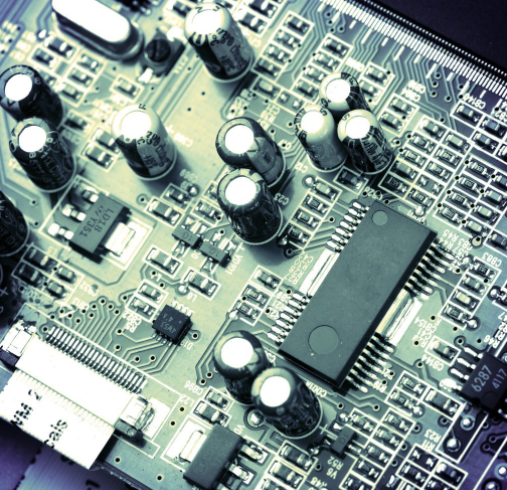
SMT module side bracket or turnover and distribution technology
Cause SMT chip processing module stands up or turns over
The SMT wafer processing module stands and turns over on the side means that the module is connected to the corresponding pad of the PCB, but the module rotates 90 ° or 180 ° laterally, and then stands laterally. Turning over means that the reverse side of the SMT wafer component faces up and the front side faces up. down
What is the reason for the two phenomena of SMT wafer processing module standing and turning sideways?
1. In the SMT placement process, the component thickness is set incorrectly, or the PCB pad is not contacted and is put down, which is easy to cause side standing or overturning.
2. When picking up the SMT mounter, the pressure is too high, causing the feeder to vibrate, which will overturn the components in the next cavity of the braided belt.
3. The vacuum of the tip mounter suction nozzle is opened or closed too early, causing the parts to stand or turn over laterally.
4. Wear or partial blockage of the tip mounter suction nozzle will also cause the parts to stand up or turn over.
Circuit board
5. Seriously deformed PCB board with a dent of more than 0.5mm will also cause the SMT chip assembly to stand up and turn over
The reasons for standing and turning on the side are roughly as described above. SMT wafer processing plants should pay more attention to these problems to ensure processing quality.
SMT dispensing technology
1. Needle size
In fact, the inner diameter of the needle should be 1/2 of the diameter of the dispensing point. In the dispensing process, the dispensing pin should be selected according to the size of the pad on the PCB: for example, the pad sizes of 0805 and 1206 are similar. The same type of pins can be selected, but different pins must be selected for pads with large differences, so as to ensure the quality of glue spots and improve production efficiency.
2. Distance between needle and PCB board
Different dispensers use different needles, and some needles stop to a certain extent (such as CAM/ALOT5000). The distance between the needle and PCB shall be calibrated at the beginning of each work, i.e. Z-axis height calibration.
3. Dosage
According to work experience, the diameter of the glue point shall be half of the pad spacing, and the diameter of the repaired glue point shall be 1.5 times of the glue point diameter. Through this kind of pipe, it can ensure that there is enough glue to bond the parts and avoid excessive glue impregnating the gasket. The amount of glue to be distributed is determined by the rotation time of the screw pump. In practice, the rotation time of the pump should be selected according to the production conditions (room temperature, glue viscosity, etc.).
4. Distribution pressure (back pressure)
The currently used glue applicator uses a screw pump to supply the glue needle, and the hose bears the pressure to ensure that sufficient glue is supplied to the screw pump. If the back pressure is too high, the glue will overflow and the amount of glue will be too much; If the pressure is too low, the glue will leak intermittently, resulting in defects. The pressure shall be selected according to the glue of the same quality and the working ambient temperature. High ambient temperature will reduce the viscosity of glue and improve its fluidity. At this time, it is necessary to reduce the back pressure to ensure glue supply, and vice versa.
5. Glue temperature
Generally speaking, the epoxy resin adhesive shall be stored in the freezer at 0-50 ℃ and taken out 1/2 hour before use to make the adhesive fully meet the working temperature. The operating temperature of glue shall be 230C-250C; The ambient temperature has a great influence on the viscosity of glue. If the temperature is too low, the bonding point will become smaller and wire drawing will occur. When the ambient temperature difference is 50 ℃, the dispensing amount will change by 50%. The ambient temperature shall be controlled. At the same time, the ambient temperature should also be guaranteed. Small glue spots are easy to dry and affect the adhesion.
6. Glue viscosity
The viscosity of glue directly affects the quality of glue. If the viscosity is high, the glue point will become smaller, even wiredrawing; If the viscosity is low, the glue point will become larger, which may contaminate the mat. In the process of gluing, select reasonable back pressure and gluing speed for glue with different viscosity.
7. Curing temperature curve
For the curing of glue, the SMT manufacturer generally gives the temperature curve. In practice, it should be possible to use higher temperatures for curing, so that the glue has sufficient strength after curing.
8. Bubble
The glue must be free of bubbles A little stinginess will lead to many PCB pads without glue; Every time the intermediate hose is replaced, the air at the connector should be drained to prevent runaway