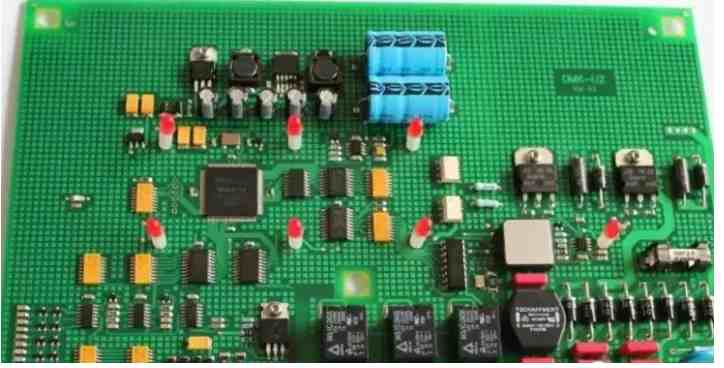
SMT proofing small batch processing cost is high where?
Electronic product research and development enterprises in the PCBA processing plant for SMT proofing small batch processing, often hear start-up costs and engineering costs. SMT patch processing requires fast and efficient production. Generally, the SMT workshop will carry out non-stop production. Downtime to replace machines will increase production costs and reduce profits. Therefore, small batch orders are often charged start-up fees.
First, SMT proofing smallbatch processing said that the high charge mainly refers to the loss of time, rather than the start of the loss. That is to say, before SMT chip processing, whether it is large-area SMT chip processing or small-scale SMT chip processing, the preliminary work that needs to be done is the same, such as SMT chip processing machine programming, PCB positioning, and the first piece confirmation after starting.
In fact, the time in the patch processing is very short. Therefore, when the amount is smaller, the so-called loss is more time lost. The cost of the project is the production of data documents, the production of steel mesh, the commissioning of equipment, the replacement of SMT lines, etc. Because the order is too small and does not meet the minimum consumption level, the customer needs to bear the cost of these works.
Second, under the same time cost, the production efficiency of mass SMT patch processing is higher, and there is no need to waste time on the preliminary work after a morning or a day of production. Sometimes customers take it for granted that a small quantity will make the price very cheap. In fact, this is not the case.
The early work of mass SMT processing and small batch processing is the same. The SMT placement machine programming, PCB positioning, and first piece confirmation after starting are all the same, as long as the placement machine is properly debutted. Therefore, small batch processing will charge engineering fees, or some places called start-up fees. Otherwise, the quantity is too small, not enough labor costs and machine losses, and the time in and out is basically wasted. This is the reason why SMT proofing small batch processing costs are high.
Strength Guarantee
▪SMT workshop: With imported SMT machines, optical inspection equipment, can produce 4 million points per day. Each process is equipped with QC personnel, who can keep an eye on product quality.
▪DIP production line: there are two wave soldering, of which there are more than 10 old employees who have worked for more than three years. The workers have high proficiency and can weld all kinds of plug-in materials.
Quality Assurance, Cost-effective
▪ High-end equipment can be attached to precision special-shaped parts, BGA, QFN, 0201 materials. Also can be template patch, loose material hand.
▪ Sample and size batch can be produced, proofing from 800 yuan, batch 0.008 yuan/point, no start-up fee.
Rich Experience In SMT And Welding Of Electronic Products, Stable Delivery.
▪ Accumulated services for thousands of electronic enterprises, involving many types of automotive equipment and industrial control motherboard SMT processing services, products are often exported to Europe and the United States, quality can be affirmed by new and old customers.
▪ Punctual delivery, normal 3-5 days after complete materials, small batches can also be expedited on the same day.
Strong Maintenance Ability, Perfect After-sales Service.
▪ Experienced maintenance engineers can repair all kinds of patch welding caused by bad products, to ensure the connectivity of each circuit board.
▪ 24-hour customer service staff responds at any time to solve your order problems as quickly as possible.
Replaceable and adjustable components, if you encounter components and parts that need to be frequently replaced or adjusted, you need to consider the characteristics and requirements of the entire machine, and place it in a position that is easy to replace.
Temperature-sensitive components in the mounting process, if you encounter temperature-sensitive components, be sure to stay away from heating components, such as transistors, integrated circuits, electrolytic capacitors, etc., to stay away from high-power components, radiators and high-power resistors.
The arrangement direction, in the actual processing of the SMT patch, the arrangement direction of the patch components is also required, as far as possible to maintain the same direction, the characteristic direction should be consistent, so as to facilitate the subsequent installation, welding and testing, especially the printing direction of the component number must be the same.
The distribution is balanced, the high quality of the patch components in the process of reflow processing heat capacity will be larger than the general components, which will lead to local temperature difference and even welding problems, maintain the distribution balance in the SMT patch processing can avoid such problems, but also to maintain the balance of the circuit board.
Heating components, different components contact together, will have an impact on other components, such as heating components, this is generally placed on the corner, ventilation position, conducive to heat dissipation. The heating element must be supported by other leads or supports, but also maintain a certain distance from the printed circuit board surface, the minimum can not be less than 2mm, otherwise it will affect the quality of the circuit board.