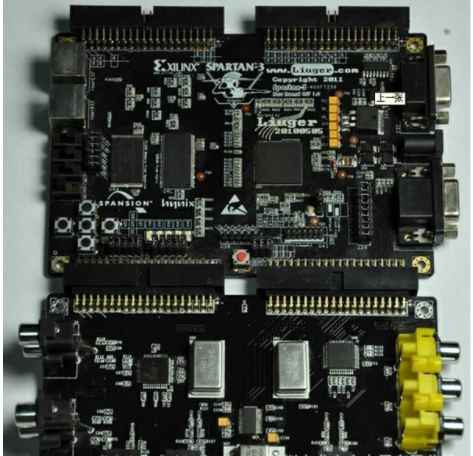
There are many SMT processing modes, such as SMT patches and OEM processing, different processing cooperation modes of the process is different, the corresponding customer needs to prepare things are not the same. The biggest difference between OEM and SMT patches is that OEM requires customers to prepare their own materials, and OEM can give the board, component procurement and other links to PCBA processing plants to do. Quality is always the most important measure for all electronics processing plants, and the same is true for incoming processing. kingford uses the most professional processing equipment, plant and production process control to ensure product quality.
The two parties will discuss the SMT processing project in detail, and sign the cooperation contract after confirmation. The customer needs to provide PCB file, Bom list and component materials. The PCB file and Bom list are used to confirm the component mounting direction and material accuracy.
Incoming material inspection and processing. IQC inspection of materials to ensure production quality, for some components need to carry out material processing, such as material cutting feet, component molding and so on.
On-line production. The first sample will be made before production, and mass production will be carried out after confirmation by both parties. During the process, we will carry out steel mesh production, solder paste printing, component mounting, reflux process and red glue process.
Finished product inspection. The products shall be checked by the quality department, and packaged and delivered to the warehouse after the power is qualified.
kingford Electronics Co., Ltd. specializes in providing integrated PCBA electronic manufacturing services, including upstream electronic component procurement to PCB production and processing, SMT patches, DIP plug-ins, PCBA testing, finished product assembly and other one-stop services.
The company gives full play to its competitive advantages in scale procurement and quality control, and has signed long-term cooperation agreements with many electronic component manufacturers at home and abroad and around the world to ensure the quality and stable supply of raw materials, and transfer the benefits to customers.
Long-term maintenance of IC, resistors, capacitors, inductors, audiodes and other components procurement advantages, can greatly save customers' inventory costs, improve production turnover efficiency, save time. Currently for the United States, Britain, Japan, Russia, France, Canada, Australia, Romania, Switzerland and other countries and regions to provide PCBA processing services.
Why Should SMT processing Do Electrostatic Protection?
There are precision electronic components on the PCBA board, and many components are more sensitive to voltage. A shock above the rated voltage will damage these components.
The SMT patches damaged by static electricity is difficult to gradually investigate during functional testing. What is more fatal is that some PCBA boards function normally during testing, but when the finished products are used in the hands of customers, there are occasional defects, which brings great hidden dangers to the after-sales service and affects the company's brand and reputation. Therefore, in the SMT processing process, we must attach great importance to ESD electrostatic protection.
SMT processing how to do electrostatic protection measures
The operator must wear electrostatic work clothes, it is forbidden to attach or wear any metal products on the work clothes, and it is not allowed to take off the work clothes on the site of the operation of electrostatic sensitive products. The buttons of the work clothes must be all buttoned up, and it should not be in a state of undressing as far as possible.
Wear an ESD wrist strap that is in good contact with your skin and grounded reliably. Do not store electrostatic objects such as plastic boxes, erasers, cardboard, and glass on the ESD safety workbench.
The operation of all components must be carried out on the electrostatic safety workbench. Components entering the ESD work area must be treated according to the ESD requirements.
The electrostatic sensitive components that fall on the floor during the operation must be tested and reconfirmed before they can be used. Items that cannot be directly tested must be confirmed before they can be released.
When holding the sensitive element, avoid touching its lead and connector. Avoid the area of electrostatic sensitive components when holding the mainboard. When some components are to be cleaned, anti-static brushes should be used, and plastic brushes should not be used.