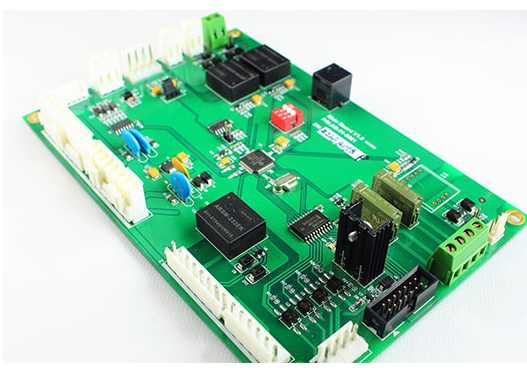
1. Pre-divide the digital, analog and DAA signal wiring area on the PCB board.
2. Digital and analog components and corresponding wiring should be separated and placed in their respective wiring areas as far as possible. 3. The high-speed digital signal route is as short as possible.
4. The route of sensitive analog signals should be as short as possible.
5. Allocate power and land properly.
6. DGND, AGND, and field separate.
7. Use wide wires for power supply and critical signal wiring.
8. Power cables and ground cables should be radial as far as possible, and signal cables should not be looped.
9. The digital circuit is placed near the parallel bus/serial DTE interface, and the DAA circuit is placed near the telephone line interface.
10. The wiring of small discrete devices should be symmetrical, and the leads of SMT pads with close spacing should be connected from the outside of the pads, and direct connection in the middle of the pads should not be allowed.
11. Key signal line priority: power supply, analog small signal, high-speed signal, clock signal and synchronization signal and other key signals priority.
12. The principle of wiring density priority: Start wiring from the most complex device connected on the board. Start with the most densely wired area of the board.
13 PCB design should avoid producing sharp angles and right angles, producing unnecessary radiation, and PCB production process performance is not good.
14. There can be no through hole on the patch pad to avoid the loss of solder paste resulting in virtual welding of components. Important signal cables are not allowed to pass between pins.
kinhford Electronics is a professional PCB design company engaged in electronic product circuit board design (layout layout design), mainly undertake multi-layer, high-density PCB design and circuit board design proofing business. With an average of more than 10 years of work experience in PCB design team, can skillfully use the market mainstream PCB design software, professional and efficient communication to ensure PCB design progress, to help you seize the market opportunity one step earlier!
1. Customer needs to provide data: schematic diagram (schdoc, DSN or sch) or netsheet, structure diagram (DXF), package library (need to provide a new package datasheet manual), design requirements.
2. Layout and wiring review: based on design specifications, design instructions, customer design requirements, and related CHECKLIST. After the project is started, our engineers will carry out schematic DRC check, structural check and other electrical design requirements. If there is any problem, feedback EQ record to the customer at the first time.
3. Customer layout confirmation: provide layout files and structure files for customers to conduct layout review; The customer confirms the layout rationality, the stacking scheme, the impedance scheme, the structure, the package, and the wiring parameters.
4. Design data output: PCB source files, Gerber files, assembly files, steel mesh files, structural files, etc. After the PCB Layout design is completed, our engineers will conduct mutual inspection, including DFM inspection, QA inspection, EMC inspection. After the customer confirms that it is OK, Gerber and other production documents will be issued.
The role of PCB design discharge teeth
During surge testing or ESD testing, high voltage will be generated at both ends of the common mode inductor, resulting in flarcs. If the distance between the two devices is too close, the surrounding devices may be damaged. Therefore, a discharge tube can be connected in parallel to suppress its voltage. Such as gas discharge tube, parallel at both ends of the common mode inductor, it can thus play the effect of extinguishing arc.
Gas discharge tube has good inhibition effect, but at a relatively high cost. In many cases, we will place discharge teeth at both ends of the common-mode inductor during PCB design, so that the common-mode inductor can discharge through the tip of the discharge teeth, which can reduce or even avoid discharge through other paths, and can protect the surrounding and post-stage devices. This discharge tooth is discharged through the air form, so the design should pay attention to the different sides of the common mode inductor, although it can play a certain effect, but for often with the surge current voltage, ESD in the occasion, if the use of this discharge tooth will be easy to produce carbon deposition, a long time will cause short circuit, it will go against the original design intention.
Maximum signal design rate: 10Gbps CML differential signal; Maximum PCB design layer: 40 layers;
Minimum line width: 2.4mil; Minimum line spacing: 2.4mil; Minimum BGA PIN spacing: 0.4mm; Minimum mechanical hole diameter: 6mil; Minimum laser drilling diameter: 4mil; Maximum number of pins:; 63000+ Maximum number of components: 3600; Maximum number of BGA: 48+.
kingford Electronics is a professional PCB design company engaged in electronic product circuit board design (layout layout design), mainly undertake multi-layer, high-density PCB design and circuit board design proofing business. With an average of more than 10 years of work experience in PCB design team, can skillfully use the market mainstream PCB design software, professional and efficient communication to ensure PCB design progress, to help you seize the market opportunity one step earlier!