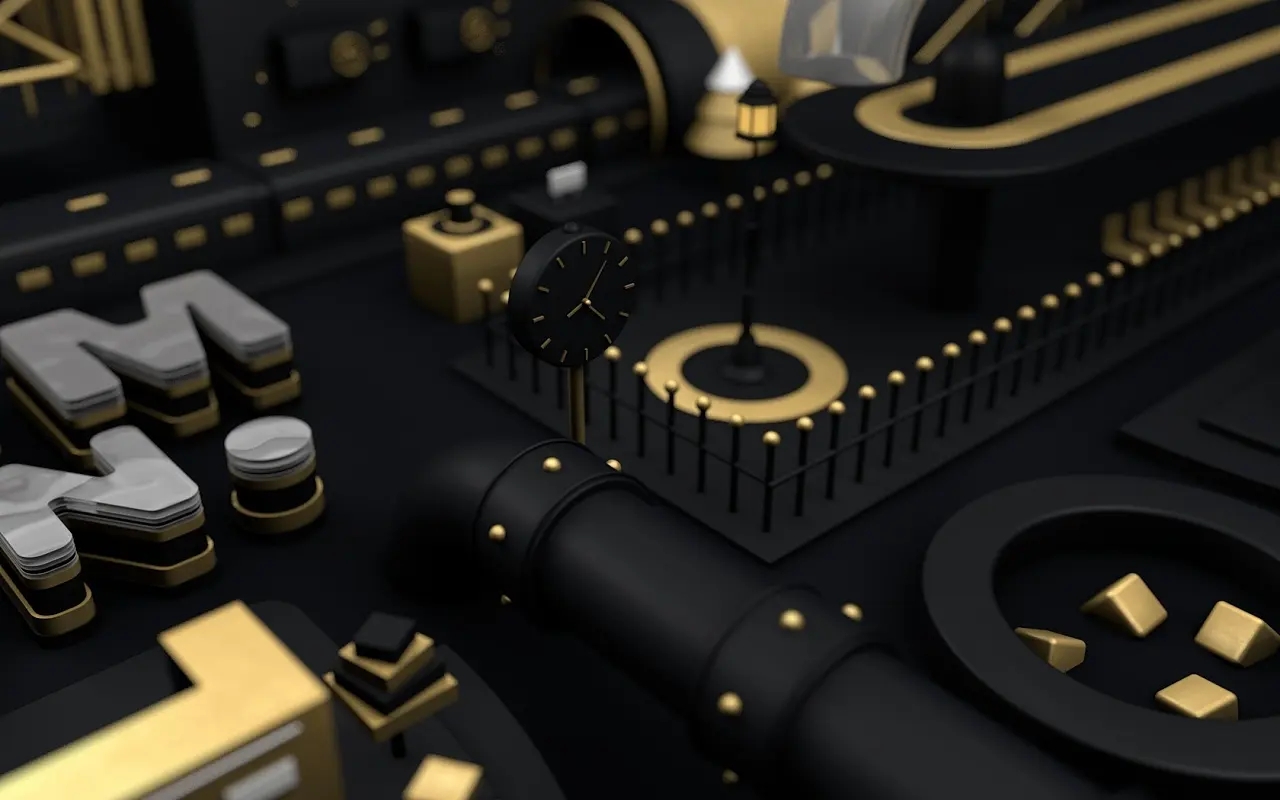
Cause Analysis and Prevention of PCBA Assembly Explosion -- Measures to Prevent Plate Explosion
PCBA processing is to connect various electronic components on PCB board through surface mount (SMT), plug-in (DIP) and other electronic assemblies. PCBA process flow mainly includes SMT, AOI, DIP, FCT testing and other processes. Due to the size difference of electronic components, there will be different processes and requirements in assembly and insertion. The assembly density of PCBA is relatively high, and the small size and light weight of electronic products also have certain changes and requirements in mounting. The reliability, seismic resistance and excellent weldability of the products have high requirements for the hardware and software facilities of PCBA processing.
The key to solve the problem is to reduce the moisture absorption of printed boards during the manufacturing, storage and use of printed boards. To this end, there are the following measures:
1. PCB packaging and storage
After the PCB with high CTI value is made, the circuit board manufacturer shall bake and dehumidify the PCB in the baking process, and then use two times of high vacuum double-layer film packaging to increase the sealing of PCB packaging. Finally, desiccant shall be placed in the large package.
The packaged PCB storage shall be stored in a room temperature and low humidity environment, and placed on the platform or appropriate rack in the original packaging form. Avoid heavy pressure and deformation of plates caused by improper storage. The storage period is 3 months.
The PCBA assembly manufacturer shall check whether the packaging of such PCB incoming materials is intact, and confirm whether the shelf life and the status of the humidity card in the inner packaging meet the requirements. Prevent the use of overdue PCB.
2. PCBA board production
First, the drying process of PCB light plate shall be conducted for dehumidification before mounting, and then put into production to complete mounting - inserting - testing - packaging and shipping. The entire production process is required to be completed within one week in the production plan.
The temperature curve of reflow welding and wave soldering shall be set according to their operation instructions. The preheating rate cannot be too fast. Set the peak temperature to no more than 245 ℃. The higher the temperature is, the greater the risk of plate bursting is. For repair welding by manual welding, use a temperature controlled soldering iron, set the temperature at 350 ℃, and control the welding time at 2~3s to prevent local overheating and potential defects.
For PCBA production with CTI>600, the key to prevent bursting is to do a good job of prevention and quality monitoring. Trace the production management of PCB with CTI>600. Production management of PCB with CTI>600. They are the foundation stone to prevent explosion.
In addition, the control of thermal stress in PCBA assembly and production can completely reduce or even eliminate the influence of thermal stress factors, which is the cause of bursting, and can completely reduce or even eliminate the occurrence of bursting.