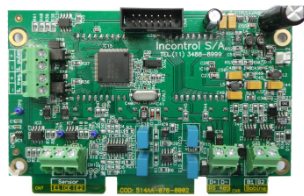
Manual welding is often needed in SMT processing plants, in order to make the object better welding must master the technical essentials of welding, then how to quickly master the technical essentials of manual welding?
The main tool for manual welding is the electric soldering iron, there are many types of electric soldering iron, according to the heating method, can be divided into direct heat, induction, constant temperature electric soldering iron, intelligent electric soldering iron, tin pump, hot air welding table, electric clamp and so on. Manual welding should first choose anti-static constant temperature electric soldering iron.
1, welding operation posture
(1) Welding distanceThe gas generated during welding will cause harm to the human body, so when using a soldering iron, the distance between the nose and the soldering iron should be more than 30cm, and 40cm is a more appropriate distance.
(2) Electric soldering iron grip
The soldering iron has three grip methods: reverse grip, positive grip and pen grip. The reverse grip is stable, and the operation is not easy to fatigue for a long time. It is suitable for holding the high-power soldering iron, and the positive grip is suitable for the operation of the medium-power soldering iron or the soldering iron with elbow.
2, welding five-step method
(1) Prepare for welding - clean soldering iron: add tin to the soldering iron head, clean the soldering iron head, which is conducive to heat conduction; Do not scrape the oxide layer of the iron tip with a knife or other object.
(2) Heating the weldment: place the soldering iron head at the connection point of the welded metal (the place with the greatest heat capacity); Heat begins to flow to the surface of the metal being welded.
(3) Solder wetting: the tin wire is placed between the connection point of the soldering iron head and the metal to be welded to form a thermal bridge; The flux flows in the cold direction and infiltrates the pad - from the tip of the soldering iron to the entire pad, removing the oxide layer and promoting heat conduction; When the solder wire is moved to the opposite side of the heat source, the molten tin flows in the direction of heat, infiltrates the pad and pin, and capillary phenomenon, diffusion, dissolution and metallurgical bonding occur at the interface; Push the flux residue towards the surface and edge of the solder joint.
(4) Withdraw the tin wire: evacuate the tin wire first, and then evacuate the soldering iron, otherwise the tin wire will solidified on the solder joint.
(5) Stop heating: cooling, solidification, forming solder joints; Note that when the tin wire is not fully solidified, do not shake the component and pcb to avoid virtual welding.
1.Maximum board: 310mm*410mm(SMT);
2. Maximum plate thickness: 3mm;
3. Minimum plate thickness: 0.5mm;
4. Minimum Chip parts: 0201 package or parts above 0.6mm*0.3mm;
5. Maximum mounting parts weight: 150g;
6. Maximum part height: 25mm;
7. Maximum part size: 150mm*150mm;
8. Minimum pin part spacing: 0.3mm;
9. Minimum ball part (BGA) spacing: 0.3mm
10. Minimum ball part (BGA) diameter: 0.3mm
11. Maximum part mounting accuracy (100QFP) : 25um@IPC;
12. SMT capacity: 300-400 Wandian Electronics Co., Ltd. specializes in providing overall PCBA electronic manufacturing services, including upstream electronic component procurement to PCB production and processing, SMT patches, DIP plug-ins, PCBA testing, finished product assembly and other one-stop services.