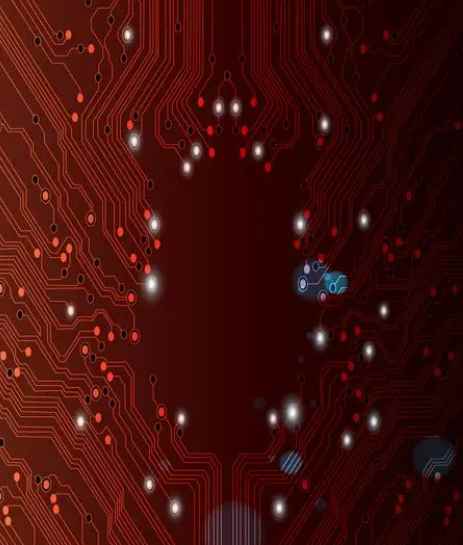
Printed circuit board (PCB circuit board), also known as printed circuit board, is a provider of electrical connections for electronic components. It has a history of more than 100 years; Its design is mainly layout design; The main advantage of using circuit boards is to greatly reduce wiring and assembly errors, improve the level of automation and production labor rate.
The following introduces the main functions of the PCB components:
The circuit board is mainly composed of welding pad, through hole, mounting hole, wire, components, connectors, filling, electrical boundary, etc. The main functions of each component are as follows:
Mounting hole: used to secure the circuit board.
Wire: Electrical network copper film used to connect component pins.
Pad: A metal hole for welding the pin of a component.
Through holes: There are metal through holes and non-metal through holes, where in the metal through holes are used to connect the component pins between the layers.
Connector: A component used to connect circuit boards.
Identify the factors and skills of PCB circuit boards
For PCB boards, its practicality is more important than its appearance. Specifically, there are two standards for good use and durability, one is that the symbol does not meet the relevant national standards, and the other is that the symbol does not meet the requirements of customers. If you want to process a telephone circuit board, then what are the factors and techniques to judge the quality of the Pcb circuit board?
1. The telephone should be easy to use after the components are installed, that is, the electrical connection should meet the requirements;
2. The line width, line thickness, line distance meet the requirements, so as to avoid heat, break, and short circuit of the line;
3. By high temperature copper skin is not easy to fall off;
4. The copper surface is not easy to oxidize, affecting the installation speed, and it will be broken soon after oxidation;
5. No additional electromagnetic radiation;
6. The shape is not deformed, so as to avoid deformation of the shell after installation and dislocation of the screw hole. Now are mechanized installation, the hole position of the circuit board and the deformation error of the line and design should be within the allowable range;
7. And high temperature, high humidity and special environment should also be considered in the range;
8. The mechanical properties of the surface should meet the installation requirements;
9. The appearance of the aesthetic problem.
The anode copper ball contains 0. 3-0. The main purpose of 6% phosphorus is to reduce the anode dissolution efficiency and reduce the production of copper powder;
When supplementing drugs, such as adding a larger amount such as copper sulfate, sulfuric acid; After addition, low current should be electrolyzed; When adding sulfuric acid, attention should be paid to safety, and when the amount of supplementation is large (more than 10 liters), it should be added slowly several times; Otherwise, the temperature of the tank will be too high, the decomposition of the light agent will be accelerated, and the tank will be polluted.
⑦ The addition of chloride ions should be paid special attention to, because the chloride ion content is particularly low (30-90ppm), it must be added with a measuring cylinder or measuring cup before weighing accurately; 1ml hydrochloric acid contains about 385ppm chloride ions,
⑧ Calculation formula for drug addition:
Copper sulfate (unit: kg)=(75-X) x tank volume (L)/1000
Sulfuric acid (unit: liter)=(10%-X)g/L× tank volume (liter)
Or (unit: liters)=(180-X)g/L x tank volume (liters)/1840
Hydrochloric acid (unit: ml)=(60-X)ppm x tank volume (L)/385
(3) Acid degreasing
① Purpose and function: Remove the oxide on the copper surface of the line, the ink residual film residual glue, and ensure the binding force between the copper and the copper or nickel electroplating of the graphic PCB.
② Remember to use acid degreasing agent here, why not use alkaline degreasing agent and alkaline degreasing agent degreasing effect is better than acid degreasing agent? Mainly because the graphic ink is not alkali resistant, it will damage the graphic circuit, so the graphic PCB can only use acid degreaser before electroplating.
③ Only need to control the concentration and time of oil remover during production, the concentration of oil remover is about 10%, the time is guaranteed to be 6 minutes, and a little longer will not have adverse effects; The use of tank fluid replacement is also in accordance with 15 square meters/liter of working fluid, and the addition is in accordance with 100 square meters. 5-0. 8L.