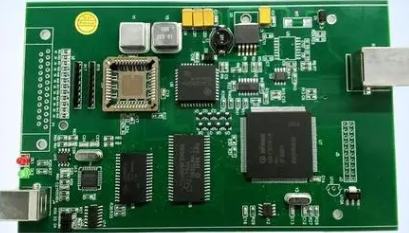
SMT refers to a series of process processes based on PCB, PCB (Printed Circuit Board) is a printed circuit board. SMT is the Surface assembly Technology (Surface Mounted Technology) (short for Surface Mounted technology), is the most popular technology and process in the electronic assembly industry.
The main characteristics of SMT patch processing
1, high density: Because the number of pins processed by the SMT patch is as high as hundreds or even thousands of pins, and the center distance of the pins can reach 0.3mm, the high progress BGA on the circuit board requires fine lines and fine spacing. The line width has been reduced from 0.2~0.3mm to 0.1mm or even 0.05mm, and the double lines between the 2.54mm grid have developed to 4, 5 or even 6 wires. Thin lines and fine spacing greatly increase the assembly density of SMT. In the case of high accuracy of the corresponding SMT patch processing equipment, the corresponding patch processing plant can be completed.
2, small aperture: most of the metallized holes in SMT are not used to insert component pins, and are no longer welded in the metallized holes, and the metallized holes are only used as an electrical interconnection between layers, so the aperture should be reduced as much as possible to provide more space for the SMT patch. The aperture has changed from 0.5mm in the past to 0.2mm, 0.1mm and even 0.05mm.
3, low coefficient of thermal expansion: any material will expand after heating. Polymer materials are usually higher than inorganic materials. When the expansion stress exceeds the bearing limit of the material, the material will be damaged. Because the SMT pins are too many and short, the CTE between the device body and the SMT is inconsistent, and the device damage caused by thermal stress often occurs. Therefore, the CTE of the SMT board substrate should be as low as possible to accommodate the match with the device.
4, high temperature performance is good: most of today's SMT circuit boards need to install components on both sides. Therefore, the PCB machined by SMT needs to be able to withstand two reflow soldering temperatures. At present, lead-free welding is widely used, and the welding temperature is high. After welding, the SMT chip circuit board is required to have small deformation, no foaming, the welding pad still has good weldability, and the surface of the SMT chip circuit board still has a high flatness.
1. Strength guarantee
▪SMT workshop: With imported SMT machines, optical inspection equipment, can produce 4 million points per day. Each process is equipped with QC personnel, who can keep an eye on product quality.
▪DIP production line: there are two wave soldering, of which there are more than 10 old employees who have worked for more than three years. The workers have high proficiency and can weld all kinds of plug-in materials.
2. Quality assurance, cost-effective
▪ High-end equipment can be attached to precision shaped parts, BGA, QFN, 0201 materials. Also can be template patch, loose material hand.
▪ Sample and size batch can be produced, proofing from 800 yuan, batch 0.008 yuan/point, no start-up fee.
3. Rich experience in SMT and welding of electronic products, stable delivery
▪ Accumulated service for thousands of electronic enterprises, involving many types of automotive equipment and industrial control motherboard SMT processing services, products are often exported to Europe and the United States, quality can be affirmed by new and old customers.
▪ Punctual delivery, normal 3-5 days after complete materials, small batches can also be expedited on the same day.
4. Strong maintenance ability, perfect after-sales service
▪ Experienced maintenance engineers can repair all kinds of patch welding caused by bad products, to ensure the connectivity of each circuit board.
▪ 24-hour customer service staff responds at any time to solve your order problems as quickly as possible.