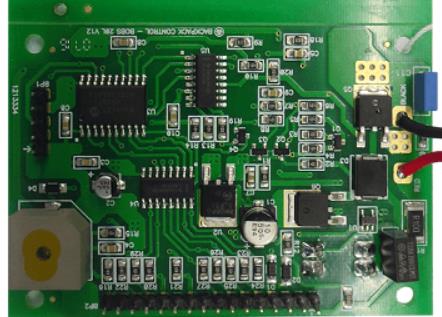
An important part of visual inspection of surface mount components
1. The influence of foreign matters on the lens SMT mounter, the glass lens above the diaphragm, is used to prevent dust from entering the aperture and affecting the intensity of the light source. However, if there are foreign matters such as dust or parts on the glass lens, it will affect the intensity of the light source Low, low gray value This leads to low recognition. Please pay attention to cleaning the lenses and all kinds of lenses
2. The reflector acts on the backlight When there is dust on the reflector, the intensity of the light source reflected to the camera will be reduced, and the gray value will also be reduced, resulting in poor identification and loss of components. Therefore, SMT sticker and film applicator should pay attention to that the reflector is a part that needs to be wiped regularly
3. Affected by the aperture light source, the intensity of the aperture light source will gradually decrease after a period of use, because the intensity of the light source is proportional to the gray value converted by the solid-state camera. The larger the gray value, the closer the digital image is to the view observed
Circuit board
So the gray value in the machine will not decrease with the decrease of the light source intensity Only through regular calibration and testing, the gray value will be the same as the intensity of the light source In direct proportion, when the intensity of the light source is too weak to identify the components, the bulb needs to be replaced
4. The SMT catalog parameters are set incorrectly. This is usually due to inconsistent part shape during refueling. The identification parameters need to be rechecked and set again. Inspection items include part shape and size. The solution is to let the vision system "learn" the part shape again, and the system will generate the similarity from the ground. CAD is described comprehensively, and this method is fast and effective. In addition, if the dimensional consistency of the incoming materials is not good, the tolerance can be added appropriately.
5. Effect of suction nozzle. When the backlight is recognized, if the shape of the nozzle is larger than the contour of the device, the contour of the nozzle will appear in the image. The identification system regards the contour of the suction nozzle as part of the component, which will affect the identification of SMT components. Centring. We can deal with the specific reasons:
a. If the outside diameter of Yamaha nozzle is larger than the equipment size, switch to the nozzle with smaller outside diameter.
b. The position deviation of the suction nozzle causes the contour of the suction nozzle to extend to the contour of the equipment to adjust the deviation of the material level. HSP4796L has the function of automatically correcting the suction position of components. The average error is calculated by continuously measuring the suction position of components, and the correction value is automatically generated for compensation. The correction values are stored in the FEED (B) OFFET and SMT databases. The correction value automatically generated for each material level can solve the problem by clearing the deviation value of the material level where the part is located.
Through the above introduction, everyone knows that the visual inspection of SMT components is an important part of the mounter In order to avoid misplacement of data SMT during construction, it is recommended that you do a good job of machine maintenance at ordinary times!
The above is the explanation given by the editor of pcb circuit board company.
If you want to know more about PCBA, you can go to our company's home page to learn about it.
In addition, our company also sells various circuit boards,
High frequency circuit board and SMT chip are waiting for your presence again.