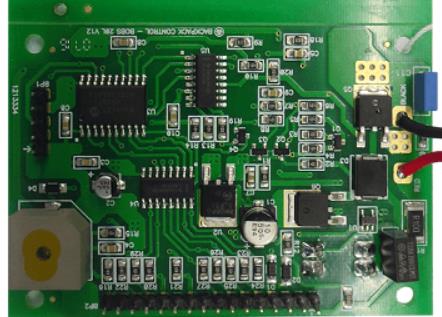
SMT automatic solder paste printer parameter setting adjustment
Solder paste printer is located in SMT production, marking and printing solder paste on PCB pad Therefore, the printing quality of solder paste printer is directly related to the quality of PCB placement and reflow Industry insiders believe that the pass rate of PCBA reflow soldering is 80% because of solder paste printing, so the printing of solder paste printer is very important Good printing can not only improve productivity and efficiency, but also reduce costs
There are many factors that affect the printing quality of solder paste printer. Printing parameter settings can easily lead to reduction of tin number, increase of tin number, continuous tin number and even sharpening. Let me share with you the process parameter adjustment of SMT automatic solder paste printer.
1. Printing clearance of solder paste printer
Circuit board
The printing gap is the distance between the mold and the printed circuit board, which is related to the residual amount of solder paste With the increase of distance, the amount of solder paste increases, which is usually controlled at 0-0.05mm
2. Printing speed
Printing speed is closely related to the viscosity of solder paste. The slower the printing speed is, the greater the viscosity of solder paste is. The faster the printing speed is, the smaller the viscosity of solder paste is. The speed is fast, the time for the scraper to pass through the mold opening is relatively short, and the solder paste cannot completely penetrate into the opening, which may easily lead to printing defects such as insufficient solder paste molding or missing printing.
3. Angle between scraper and template
The smaller the angle between the scraper and the mold, the greater the downward pressure. The solder paste is easier to inject into the grid, but it is also easier to squeeze the solder paste onto the bottom of the mold, causing the solder paste to adhere. Typically 45 to 60 degrees.
4. Scraper pressure
The scraper pressure actually refers to the depth at which the scraper drops. If the pressure is low, the amount of solder paste leaking into the window is small, and the amount of solder on the PCB is insufficient. Too much pressure will lead to too thin solder paste printing. The ideal printing speed and pressure should only scrape the solder paste off the mold surface.
5. Scraper width
If the scraper is too wide relative to the PCB, more pressure and more solder paste are required, which will lead to waste of solder paste. Generally, the width of the scraper is PCB length plus 50mm, and the scraper should be placed on the metal template.
6 Demoulding speed
After the solder paste is printed, the instant speed of the mold leaving the PCB is the demoulding speed, which is a parameter related to the printing quality. It is most important in fine pitch and high-density printing. The adhesive force between solder paste and bonding pad is very small. This part of solder paste sticks to the bottom of the mold and the wall of the opening, resulting in printing defects such as insufficient printing and tin collapse. When the separation speed slows down, the viscosity and cohesion of the solder paste are large, and the solder paste is easy to leave the mold opening wall. The demoulding speed is generally set as 0.3-3mm/s, and the demoulding distance is generally 3mm.
7. Cleaning pipes and cleaning frequency
During printing, clean the bottom of the mold to remove its accessories to prevent PCB contamination Anhydrous ethanol is usually used as cleaning agent The cleaning frequency set by the solder paste printer should be cleaned every 8-10 printing times Spacing, high density and higher cleaning frequency ensure printing quality. Wipe it manually with dust-free paper every 30 minutes