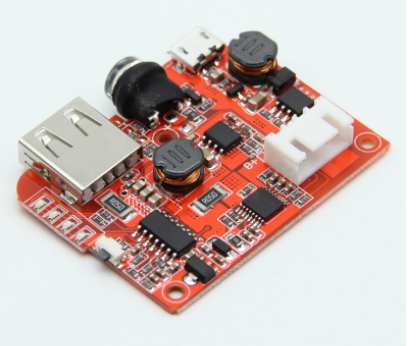
There is a bad processing phenomenon in the SMT OEM processing called welding pores, which is what we often say bubbles. Welding pores are SMT processing must be solved in the process of bad processing phenomenon, do not appear any bad phenomenon to give customers the best SMT patch processing service, the next SMT processing manufacturers electronic for you to share how to avoid patch welding pores.
1. Bake
Baking circuit boards and patch components exposed to air for a long time may affect the removal of water from the process.
2. Solder paste
If the solder paste contains moisture, it is also easy to produce undesirable phenomena such as pores and tin beads in the SMT patch processing process. For the solder paste, we need to choose high-quality solder paste, and then for the solder paste return temperature, stirring need to be strictly in accordance with the requirements of electronic processing production, the solder paste exposed to the air time as short as possible, after printing the solder paste, need to timely reflow welding.
3.Planned to monitor the humidity of the workshop, control between 40-60%.
4. Furnace temperature curve
The furnace temperature test is carried out twice a day to optimize the furnace temperature curve, and the heating rate cannot be too fast. The temperature of the preheating zone should meet the requirements, not too low, so that the flux can be fully volatilized, and the speed of the furnace can not be too fast.
5. Flux
In over-wave soldering, the amount of flux spraying can not be too much, and the spraying is reasonable. Electronic Co., Ltd. specializes in providing PCBA OEM services, including upstream electronic component procurement to PCB production and processing, SMT patches, DIP plug-ins, PCBA testing, finished product assembly and other one-stop services.
The company gives full play to its competitive advantages in scale procurement and quality control, and has signed long-term cooperation agreements with many electronic component manufacturers at home and abroad and around the world to ensure the quality and stable supply of raw materials, and transfer the benefits to customers.
Long-term maintenance of IC, resistors, capacitors, inductors, audiodes and other components procurement advantages, can greatly save customers' inventory costs, improve production turnover efficiency, save time. Currently for the United States, Britain, Japan, Russia, France, Canada, Australia, Romania, Switzerland and other countries and regions to provide PCBA processing services.