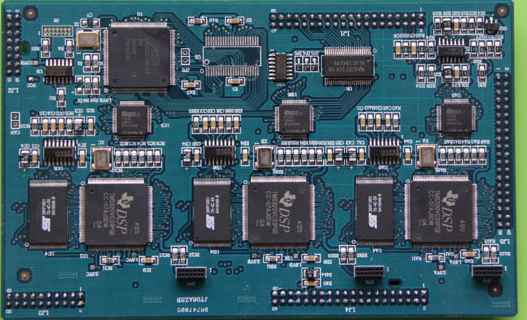
In order to complete the quality inspection, the quality objectives of SMT proofing processing with high qualification rate and high reliability need to control the design scheme, components, data, process, equipment, rules and regulations of the printed circuit board. The quality inspection of SMT patch proofing includes incoming inspection, process inspection and surface assembly board inspection. According to defect analysis, the quality inspection process of SMT patch proofing can reduce the defect rate and scrap rate, reduce rework maintenance costs, and avoid quality hazards from the source. Before entering the next process, SMT should follow reasonable detection methods to avoid various defects and hidden dangers.
1, SMT incoming material detection
The quality inspection of SMT patch proofing includes incoming inspection, process inspection and surface assembly board inspection. Quality problems found in process inspection can be corrected according to the rework situation. The rework cost of unqualified products found in incoming inspection, solder paste printing and pre-welding training is relatively low, which has little impact on the reliability of electronic products. But the rework of non-conforming products after welding is completely different. Since post-welding repairs require welding from scratch, in addition to working time and materials, components and circuit boards can also be damaged. According to defect analysis, the quality inspection process of SMT patch proofing can reduce the defect rate and scrap rate, reduce rework maintenance costs, and avoid quality hazards from the source.
2, SMT processing and testing
SMT patch proofing and welding inspection is a comprehensive inspection of welding products. Generally, the points that need to be detected are: to detect whether the spot welding surface is smooth, whether there are holes, holes, etc. Whether the spot welding is crescent shape, whether there is more tin and less tin, whether there are defects such as erected monuments, Bridges, parts moving, missing parts, tin beads, etc. Whether the parts have defects of different levels; Check whether there are defects such as short circuit and conduction during welding, and check the color change of the printed circuit board surface.
In the process of patch processing, in order to ensure the welding quality of printed circuit boards, we must always pay attention to whether the reflow process parameters are reasonable. If there is a problem with the parameter setting, the welding quality of the printed circuit board cannot be guaranteed. Therefore, under normal circumstances, the furnace temperature must be tested twice a day, and the low temperature test once. Only by continuously improving the temperature curve of welding products and setting the temperature curve of welding products can the quality of processed products be guaranteed.
The quality inspection of professional SMT patch proofing must be very strict, and only strict quality inspection can ensure the quality of SMT processed products. The Pearl River Delta. SMT factories are everywhere. It can even be said that nine out of ten industrial zones have electronic processing plants. If you want to survive and expand in this environment, ensuring product quality is a prerequisite.
1. Strength guarantee
▪SMT workshop: With imported SMT machines, optical inspection equipment, can produce 4 million points per day. Each process is equipped with QC personnel, who can keep an eye on product quality.
▪DIP production line: there are two wave soldering, of which there are more than 10 old employees who have worked for more than three years. The workers have high proficiency and can weld all kinds of plug-in materials.
2. Quality assurance, cost-effective
▪ High-end equipment can be attached to precision shaped parts, BGA, QFN, 0201 materials. Also can be template patch, loose material hand. ▪ Sample and size batch can be produced, proofing from 800 yuan, batch 0.008 yuan/point, no start-up fee.
3. Rich experience in SMT and welding of electronic products, stable delivery
▪ Accumulated service for thousands of electronic enterprises, involving many types of automotive equipment and industrial control motherboard SMT processing services, products are often exported to Europe and the United States, quality can be affirmed by new and old customers.
▪ Punctual delivery, normal 3-5 days after complete materials, small batches can also be expedited on the same day.
4. Strong maintenance ability, perfect after-sales service
▪ Experienced maintenance engineers can repair all kinds of patch welding caused by bad products, to ensure the connectivity of each circuit board.
▪ 24-hour customer service staff responds at any time to solve your order problems as quickly as possible.