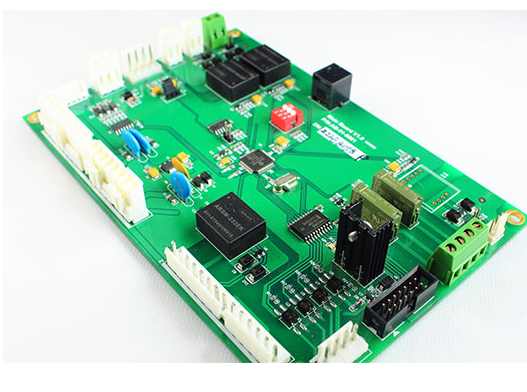
When we do the PCB design, we attach great importance to the direction and corresponding order of the bit number, and worry about the reverse direction of the bit number screen printing or the incorrect placement of the screen printing, which will affect the placement error.
It can be clearly said that the screen printing position number does not determine whether the final patch is correct. Many experienced engineers found that many experienced engineers found that deleting the bit number screen printing, PCBA patch product patch back and there is no problem. In general, the machine patch first finds the device, and then places the found device in the correct position on the PCB,
which involves simple programming, including two points:
1.The pick-up program is to tell the machine where to pick up, what components to pick up, what packaging components and other pick-up information. The content includes: the name of the component of each step, the offset of X, y, and Angle t of each step, the type of feeder, the pick height, the throwing position, and whether to skip.
2. The patch program is to tell the machine where to paste the components, the Angle of the patch, the height of the patch and other information. Its content includes: the component name and description of each step, the X, y coordinates and Angle t of each step, whether the height of the patch needs to be corrected, the number of patch heads, whether the patch time is at the same time, whether the step is skipped, and so on. The patch also includes the PCB's X and Y coordinate information and local markings.
This shows that the machine patch will not find the silk screen bit number on your PCB at all, but work according to the programming program, and the most important file for programming is the accurate coordinate file, so we can understand why you do not need the bit number map, but must need the coordinate file.
Shenzhen Kingford Technology Co.,Ltd. specializes in providing complete PCBA electronic manufacturing services, including PCB design, upstream electronic component procurement to PCB production and processing, PCBA patch, DIP plug-ins, PCBA testing, finished product assembly and other one-stop services. The company gives full play to its competitive advantages in scale procurement and quality control, and has signed long-term cooperation agreements with many electronic component manufacturers at home and abroad and around the world to ensure the quality and stable supply of raw materials, and transfer the benefits to customers.
Long-term maintenance of IC, resistors, capacitors, inductors, audiodes and other components procurement advantages, can greatly save customers' inventory costs, improve production turnover efficiency, save time. Currently for the United States, Britain, Japan, Russia, France, Canada, Australia, Romania, Switzerland and other countries and regions to provide PCBA processing services.
We provide PCBA processing services, starting from PCB circuit board production, our own PCB manufacturers (obtained the extremely strict automotive industry TS16949 certification), focusing on the quality of the circuit board and PCBA quality control system.
Due to decades of experience in purchasing electronic components, we maintain long-term cooperation with large brands to ensure the original packaging and procurement channels of components. In the packaging process of components, the selection of thousands and Locai solder paste to ensure the reliability of welding, with automatic printing press, Panasonic high-speed placement machine, upper and lower eight temperature zone reflow, AOI automatic optical detector, can effectively ensure the reliability and quality of electronic packaging process.
In addition, perfect IPC, IPQC, OQA and other management processes, clear job responsibilities, strict implementation of IPC electronic assembly acceptance standards. For PCBA testing, we have professional engineers to perform 100% batch testing using a variety of test stands, including channels, noise, amplitude, signal, temperature, humidity, drop or to perform customer-specific test plans. All efforts are aimed at becoming a refined PCBA processing factory.