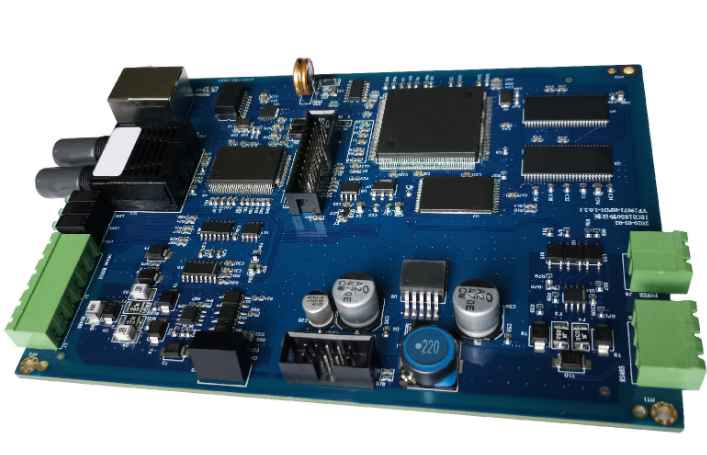
What Is PCBA Post Welding?
PCBA processing in many products in addition to the need for patch processing will also exist plug-in cases, plug-in is generally the use of wave soldering welding to improve welding efficiency to achieve mass production. However, in addition to wave soldering, there is another welding method that is post-welding processing, which requires the operator to directly use the electric soldering iron for welding processing. In the rapid development of the processing efficiency of SMT OEM, why do you need to use this inefficient processing method of post-welding? In fact, some components are not suitable for SMT proofing small batch processing, nor are they suitable for wave soldering, and can only be processed by manual welding.
First, the position of the component plug-in near the process edge will touch the assembly line and affect normal welding.
Second, special components for customers with special requirements of high sensitivity components, can not be over wave soldering.
Third, the height of the components is also limited, and the components are too high to lead to wave soldering.
Fourth, there are a small number of plug-ins on the side of the wave crest in a, there will be some plug-ins on the side of the wave crest welding, if it is a small number of plug-ins, you can use post-welding processing to improve efficiency.
Fifth, components are not resistant to high temperature, and now lead-free technology is becoming more and more popular. When soldering through the wave crest, the temperature in the furnace is higher than the temperature of the lead. Therefore, some components that are not resistant to high temperature cannot pass wave soldering.
Shenzhen Kingford Technology Co., Ltd. specializes in providing integrated PCBA electronic manufacturing services, including upstream electronic component procurement to PCB production and processing, SMT patches, DIP plug-ins, PCBA testing, finished product assembly and other one-stop services.
The company gives full play to its competitive advantages in scale procurement and quality control, and has signed long-term cooperation agreements with many electronic component manufacturers at home and abroad and around the world to ensure the quality and stable supply of raw materials, and transfer the benefits to customers.
Long-term maintenance of IC, resistors, capacitors, inductors, audiodes and other components procurement advantages, can greatly save customers' inventory costs, improve production turnover efficiency, save time. Currently for the United States, Britain, Japan, Russia, France, Canada, Australia, Romania, Switzerland and other countries and regions to provide PCBA processing services.
We provide PCBA processing services, starting from PCB circuit board production, our own PCB manufacturers (obtained the extremely strict automotive industry TS16949 certification), focusing on the quality of the circuit board and PCBA quality control system.
Due to decades of experience in purchasing electronic components, we maintain long-term cooperation with large brands to ensure the original packaging and procurement channels of components. In the packaging process of components, the selection of thousands and Locai solder paste to ensure the reliability of welding, with automatic printing press, Panasonic high-speed placement machine, upper and lower eight temperature zone reflow, AOI automatic optical detector, can effectively ensure the reliability and quality of electronic packaging process.
In addition, perfect IPC, IPQC, OQA and other management processes, clear job responsibilities, strict implementation of IPC electronic assembly acceptance standards. For PCBA testing, we have professional engineers to perform 100% batch testing using a variety of test stands, including channels, noise, amplitude, signal, temperature, humidity, drop or to perform customer-specific test plans. All efforts are aimed at becoming a refined PCBA processing factory.