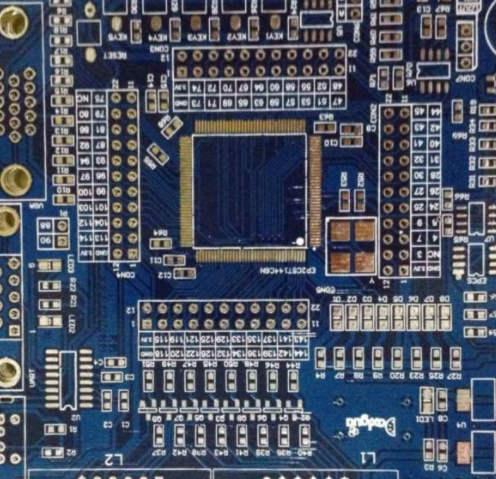
X-ray Automatic Inspection Technology in PCB Assembly
In short, the so-called automatic X-ray inspection or AXI technology uses X-ray to check the characteristics of target objects As an application program, it has a place in many industries, including but not limited to aerospace, medical, PCB assembly, etc
As a traditional testing equipment, X-ray still has a long way to go in testing the quality of printed circuit boards, especially in the case of increasing miniaturization, they have their own limitations. In addition, there are hidden solder joints in some cases. However, X-rays can also penetrate and check the quality of hidden solder joints. This, although automatic optical inspection is only applicable to defects that are relatively easy to find, such as open circuit or welding bridge, if light cannot be inspected separately, automatic X-ray inspection is required.
What PCB components are the reasons for choosing automatic X-ray testing technology
The advantage of X-ray is that the X-ray absorbed by data is proportional to its atomic weight and depends on its density and thickness. In this case, heavier elements absorb more X-ray than lighter elements. It is easy to catch hidden defects, such as lack of power components, short circuit, etc.
An ideal X-ray system must have a clear image so that the information about defect analysis is clear and feasible. In this case, it is ideal that the X-ray inspection system has sufficient magnification and inclination inspection functions. The latter ensures that the solder ball is not only inspected from above.
Circuit board
X-ray inspection equipment usually has two forms: two-dimensional and three-dimensional. Both can be operated offline, making the inspection process simple. However, some devices can be used online. The selection of offline and online devices usually depends on the amount of checks required. When a large number of inspections are required and the inspection level is complex, online equipment is usually used. Although two-dimensional systems can display two-dimensional images of components on both sides, three-dimensional systems can generate cross-sectional images. The 3D system can also combine cross section images through a method called tomography.
The required resolution type also needs to select the appropriate X-ray tube. There are usually two types of opening and closing. The required magnification also determines the distance between the sample and the X-ray tube. X-ray voltage is another determinant of its penetration ability. With high voltage, objects with high density and thickness can be easily checked. However, for a single panel, low voltage is sufficient. Similarly, multilayer boards require high pressure.
The early detection equipment is equipped with an image intensifier connected to the CCD camera, but the image intensifier has the following limitations:
Limited coverage, in turn, means that multiple technologies may be required to inspect the area. This in turn adds time for satisfaction checks. Within a limited field of view at a given point in time, an area 3 to 5 inches in diameter can be examined. Since the ionizing radiation passing through the casting edge is not attenuated, image overflow may occur at the image edge. The noise level adds an image intensifier to generate noise images. A clean, noise free image requires digital processing of the image, which in turn is time-consuming and cannot keep the process real-time.
However, the above limitations can be mitigated by the following pipelines. Use direct digital imaging equipment. It not only provides a larger detection area, but also improves the resolution.
With X-ray inspection, we can perform the following operations:
Carry out nondestructive testing, detect short circuit, detect faulty soldering, determine component displacement, check electrocrystal, check switch, relay, plug and cable connection
In short, the advantages of automatic X-ray detection technology are as follows:
Reliable and consistent results reduce inspection time and labor costs Effective process control, because defective PCB components can be found at an early stage, and other defective PCB components can be prevented