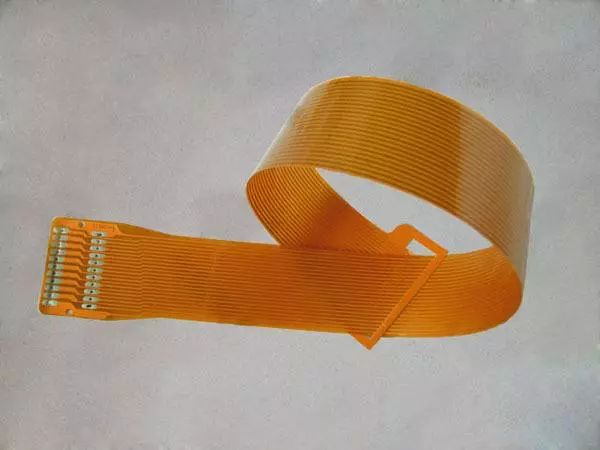
Since the FPC flexible board can be bent, folded or repeatedly moved in various ways, compared with ordinary rigid boards (pcb), it has the advantages of lightness, thinness and flexibility, so its application is more and more extensive. The characteristics depend on the performance of the substrate material, so to improve the technical performance of the FPC flexible circuit board, we must first improve the performance of the substrate. So how about the development of FPC soft board materials, let's talk about it in detail.
The development of FPC soft board materials
1. Performance comparison of commonly used film substrates
The function of the film substrate is to provide the carrier of the conductor and the insulating medium between the lines, and at the same time, it can be bent and curled. FPC soft board substrates are commonly used PI polyimide film and PET polyester film. Flexible copper clad laminates and rigid copper clad laminates also have halogen-free environmental protection requirements, and green and environmentally friendly materials are an inevitable trend.
Polyester (PET) resin has good mechanical and electrical properties, but the biggest disadvantage is poor heat resistance, which is not suitable for direct welding and assembly. The adhesive is to combine the copper foil with the base film, and commonly used are PI resin, PET resin, modified epoxy resin, and acrylic resin.
Introduction to the development of FPC soft board materials
2. PI substrate with two-layer structure
Flexible copper clad laminates (FCCL) usually have a three-layer structure, namely polyimide, adhesive and copper foil. Since adhesives can affect the properties of flexible boards, especially electrical properties and dimensional stability, adhesive-free two-layer flexible copper clad laminates have been developed. At present, there are many methods of depositing electroplated metal layers on polyimide films, and flexible PCB with high performance requirements tend to use two-layer copper clad laminates.
3. LCP substrate
Liquid crystal polymer (LCP) copper clad laminate is made of thermoplastic liquid crystal polymer film and covered with copper foil by continuous hot pressing to obtain single-sided or double-sided copper clad laminate. The water absorption rate is only 0.04%, and the dielectric constant is 2.85 at 1GHz. requirements. The polymer is in a liquid crystal state, and the one that melts when heated is called "TLCP hot-melt liquid crystal polymer".
The advantages of TLCP can be injection molding, extrusion processing into a film to become the substrate of PCB and FPC, and secondary processing for recycling. The low hygroscopicity, high frequency suitability, and thermal dimensional stability of TLCP films make TLCP films applied on FPC-COF multilayer substrates.
4. Halogen-free flexible substrates that meet environmental requirements
Halogen-free (bromine) substrates have been developed and applied in rigid boards and flexible PCB. For flexible substrates, including FCCL, cover films, adhesive sheets, and solder resists, as well as reinforcing boards, they must be flame-retardant and halogen-free.
5. New copper foil
The conductive material of FPC soft board is mainly copper-copper foil, and some alloys such as aluminum, nickel, gold, and silver are also used. The basic requirements of the conductor layer are not only electrical conductivity, but also bending resistance. There are two types of copper foils: electrolytic copper foil and rolled copper foil.
The difference between RA and ED copper foil is that the crystal shape is different, RA copper foil is columnar arrangement, the structure is uniform, flat, and easy to roughen or etch; ED copper foil is a fish-scale sheet-like stack, and the rolled copper foil is smooth and tough. Good, while roughening or etching process becomes difficult.
6. Conductive silver paste
In the manufacture of flexible PCBs, conductive inks are used to print wires or shielding layers on the insulating film. Most of these conductive inks are silver paste conductive pastes. The conductive layers formed by printing are required to have low resistance, strong bonding, and flexibility. Easy to cure. The use of conductive inks to create graphics is also an environmentally friendly, low-cost technology.