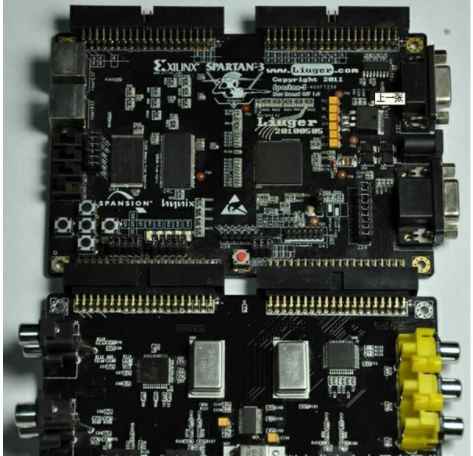
PCB as the core substrate of electronic products, its quality and reliability directly affect the quality and reliability of electronic products, for this reason, high-reliability PCB has become the basic requirements of many electronic products.
1, to achieve 25μm hole wall copper thickness can enhance reliability, including improved Z-axis expansion resistance;
2, the perfect circuit can ensure reliability and safety, high reliability PCB is generally no welding repair or break repair line, so that it can avoid the risk of circuit board break.
3, the residue on the circuit board, solder accumulation will bring risks to the welding layer, ionic residue will lead to welding surface corrosion and pollution risk, which may lead to poor solder joints/electrical failure and other reliability problems, and ultimately increase the probability of actual failure, beyond the cleanliness requirements of the IPC specification PCB can improve its reliability.
4, the surface treatment of the old circuit board will undergo metallogenetic changes, there may be solderability problems, and moisture intrusion may lead to delamination, inner layer and hole wall separation (break) problems in the assembly process or actual use, so the high-reliability PCB will strictly control the service life of each surface treatment.
5, poor mechanical properties mean that the circuit board can not play the expected performance under assembly conditions, such as high expansion performance will lead to delamination, breaking and warping problems. Weakened electrical characteristics can lead to poor impedance performance and other problems, therefore, high-reliability PCB factories will use internationally renowned substrates, such as Shengyi, Kingboard, Lianmao and other well-known brands, KINJI PCB factory is the use of these substrates, to ensure the high reliability of customers PCB products.
6, because the electrical performance may not meet the specified requirements, the output/performance of the same batch of components will be greatly different, high-reliability PCB factory will strictly control the dielectric layer thickness to reduce the expected value deviation of electrical performance.
7, poor quality ink can lead to adhesion, flux resistance and hardness problems. All of these problems can cause the solder stop layer to detach from the circuit board and eventually lead to corrosion of the copper circuit. Poor insulation characteristics can cause short circuits due to unexpected electrical connectivity/arcing. High-reliability PCB factories strictly define solder resistance materials to ensure compliance with IPC-SM-840ClassT requirements.
8, high reliability PCB will strictly define the shape, hole and other mechanical characteristics of the tolerance, very good to improve the size of the product quality - improve the fit, shape and function.
9, thin solder resistance layer can lead to adhesion, flux resistance and hardness problems, high reliability PCB factory NCAB specified solder resistance layer thickness, although IPC has no relevant regulations.
10, high reliability PCB factory defines the appearance requirements and repair requirements, in the manufacturing process to carefully care and carefully cast safety, to avoid a variety of scratches, small damage, repair and repair.
11, the depth of the jack has high requirements, the use of high-quality jack to reduce the risk of failure in the assembly process.
Surface process: spray tin, lead-free spray tin, sinking gold, full plate gold plating, plug gold plating, full plate thick gold, chemical sinking tin (silver), anti-oxidation (OSP) blue glue, carbon oil
▪ SMT workshop: With imported SMT machines and a variety of optical testing equipment, it can produce 4 million points per day. Each process is equipped with QC personnel who can keep a close eye on product quality.
▪ DIP production line: There are two wave soldering machines. Among them, there are more than 10 old employees who have worked for more than three years. Skilled workers can weld all kinds of plug-in materials.
Quality assurance, high cost performance
▪ High-end equipment can mount precision parts, BGA, QFN, 0201 materials. Proof can be machine paste, also can hand swing.
▪ Samples and large and small batches can be produced. Proofing starting price 800 yuan, batch starting price 0.008 yuan/point, no start-up fee.
Rich experience in SMT and welding of electronic products, stable delivery time
▪ Accumulated service for thousands of home appliance subsidiaries, involving various types of automotive equipment and industrial control motherboard SMT processing services. Products are often exported to Europe and the United States, and the quality is affirmed by new and old customers.
▪ On-time delivery, generally delivered within 3-5 days after the board is assembled, small batch expedited can also be shipped on the same day.
4. Strong maintenance ability, perfect after-sales service
▪ Experienced maintenance engineers can repair bad products caused by various welding problems, and can ensure the connectivity of each circuit board. ▪ 24-hour customer service staff will be ready to respond and resolve your order as soon as possible.