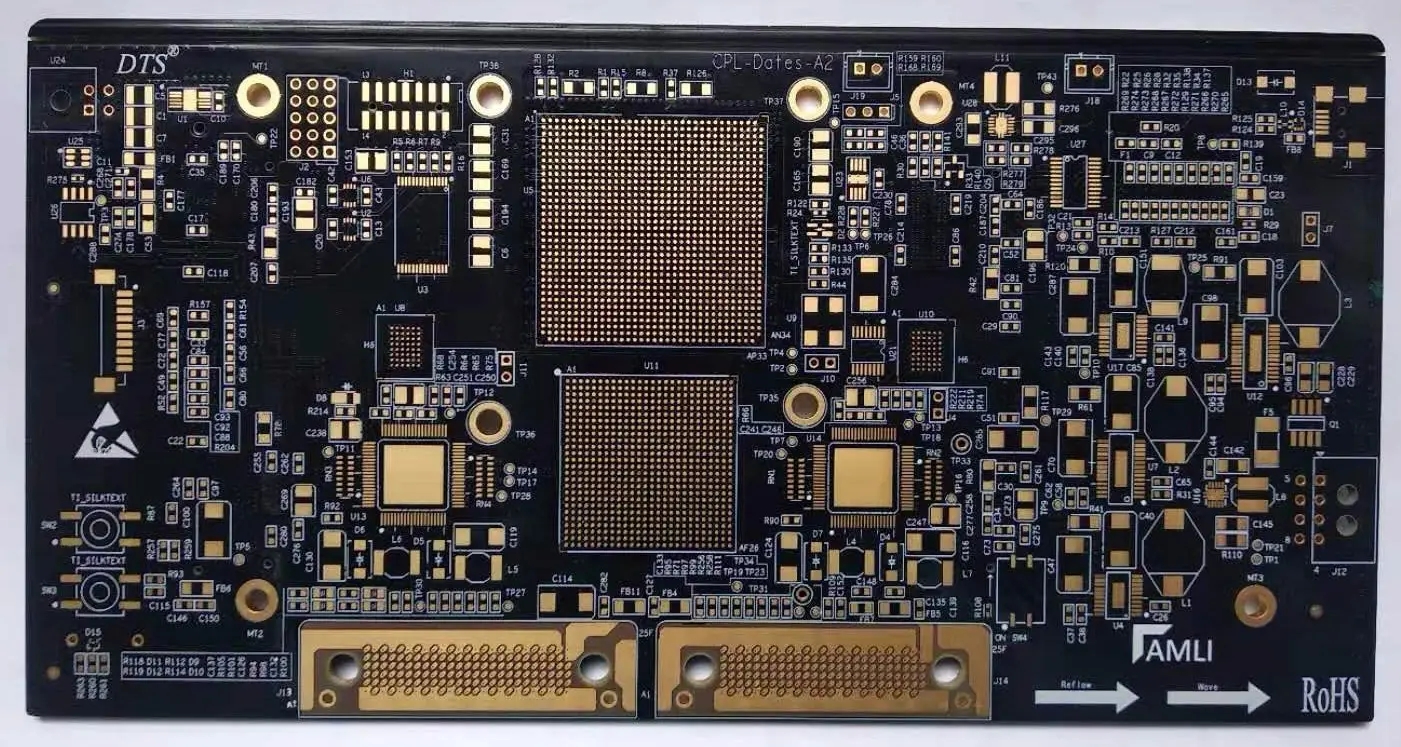
SMT lead-free process requirements and solutions
1、 Solder paste screen printing process requirements
1. Thawing and stirring: firstly, take solder paste out of the cold storage to thaw for at least 4 hours, and then stir it. The stirring time is mechanical for 2 minutes and manual for 3 minutes. The purpose of stirring is to physically separate solder paste stored in the warehouse or restore it due to high metal content due to use and recycling. At present, lead-free solder paste Sn/Ag3.0/Cu0.5 replaces alloy, with a specific gravity of 7.3, The specific gravity of Sn63/Pb37 alloy is 8.5, so the mixing and separation time of lead-free solder paste can be shorter than that of lead containing solder paste.
2. Formwork: stainless steel laser opening, 80-150 meshes (0.1-0.25mm) thick, copper and electroformed Ni die analysis can be used.
3. Scraper: hard rubber (polyurethane scraper) and stainless steel metal scraper.
4. Scraper speed angle: 2cm-12cm per second. (Determined according to the size and density of PCB components); Angle: 35-65 ℃.
5. Scraper pressure: 1.0-2Kg/cm2.
6. Reflux mode: applicable to various reflux devices such as compressed air, infrared ray and gas-phase reflux.
7. Process requirements: The solder paste screen printing process includes four main processes, namely alignment, filling, leveling and release. To do the whole work well, there are certain requirements on the base plate. The base plate shall be flat enough, and the dimensions between bonding pads shall be accurate and stable. The design of bonding pads shall coordinate with the screen printing steel mesh, and have a good reference point design to assist in automatic positioning and alignment. In addition, the label oil print on the base plate shall not affect the screen printing part. The design of the base plate must facilitate the automatic up and down of the screen printing machine. The appearance and thickness shall not affect the flatness required for screen printing.
8. Reflow welding process: Reflow welding process is the most commonly used welding technology at present. The key of the reflow welding process is to adjust the set temperature curve. The temperature curve must meet the requirements of solder paste products from different manufacturers.
2、 Reflow soldering temperature curve
The lead-free reflow soldering optimization process curve recommended in this paper describes four important points on the recommended process curve:
1. The heating speed in the preheating area should be as slow as possible (2-3 ℃/s), so as to control the solder bridge and solder ball caused by the collapse of solder paste.
2. The active area must be within the range of (45-90sec, 120-160 ℃), so as to control the temperature difference of PCB substrate and the change of flux performance and other factors, which may lead to poor reflow soldering.
3. The maximum temperature of welding shall be kept above 230 ℃ for 20-30 seconds to ensure the wettability of welding.
4. The cooling rate shall be - 4 ℃/s.
Description of humidity change of reflux curve:
1. The flux of the solder paste starts to melt when the humidity rises to 100 ℃ (it starts to enter the active period). The main role of the solder paste in the active area is to remove the oxide layer on the surface of the solder object. If the active area lasts too long, the flux will evaporate too quickly, which will also cause the solder joint surface to be not smooth and grainy. It takes about 30-45 seconds for the solder paste to completely melt above the melting point humidity (into the reflow zone). Whether to extend the time depends on the PCB thickness, component size and density.
2. The temperature of the active area can also help the components of the PCB absorb slowly, reducing the temperature difference between the large and small components, and reducing the occurrence of functional failures.
3. The temperature difference between the large and small components entering the reflux furnace is about 11.4 ℃, so we should reduce their difference from the active area to control, and the maximum temperature difference can be reduced to 5-8 ℃.
4. Considering that lead-free solder paste is composed of multiple alloys and the cooling shrinkage time of metal is different, in order to make solder joints bright, except for other methods, rapid cooling is the most effective method.
3、 Defects in Reflow Soldering and Solutions
1. The welding defects are divided into main defects, secondary defects and surface defects: a. The main defects cause the SMA function failure of the product. b. Minor defects refer to good wetting between solder joints, normal SMA function, but will affect the life of the product. c. Surface defects do not affect the life and function of the product (usually identified by production process, appearance).
2. Problem formation and handling plan:
A. Tin bead
Cause: During the assembly of components, the solder paste is placed between the pin and the pad of the chip component. If the pad and the component pin are not well wetted (poor solderability), the liquid solder will shrink and make the weld insufficient, and all solder particles cannot be aggregated into a solder joint. Some liquid solder will flow out of the weld to form solder beads. b. When the pressure of Z-axis is too high, the solder paste is squeezed out of the pad. c. If the heating speed is too fast and the time is too short, the moisture and solvent in the solder paste can not be completely volatilized. When it reaches the reflow soldering area, the solvent and moisture will boil and the solder bead will be splashed. d. The opening size and contour of the formwork are not clear.
Solution: a. Follow up whether bonding pads, component pins and solder pastes are oxidized. B. Adjust the template opening to accurately align with the pad. C. Accurately adjust the Z-axis pressure. d. Adjust the temperature rise rate of the activation zone in the preheating zone. e. Check whether the opening and contour of the formwork are clear, and replace the formwork if necessary.
B. Erect a monument
(Manhattan phenomenon)
One end of the component is welded to the other end of the pad, and then it is warped.
Causes: a. Uneven heating at both ends of the component or excessive width, length and gap at both ends of the pad, resulting in the solder paste melting successively. b. The placement element is displaced. c. The flux in the solder paste floats the component. d. Poor solderability of components. E. The printing solder paste is not thick enough.
Solution: a. The components shall be uniform and reasonably designed, and the dimensions at both ends of the pad shall be symmetrical. b. Adjust printing parameters and placement position. c. Use a moderate flux (10.5 ± 0.5% for lead-free solder paste flux). d. Lead free solder paste or solder paste containing silver and bismuth shall be used as non material. e. Increase the printing thickness.
C. Bridging
(The unconnected solder joints are connected together), one of the most common defects in SMT production, which will cause short circuit between components.
Reasons: a. Solder paste quality problems, high metal content in solder paste and long printing time. b. Too much solder paste, low viscosity, and poor slump. After preheating, it flows out of the pad and leads to the bridging of solder joints with dense gaps. c. The printing alignment is not correct or the printing pressure is too large, which is easy to cause fine pitch QFP bridging. D. The solder paste overflows when the pressure of components is too high. E. The chain speed and heating speed are too fast, and the solvent in the solder paste cannot volatilize in time.
Solution: a Replace or add new solder paste (new solder paste can be added regularly during printing to maintain its metal content and viscosity). b. Reduce the scraper pressure and use solder paste with viscosity of 190 ± 30Pa · S. c. Adjust the template for accurate alignment. d. Adjust the Z-axis pressure. e. Adjust the reflux temperature curve, and adjust the chain speed and furnace temperature according to the actual situation.
D. Solder spot tin is insufficient
Reasons: a. Insufficient solder paste, printing after the machine stops, blocked template opening, and bad solder paste quality. b. Solderability of bonding pads and components is poor. c. Less reflux time.
Solution: a Increase the thickness of the template, increase the printing pressure, and check whether the template is blocked when the machine is restarted after shutdown. The opening of the template used for lead soldering tin shall be greater than or equal to 100% of the pad when the design allows. b. Select pads and components with good solderability. c. Increase the return time.
E. False soldering
Causes: a. Poor solderability of components and pads. b. The reflow welding temperature and heating rate are improper. c. The printing parameters are incorrect. d. After printing, the stagnant time is too long, and the activity of solder paste becomes poor.
Solution: a. Strengthen the screening of PCB and components to ensure good welding performance. B. Adjust the reflow temperature curve. c. Change the pressure and speed of the scraper to ensure good printing effect. d. Solder paste shall be reflowed as soon as possible after printing.
F. Cold welding
(The surface of the welding spot is dark and rough, and there is no fusion with the object to be welded.)
Cause: a. The heating temperature is not suitable. b. The soldering tin is deteriorated. c. The preheating time is too long or the temperature is too high.
Solution: a Adjust the reflux temperature curve according to the curve reference provided by the supplier, and then adjust according to the actual situation of the products produced. b. Replace the solder paste. c. Check whether the equipment is normal and correct the preheating conditions.
G. Wicking phenomenon
This problem is rarely described in previous documents, because there are not many problems with Sn/Pb solder paste, but it often occurs when using lead-free solder paste.
Cause: The wetting and expansion rate of lead-free solder paste is lower than that of lead solder paste. The reason for wicking phenomenon is generally believed to be that the thermal conductivity of the component pin is high, the temperature rises rapidly, so that the solder preferentially wets the pin. The wetting force between the solder and the pin is much greater than that between the solder and the pad. The pin's upwarping will further aggravate the wicking phenomenon. In infrared reflow soldering, the organic flux in PCB substrate and solder is an excellent absorbing medium for infrared, while the pin can partially reflect infrared. In contrast, solder is preferentially melted. Its wetting force with the pad is greater than that between solder and its pin, so the solder will not climb up along the pin. On the contrary, solder will climb up along the pin.
Solution: During reflow soldering, the SMA shall be fully preheated before being put into the reflow furnace, and the solderability of PCB pad shall be carefully checked and guaranteed; Coplanarity of soldered components cannot be ignored, and components with poor coplanarity cannot be used in production.
H. IC pin open circuit/faulty soldering
It is a common welding defect that some IC pins have faulty soldering after welding.
Reason: a The coplanarity of components is poor, especially QFP components. Due to improper storage, the pin deformation is sometimes difficult to find (some SMT machines do not have the coplanarity check function). b. It is because of poor solderability of the pins, yellowing of the pins and long storage time. c. The solder paste is not active enough and the metal content is low. The metal content of solder paste used for QFP device welding is not less than 90%. The fourth is that the preheating temperature is too high, which causes oxidation of the parts and poor weldability. Fifthly, the opening size of the formwork is small and the tin content is not enough, so corresponding solutions are made for the above problems.
1. Solder bead
Solder bead formation is a special phenomenon when solder paste and SMT processing technology are used. To put it simply, solder bead formation refers to those very large solder balls with (or without) small solder balls stuck on them, which are formed around components with very low feet, such as chip capacitors. Solder bead formation is caused by flux exhaust, which exceeds the cohesive force of the flux in the preheating stage. The exhaust promotes the formation of solder paste particles under the low gap elements. When the solder paste is melted during soft melting, it emerges again from the elements and coalesces.
Reasons: a. The thickness of the printed circuit is too high; Solder joints and components overlap too much. b. Too much solder paste is applied under the element; The pressure for placing the element is too high. c. The temperature rises too fast during preheating; The preheating temperature is too high. d. Components and solder pastes are affected with moisture; The activity of the flux is too high; Too fine welding powder or too much oxide. e. Too much solder paste slump.
The solution is to change the pore shape of the template so that there is less solder paste between the low leg support component and the solder joint.