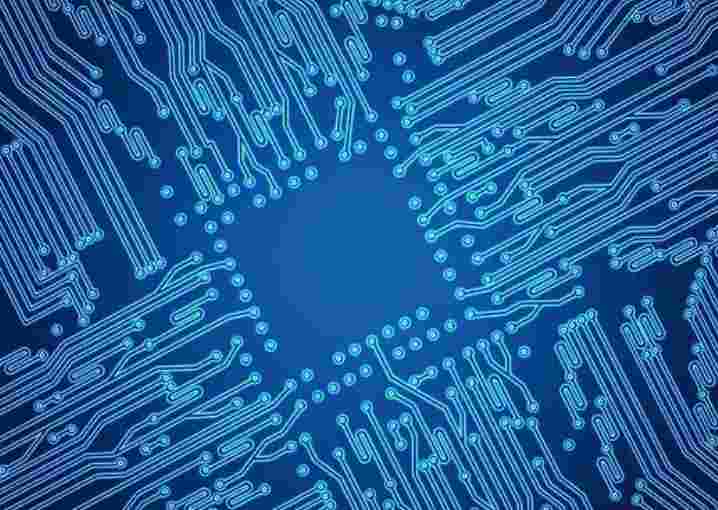
Driven by the trend of automotive lightweight, miniaturization, intelligence and electrification, automotive electronics will develop towards six functional trends in the future, namely: Mobile communications, multimedia entertainment, safe driving assistance (including autonomous driving), ride comfort and convenience, clean energy and power saving (including electric vehicles), protection and security, these are all challenges to the PCB industry, but also provide a good opportunity for development. For example, automatic driving will bring the large-scale application of millimeter wave radar, so the demand for high-frequency PCB circuit boards suitable for radar will be significantly increased, and the value is significantly higher than that of traditional PCB boards; The BMS in electric vehicles is one of the core components, and the PCB board is one of the basic components of BMS, which will also benefit from the development of electric vehicles.
The requirements for PCB in automotive electronics are diversified: high volume and low price products coexist with the demand for high reliability/safety. A large number of hard boards are used in the instrument panel, car audio, driving computer and other application environments. In the engine room, due to the heat dissipation requirements of the high temperature environment and LED light source, the heat dissipation substrate accounts for 3% of the proportion; In high frequency transmission and wireless radar detection, low temperature co-fired ceramics (LTCC) occupy 5% of the proportion. Products specially developed for automotive needs (such as IC carrier boards, soft boards, silver glue holes, etc.) account for about 17% of the overall proportion.
Driven by a large number of electronic cars, automotive PCB will also grow upward. The characteristics of stable orders and high gross profit margin of automotive PCB have attracted many PCB manufacturers to pay attention to the new blue ocean market. Because the car is used in a harsh environment at high speed, the automotive PCB is better than the ICT product specifications in terms of temperature resistance, electromagnetic wave resistance, earthquake resistance and corrosion resistance, so ensuring the quality of automotive parts and ensuring the life safety of drivers and passengers is the most important issue for all automakers. Component suppliers can provide long-term stable quality assurance is far more important than the price of cheap products, and vehicle manufacturers for the product verification period is often as long as three years, so for PCB manufacturers who want to enter the automotive electronics supply chain, they need to have enough patience and strength.
The Development Trend Of SMT Patch Processing In 2017
Industrial Revolution in Chip Processing This is an interesting time to change technology and industrial practices. For more than fifty years, welding has proven to be a reliable and efficient electronic joining process. But the challenge for people is to develop new materials that are comparable to the characteristics of solder, such as temperature and electrical properties and the strength of mechanical welding points; At the same time, it is necessary to pursue the elimination of undesirable factors, such as solvent cleaning and solvent gas efflux.
Over the past two decades, adhesive manufacturers have made progress in breaking down the welding barrier, which some SMT Processing Companies believes is worth considering in today's market.
Since IMC patch processing was once a "quasi compound" that could write the molecular formula, its properties are very different from the original metal, and it also has different degrees of influence on the overall solder joint strength. First of all, its characteristics are briefly described below: SMT patch red glue has viscosity and fluidity, temperature characteristics, wetting characteristics, etc. According to this characteristic of red glue, in the production, the purpose of using red glue is to make the parts firmly stick to the surface of the PCB to prevent it from falling.
Since the red glue of the patch processing is affected by the temperature with its own viscosity, fluidity, wetting and other characteristics, the SMT red glue must have certain conditions of use and standardized management. Red glue should have a specific flow number, according to the number of feed, date, type to number. Red glue should be stored in the refrigerator at 2-8 ° C to prevent the characteristics from being affected due to temperature changes.
Patch Processing Has Been Advancing To Miniaturization
SMT Machining Hybrid Microelectronics, fully sealed packages and Sensor technology: Epoxy resins are widely used in hybrid microelectronics and fully sealed packages, mainly because these systems have a box-shaped package that surrounds the electronic circuit. This package protects electronic circuits and prevents damage to components and bonding materials. Solder is also traditionally used in secondary connections, where damage due to handling is a problem, but because the entire electronic package is sealed, solder may not be necessary.
Since the birth of SMT processing, lead-tin combination has been the main method of connection in the electronics industry. Laws are now being implemented in Japan, Europe and North America to reduce the use of lead in manufacturing. This movement, along with the push towards greater miniaturization with increased functionality in the electronics and semiconductor industries, has led manufacturers to look for alternatives to traditional welding processes. Hybrid microelectronic packages are mostly used in military electronics, but are also widely used in the automotive industry for engine control and timing mechanisms (under the hood) and some for under-dash applications such as dual-gas control and airbag detonators. Sensor technology also uses conductive adhesives to seal pressure transducers, motion, light, sound and vibration sensors. Conductive adhesives have proven to be a reliable and effective method of joining in these applications.