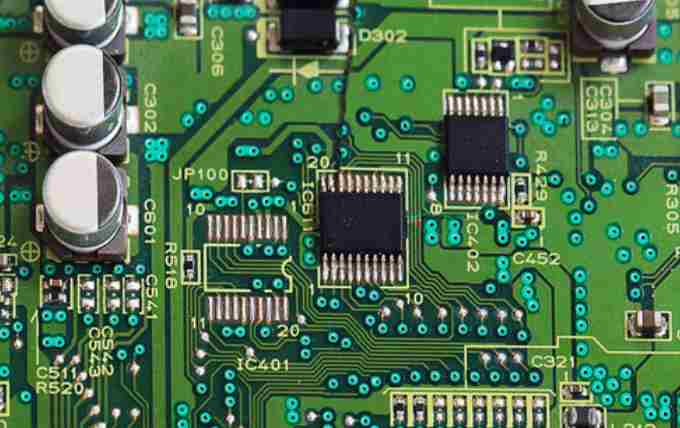
Today, with the increasing development of the electronic industry, with the trend of light, thin and short electronic products, the development of high-performance and multi-functional and the improvement of electronic device welding technology, soft circuit board (FPC) as the same circuit board used for electronic interconnection has been rapidly developed in China's printed board industry in the past two years, due to the demand for light, thin and short electronic products. The application range of flexible circuit boards is more and more wide, flexible printed boards and other types of printed boards, in a small space for a large number of wiring, need to bend repeatedly due to the selection of special materials, so compared with other cables have a longer bending life.
Due to the characteristics of thinness and lightness, the selection of machine equipment and processing methods during the surface treatment of the soft board has its special requirements. The production and surface cleaning treatment of the soft board is a key link, because it not only requires the surface to be in good condition, but also has strict requirements for the dimensional stability of the board. The dimensional stability depends on the dimensional change rate of the pressed copper foil layer. Also has a great impact on mechanical grinding in the production process, grinding brush roller running direction and the opposite direction of the board transfer, is to ensure the uniform grinding effect, but the soft plate substrate thin and soft, grinding pressure is too large the substrate will be stretched or torn, which is one of the important reasons for the size change, grinding process should avoid the substrate scratch, tear and plate. If the equipment is not specialized in the production conditions of soft board, it is recommended to use the pallet, which can avoid the deformation and even scrap of the substrate plate due to the large distance between the machine's transmission wheels, the influence of high pressure washing and drying hot air.
According to the requirements in the production process of soft board and the grinding brush wheel grinding comparison, the use of chemical cleaning method and nylon needle brush roller in the production process of soft printed board is the ideal choice of pattern transfer, hole metallization and coating film process surface treatment, which can not only remove the copper surface oxide layer but also achieve a good roughness of the board surface.
In the chemical plating and other surface processing process pre-treatment, can choose a low cutting force of non-woven brush roller, because of its uniform and fine grinding effect, can ensure the removal of the surface residual glue, the welding pad for fine and uniform grinding treatment, this is the nylon needle brush can not reach the surface treatment effect, because of its soft plate general pad small and less, ordinary nylon needle brush can not be fully ground to the pad, And grinding will leave a strip scratch, affecting welding and surface beauty. The choice of soft and cutting force is lower than the conventional non-woven brush roller can improve the effect that can not be achieved by nylon needle brush, non-woven brush roller because of its uniform and detailed grinding effect, is the first choice for many high-precision circuit board manufacturers, recommend the use of brush roller surface hardness of 30-45 degrees 1000# +1200# red non-woven brush roller. The wear mark is controlled at 8-10mm, which can ensure the dirt removal of the pad and the flatness of the surface coating.
The surface of the soft plate should be cleaned and ground before the hole metallization to improve the binding force between the hole metallization coating and the substrate. At the same time, the effective treatment of the copper surface before the formation of the image after the hole metallization is also very important to enhance the adhesion strength between the copper foil and the corrosion resistance layer. The surface of the FPC plate before the hole metallization is not clean. The porous metallized coating may appear delamination and foaming, the copper surface is not clean and coarser enough before image imaging, and the binding force with the corrosion resistance layer is not enough, and defects such as plating and short circuit are easy to appear in the subsequent plating process when making fine line graphics, resulting in scrap of the plate.
In the hole metallization and pattern transfer before the surface grinding coarsing method, it is recommended to use alumina containing abrasive 800#+1200# nylon needle brush roller, not only can effectively remove copper plating particles, and can be effective coarsing effect on the copper surface, wear marks control 8-12mm, can effectively prevent the plate from being stretched and other problems caused by excessive grinding. Alumina abrasive nylon wire in the treatment of copper surface, the cutting force is smaller than the traditional silicon carbide abrasive, can reduce the scratch of the board, the more dense the scratch, the better the adhesion of the board with the resist layer, in the back of the resist coating we recommend the use of wet film, in order to enhance the adhesion of the board with the resist layer.
Chemical cleaning method is to remove the organic debris and organic pollutants on the surface with chemical agents, and then coarsening the surface with micro-etching liquid. After treatment, the surface of the copper plate has good smoothness, and there is no mechanical scratch and residual abrasive particles, so it is an ideal clean coarsening surface treatment method in the processing of fine wire printed board. However, this method is not easy to completely smooth the copper particles and foreign bodies when cleaning the surface of copper foil, easy oxidation, roughness is not as good as mechanical grinding, and is suitable for the treatment process before the coating film.
Soft printed board as a domestic faster growth industry, many materials and equipment still need to continue to explore, mass production also need to process and machinery equipment, material field of continuous integrity, this paper extracted a link to the factors affecting the quality of the soft board to discuss, only master the essentials of each link, in order to produce higher performance more reliable, more beautiful appearance of the product, Continue to expand China's soft printed board industry.