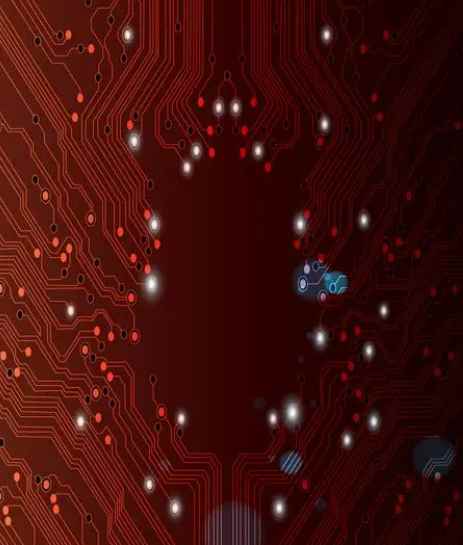
Printed PCB circuit boards, also known as printed circuit boards, are providers of electrical connections for electronic components. It has a history of more than 100 years; Its design is mainly layout design; The main advantage of using circuit boards is to greatly reduce wiring and assembly errors, improve the level of automation and production labor rate.
Wiring arrangement and reasonable layout of devices on PCB circuit board
(1) The printed circuit board is not allowed to have a cross circuit, for possible cross lines, you can use "drill", "wind" two ways to solve. That is, let a lead from other resistors, capacitors, the gap at the foot of the transistor "drill" in the past, or from one end of a lead that may cross "around" in the past, in special cases how the circuit is very complex, in order to simplify the design also allows the use of wire crossover, to solve the cross circuit problem.
(2) Resistors, diodes, tubular capacitors and other components have "vertical" and "horizontal" installation methods. Vertical refers to the component body perpendicular to the circuit board installation, welding, its advantage is to save space, horizontal refers to the component body parallel and close to the circuit board installation, welding, its advantage is that the mechanical strength of the component installation is better. These two different mounting components, the component hole spacing on the printed circuit board is not the same.
(3) The ground point of the same level circuit should be as close as possible, and the power filter capacitor of the circuit should also be connected to the ground point of the level. In particular, the ground point of the base and emitter of the transistor can not be too far away, otherwise the copper foil between the two ground points is too long, which will cause interference and self-excitation, and the circuit using such a "one-point grounding method" is more stable and not easy to self-excitation.
(4) The general ground line must be strictly in accordance with the high frequency - medium frequency - low frequency one level according to the order of weak current to strong current principle, must not arbitrarily turn over and over randomly, between the level can be wired long point, but also comply with this provision. In particular, the requirements of the ground wire arrangement of the frequency conversion head, the regeneration head, and the frequency modulation head are more stringent, and if there is improper, it will produce self-excitation so that it can not work. High-frequency circuits such as frequency modulation often use a large area enclosed ground wire to ensure a good shielding effect.
(5) The strong current lead (common ground wire, power amplifier power lead, etc.) should be as wide as possible to reduce the wiring resistance and its voltage drop, which can reduce the self-excitation caused by parasitic coupling.
Analysis of PCB board design process ten defects
1, the processing level is not clearly defined
The single panel design is on the TOP layer, if it is not specified, it may be made out of the board to install the device and not good welding.
2,Large area copper foil is too close to the outer frame
The spacing between large area copper foil and outer frame should be at least 0.2mm, because it is easy to cause the copper foil to warping and the solder resistance to fall off when milling the shape.
3, use the filler block to draw the pad
Drawing pad with filler blocks can pass DRC inspection when designing the circuit, but it is not good for machining, so the pad cannot directly generate solder resistance data. When applying solder resistance, the filler block area will be covered by solder resistance, resulting in difficulty in welding the device.
4, the electric formation is the welding pad and the connection
Because the design is a flower welding pad power supply, the formation is the opposite of the actual printed board image, all lines are isolation lines, drawing several groups of power supplies or several types of ground isolation lines should be careful, can not leave a gap, so that the two groups of power short circuit, can not cause the connection area blocked.
5, the character is misplaced
Character cover pad SMD weld, which brings inconvenience to PCB on-off test and component welding. The character design is too small, resulting in screen printing difficulties, too large so that the characters overlap each other, difficult to distinguish.
6, the surface mount device pad is too short
This is for the on-off test, for the too dense surface mount device, the distance between the two feet is quite small, the pad is also quite thin, the installation of the test needle must be staggered up and down, such as the pad design is too short, although it does not affect the installation of the device, but will make the test needle wrong.
7, single-side pad aperture setting
Single side pad is generally not drilled, if the drilling needs to be marked, its aperture should be designed to be zero. If you design the values so that when the drilling data is generated, the hole coordinates appear at this location, and there is a problem. Single side pad should be specially marked if drilled.
8, pad overlap
During the drilling process, the drill bit will be broken due to multiple holes in the same place, resulting in hole damage. The two holes in the multilayer plate overlap, and the film is drawn as an isolation plate, resulting in scrap.
9,There are too many filling blocks in the design or the filling blocks are filled with very thin lines
The light drawing data is lost, and the light drawing data is incomplete. Because the filling block is drawn line by line when the light drawing data is processed, the amount of light drawing data is quite large, which increases the difficulty of data processing.
10, graphics layer abuse
Some useless connections were made on some graphic layers, and more than five layers of lines were designed on the original four-layer board, causing misunderstanding. Against conventional design. The graphic layer should be kept complete and clear during design.