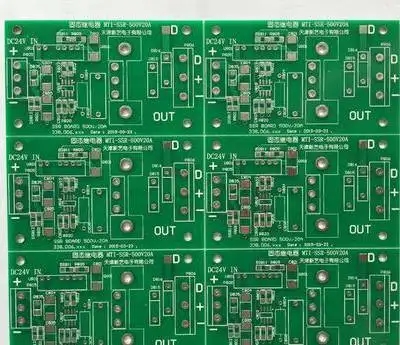
What is the reason for PCBA processing faulty soldering
What is the reason for PCBA processing faulty soldering? What's the solution
1、 What is faulty soldering?
There is an isolation layer between the soldering tin and the pin, that is, there is poor contact between the component and the bonding pad. They are not completely in contact with each other. It is generally invisible to the naked eye However, its electrical characteristics have no conduction or poor conduction, which affects the circuit characteristics.
2、 What is false welding?
False soldering is similar to false soldering, which is the phenomenon that the circuit works normally in the initial stage and gradually opens in the later stage.
3、 What is the cause of false welding?
1. Oxidation of bonding pads and component pins
It is easy to lead to insufficient wetting of solder pad and tin crawling when solder paste is liquefied during reflow soldering, resulting in faulty soldering
2. Little tin
In the solder paste printing link, due to the small opening of the steel mesh or the small pressure of the scraper, there is less tin, so that the solder paste is not enough to fully weld the components during welding
3. Temperature too high or too low
If the temperature is too high, not only the solder will flow, but also the surface oxidation speed will be accelerated, and false soldering may also occur.
4. Solder paste melting point is low
Low temperature solder paste has a relatively low melting point, while the component pin and the plate material of the fixed component are different, and their thermal expansion coefficients are different. With the change of the component working temperature, under the force of thermal expansion and cold contraction, the phenomenon of faulty soldering will occur.
5. Solder paste quality problems
Poor solder paste quality, easy oxidation of solder paste and loss of flux will directly affect the solder paste's welding performance, leading to faulty soldering/false soldering
4、 Solution to false welding
1. Moisture proof storage of components:
If the components are placed in the air for a long time, they will absorb moisture and oxidize, which will lead to the failure of the components to fully remove the oxides during welding, and thus lead to defects such as false soldering and false soldering. Therefore, PCBA processing plants will be equipped with ovens, which can be used to bake the components with water during welding and replace the oxidized components.
2. Solder pastes of famous brands are selected:
The defects of false soldering and false soldering during PCBA welding are closely related to the quality of solder paste.
3. Adjust printing parameters:
The problem of faulty soldering and false soldering is mostly due to the lack of tin. During the printing process, the pressure of the scraper should be adjusted, and the appropriate steel mesh should be selected. The opening of the steel mesh should not be too small to avoid too little tin.
4. Adjust reflow temperature curve:
During the reflow welding process, the welding time shall be controlled. If the time in the preheating area is not enough, the flux cannot be fully activated, and the surface oxide at the welding point can be removed. If the time in the welding area is too long or too short, false welding and false welding will be caused.
5. Select appropriate testing equipment:
AOI testing equipment or X-ray testing equipment shall be selected. When X-ray testing equipment can detect faulty solder joints, holes in circuit boards, and broken parts of circuit boards by detecting the difference of ray intensity of penetrating objects, the welding quality shall be detected, and the outflow of defective products of faulty solder joints and false solder joints shall be reduced.
5、 Hazards of false welding
False welding and false welding reduce the reliability of products, cause unnecessary maintenance in the production process, increase production costs, reduce production efficiency, cause great quality and safety hazards to products that have already left the factory, increase after-sales maintenance costs, increase customer distrust, reduce orders, and affect the company's image.
False soldering sometimes occurs during PCBA processing. Weak soldering, also known as cold soldering, refers to an unstable state in which components appear to be welded, but are not actually connected internally, or are not connected in time. It will not only affect the circuit characteristics, but also cause the PCB board to be unqualified or even scrapped.
False soldering sometimes occurs during PCBA processing. Weak soldering, also known as cold soldering, refers to an unstable state in which components appear to be welded, but are not actually connected internally, or are not connected in time. It will not only affect the circuit characteristics, but also cause the PCB board to be unqualified or even scrapped. The following describes the causes and solutions of PCBA processing false soldering
What is the reason for PCBA processing faulty soldering? What's the solution
1、 PCBA faulty soldering is a common circuit fault. The common causes of faulty soldering are as follows:
1. In the production process, due to improper production process, such as poor welding or lack of tin resulting in no continuity of the element pin and the welding pad, the circuit board is in an unstable state that the circuit board is not connected at the same time;
2. Due to the long-term use of electrical appliances, the solder joints at the weld legs of some parts with severe heat are prone to aging and peeling or impurities.
2、 Solution to PCBA faulty soldering:
1. Components must be stored in a moisture-proof way, such as a moisture-proof cabinet;
2. Slightly polish the straight plug before welding;
3. Solder paste and flux can be used for welding, and reflow soldering machine is preferred. Good technology is required for manual welding;
4. Properly select a good PCB substrate material.
In the process of PCBA processing, faulty soldering is an important reason that affects the quality of circuit boards. Once it occurs, it needs to be reworked. It not only increases labor pressure, but also reduces production efficiency and causes losses to the enterprise. Therefore, it is necessary to avoid the occurrence of faulty soldering as much as possible and do a good job of inspection. Once it occurs, it is necessary to find out the cause and solve it immediately.