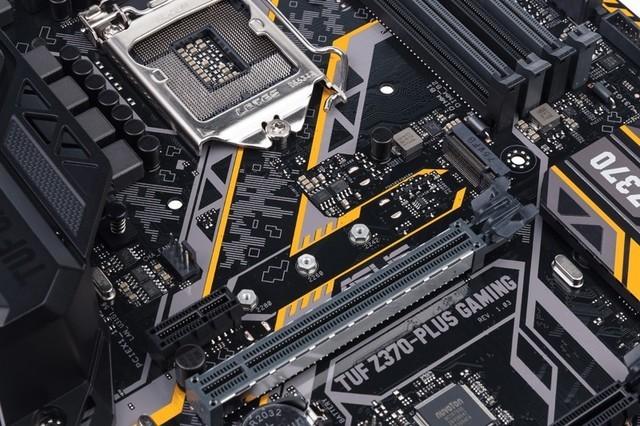
Manual inspection during PCBA assembly
PCBA processing is to connect various electronic components on PCB board through surface mount (SMT), plug-in (DIP) and other electronic assemblies. PCBA process flow mainly includes SMT, AOI, DIP, FCT testing and other processes. Due to the size difference of electronic components, there will be different processes and requirements in assembly and insertion. The assembly density of PCBA is relatively high, and the small size and light weight of electronic products also have certain changes and requirements in mounting. The reliability, seismic resistance and excellent weldability of the products have high requirements for the hardware and software facilities of PCBA processing.
At present, there are many kinds of testing technologies used in the field of electronic assembly testing, such as Manual Visual Inspection (MVI), In Circuit Tester (ICT), Automatic Optical Inspection (AOI), Automatic X-ray Inspection (AXI), Function Tester (FCT), etc.
They can be classified into two categories according to whether PCBA is powered on: one is electrical testing technology, the other is non electrical testing completion, and they can also be divided into two categories according to whether PCBA is in contact with testing equipment: one is contact testing completion, and the other is non-contact testing technology.
Manual visual MVI
Manual visual test is to confirm the mounting, inserting and welding materials of components on PCBA board through human visual comparison. Look at the goods with the operator's eyes, supplemented by a magnifying glass and a microscope. This technology is one of the oldest and most widely used online testing methods.
However, with the application and development of microelectronic surface mount technology (SMT processing), electronic products are developing towards thin and light miniaturization, and the density of printed board assemblies (PCBA) is becoming higher and higher with the continuous miniaturization of components. The secret script plug-in components block the vision of each other, as well as the micro encapsulation (0201), "invisible" solder joints (such as BGA, CSP and flip chip assembly FCA) that have been widely used in recent years, and the manual visual method of "checking words and colors" is no longer available to the naked eye to ensure the quality of PCBA processing.
It was once conducted by four experienced inspectors to inspect the quality of solder joints of the same board (moderately complex circuit board, such as a single panel with 300 components and 3500 nodes) for four times. The results showed that the first inspector found 44% of the defects, the second inspector and the first inspector had 28% consistency, the third inspector and the first two had 12% consistency, and the fourth inspector and the first three had only 6% consistency. This test exposes the subjectivity of manual visual inspection, which is neither reliable nor economical. At present, in the co processing and manufacturing, the manual visual testing method is only used as a supplementary auxiliary method.