non-work related debris, keep the workbench clean and tidy.
2, the surface of the PCBA patch to be welded must not be taken with bare hands or fingers, because the grease secreted by the human hand will reduce the weldability and prone to welding defects.
3. The operating steps of PCBA and components are reduced to a minimum to prevent dangers. In assembly areas where gloves must be used, soiled gloves can cause contamination, so replace them frequently if necessary.
4, do not use skin protection grease or various detergents containing silicone, which can cause problems in the solderability and bonding properties of the coating. Specially formulated detergents for PCBA welding surfaces are available.
5, EOS/ESD sensitive components and PCBA, must be marked with appropriate EOS/ESD logo to avoid confusion with other components. In addition, in order to prevent ESD and EOS from endangering sensitive components, all operation, installation and testing must be completed on the workbench that can control static electricity.
6. Check the EOS/ESD workbench regularly to confirm that they can work normally (anti-static). Various hazards of EOS/ESD components can be caused by incorrect grounding methods or oxides in the ground connection, so special protection should be given to the "third wire" ground terminal connector.
7. It is forbidden to stack PCBA, which will cause physical damage. Special brackets should be configured on the assembly working surface and placed according to type.
In the manufacturing of PCBA patch processing, these operating rules should be strictly observed, and the correct operation can ensure the final use quality of the product and reduce the damage of components. It can provide one-stop services from upstream electronic component procurement to PCB production and processing, SMT patches, DIP plug-ins, PCBA testing, finished product assembly, etc.
Our advantage
1. Strength guarantee
▪SMT workshop: With imported SMT machines, optical inspection equipment, can produce 4 million points per day. Each process is equipped with QC personnel, who can keep an eye on product quality.
▪DIP production line: there are two wave soldering, of which there are more than 10 old employees who have worked for more than three years. The workers have high proficiency and can weld all kinds of plug-in materials.
2. Quality assurance, cost-effective
▪ High-end equipment can be attached to precision shaped parts, BGA, QFN, 0201 materials. Also can be template patch, loose material hand.
▪ Sample and size batch can be produced, proofing from 800 yuan, batch 0.008 yuan/point, no start-up fee.
3. Rich experience in SMT and welding of electronic products, stable delivery
▪ Accumulated service for thousands of electronic enterprises, involving many types of automotive equipment and industrial control motherboard SMT processing services, products are often exported to Europe and the United States, quality can be affirmed by new and old customers.
▪ Punctual delivery, normal 3-5 days after complete materials, small batches can also be expedited on the same day.