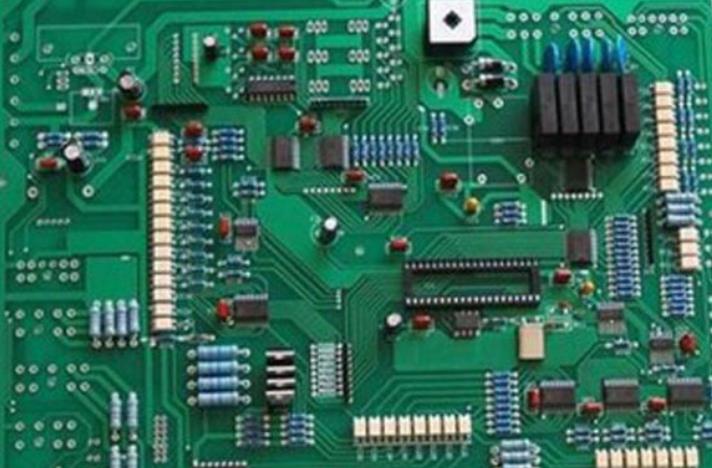
How to select and use PCB cleaning agent?
There are three main methods for bonding or attaching contaminants and components to PCB components They are bonds between molecules, also known as physical binding; The bond between atoms is also called chemical bond; Pollutants are embedded in the data in the form of particles, such as welding masks or electroplating deposits, which are called "stimulants"
The center of the cleaning mechanism is to destroy the binding force of chemical or physical bonds between pollutants and PCB printed circuit board, so as to separate pollutants from components. Because this process is an endothermic reaction, it is necessary to supply to achieve the above purpose.
SMT chip processing
Select appropriate solvent to provide energy through the dissolution reaction and saponification reaction between pollutants and solvents, which can destroy the binding force between them and dissolve pollutants in the solvent to remove pollutants.
In addition, specific water can be used to remove contaminants left on the part by water-soluble flux.
Circuit board
Because PCB printed circuit board components are polluted differently after welding, the types of pollutants are also different, and different products have different requirements on the cleanliness of cleaned components, so a variety of cleaning agents can be used. So, how to choose the right cleaner? The following scientific and technical personnel of smt processing plant will introduce some basic requirements for cleaning agent.
Humidity
For the solvent to dissolve and remove the contaminants on the shape memory alloy, it is first necessary to wet the contaminated PCB, expand and wet the contaminants.
The humidity angle is the main factor determining the humidity. The best cleaning condition is spontaneous expansion of PCB. The condition for this is that the wet angle is close to 0 °.
Capillary effect
Wet solvents may not ensure effective removal of contaminants. The solvent must be easy to penetrate, enter and exit these narrow spaces, and can be recycled repeatedly until the pollutants are removed. That is, the solvent needs to have a strong capillary effect so that it can enter these dense gaps. Capillary permeability of commonly used cleaning agents. It can be seen that the capillary permeability of water is the largest, but its surface tension is large, which is difficult to discharge from the gap, resulting in a low exchange rate of cleaning water and difficult to effectively clean. Although the capillary permeability of chlorinated hydrocarbon mixture is low, the surface tension is also low. This summary and consideration of these two functions. This solvent has a good cleaning effect on component pollutants.
viscosity
The viscosity of solvent is also an important function affecting the effective cleaning of solvent. In general, under the same other conditions, the viscosity of the solvent is high, while the connectivity in the SMA gap is low, which means that more force is required to discharge the reagent from the gap. In this case, the lower solvent helps it to complete multiple exchanges in SMD seam originals.
concentrated
Where other requirements are met, components shall be cleaned with high-density solvents. This is because during the cleaning process, when the solvent vapor condenses on the components, gravity helps the condensed solution move downward, improving the cleaning quality. In addition, the high density of the solution is also conducive to reducing its emissions to the atmosphere, thereby saving data and reducing operating costs.
Boiling point temperature
The cleaning temperature also has some influence on the cleaning power. In most cases, the solvent temperature is controlled at or near its boiling point. Different solvent mixtures have different boiling points, and the change of solvent temperature mainly affects their physical functions. Steam condensation is an important part of the cleaning loop. Higher temperature steam can be obtained by increasing the boiling point of solvent, and higher steam temperature will lead to more steam condensation, which can remove many pollutants in a short time. This connection is most important in the wave soldering and cleaning system of the tandem conveyor, because the speed of the detergent belt must be consistent with that of the wave soldering belt.
Solubility
When cleaning the shape memory alloy, due to the very small distance between the components and the base plate, between the components and between the input/output terminals of the components, only a few solvents can contact the pollutants under the equipment. In this case, it is necessary to select a solvent with high solubility, especially when cleaning needs to be completed within a limited time, such as in the online conveyor belt cleaning system. However, it should be noted that solvents with high solubility are also highly corrosive to the parts to be cleaned. Rosin based flux is used for most solder pastes and double wave soldering. In this regard, when comparing the solubility of various solvents, special attention should be paid to the residues of rosin based flux.
Ozone destruction factor
With the continuous progress of society, people's awareness of environmental protection has been growing. In this regard, when evaluating the ability of cleaning agents, the degree of destruction to the ozone layer should also be considered. Therefore, the concept of ozone destruction factor (ODP) was introduced, which is now based on the ozone destruction factor of CFC-113 (3chloroethane 3oxide), namely ODPCFC-113=1.
Minimum constraint
The minimum constraint value represents the maximum limit value that the human body can bear when contacting with the solvent, also known as the exposure limit. Operators shall not exceed the minimum limit of solvent in daily work.
The above is the selection of detergent PCBA patch treatment plant In addition to the above mentioned functions, economy and other factors, operability and compatibility with equipment shall also be considered